Another restoration - 83' 528i
Re: Another restoration - 83' 528i
Some great looking sheetmetal work there, seems you have your technique nailed down really well! Lots and lots of time and effort! Looking forward to seeing the end result!
Re: Another restoration - 83' 528i
oh to have talent like that! incredible work.
Re: Another restoration - 83' 528i
Second half of May 2020
To get more done during single paint session I started prepping my side sills so I could prime the insides.
These are some repro side sills made by Klokkerholm. It’s a pity to use repro sills on the car but the right side OEM sill is NLA. Furthermore, OEM sills don’t run full length and you’d have to buy the front and rear column as well. So these will have to do.
I could’ve just drilled some drain holes which could probably even work better as they wouldn’t get clogged as easily but I wanted to replicate the OEM look. So I made these drain holes into the sills. I just have to remember to clean them every once in a while in the future.

Front section of the sills had a few spots where metal was folded on itself.

To avoid moisture getting trapped in there I made small cuts and welded them up.
Then started to remove the primer on the inside. By sanding it down.
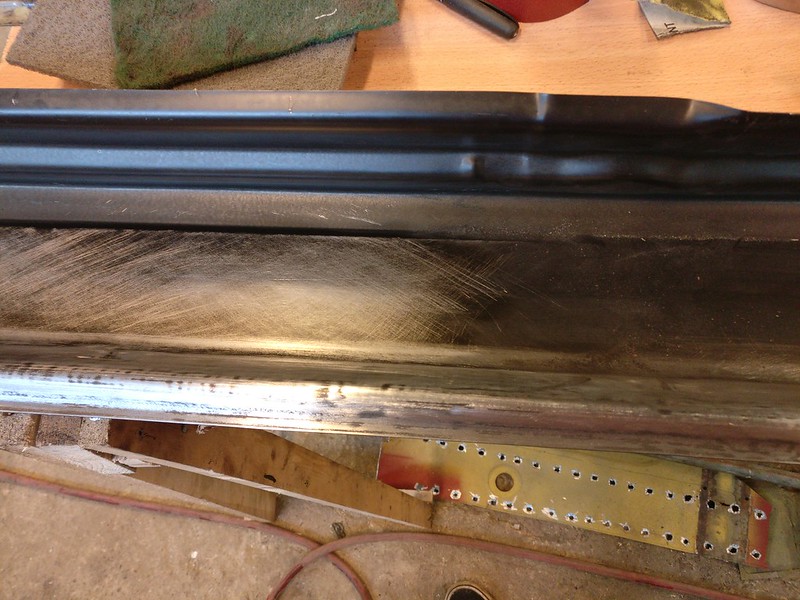
After I had wasted about one and a half hours on sanding a friend came by and asked why didn’t I just use some solvent. It took like ten to twenty minutes to get them clean using solvent. Tip: use a scouring pad dipped in solvent (instead of towel) to remove primer and prep the metal in one go.
So, (don’t quote me on the following) what I learned was that OEM parts come with some really nice quality e-coating on top of them. You do not want to remove it as it’s probably superior to anything you can put on the panel yourself, just roughen it up a little for better adhesion of the next layers. On the other hand, most repro panels come with some really crappy primer on them and you do not want it under your paint. Simple test is to use some solvent and wipe the panel with it. If some of the primer ends up on your towel then it’s not the e-coat.
I had also removed the lifting supports from the old sills. They got sandblasted and then later spot welded to the new sills at my friends workshop (no pictures).
Outer jack points were too far gone so I cut new ones out of some random brackets I got from a hardware store.

I was going to use Standox nonstop 2K primer (U7580). As this is not meant to be used on bare metal I put down a thin layer of my weld through primer. By the way, this red weld through primer (also by Standox) you see me using everywhere is awesome stuff. It’s sticks really well to the metal for a 1K primer. And what’s best, it’s available in spray cans which makes it perfect for someone like me who needs to cover a small detail every once in a while.

And then one of my friends who once was an automotive painter put some of that 2K primer on the panels and on the rear section of the car. He was going to show me some tips on using the paint gun but ended up doing everything himself.


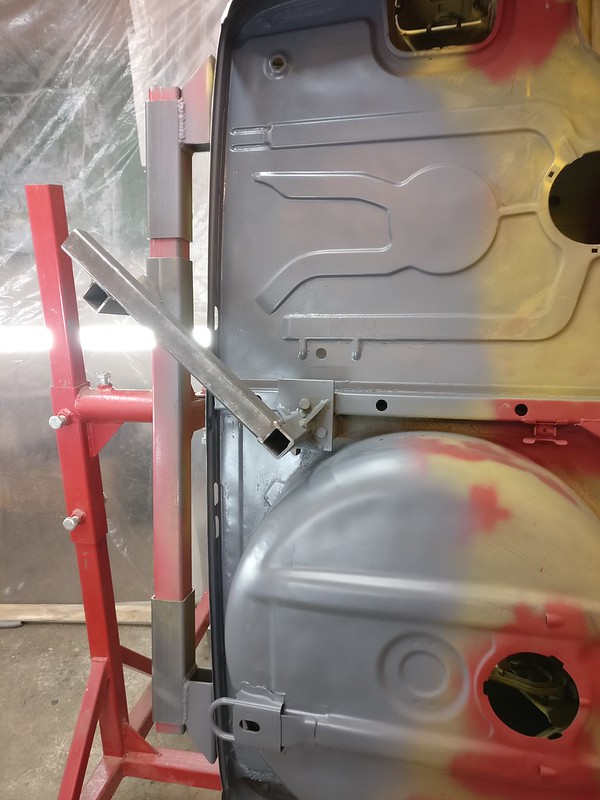
I intended to use 3M 2K panel adhesive to glue the rear valance in the corners instead of plug welding it. This would fill the gap between panels completely so no moisture gets entrapped. So I had to wait until my friend could borrow the glue gun from work.
Then I discovered this crack in my new floor panel.
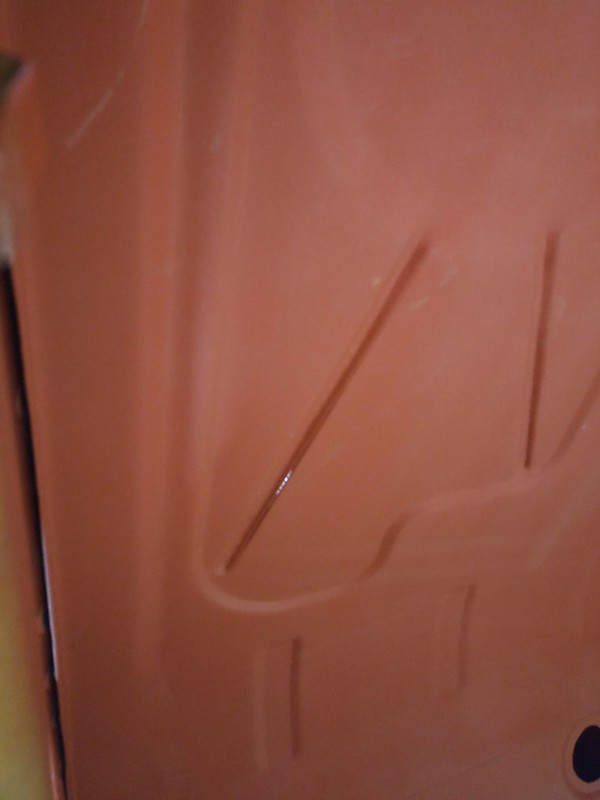

So welded it shut
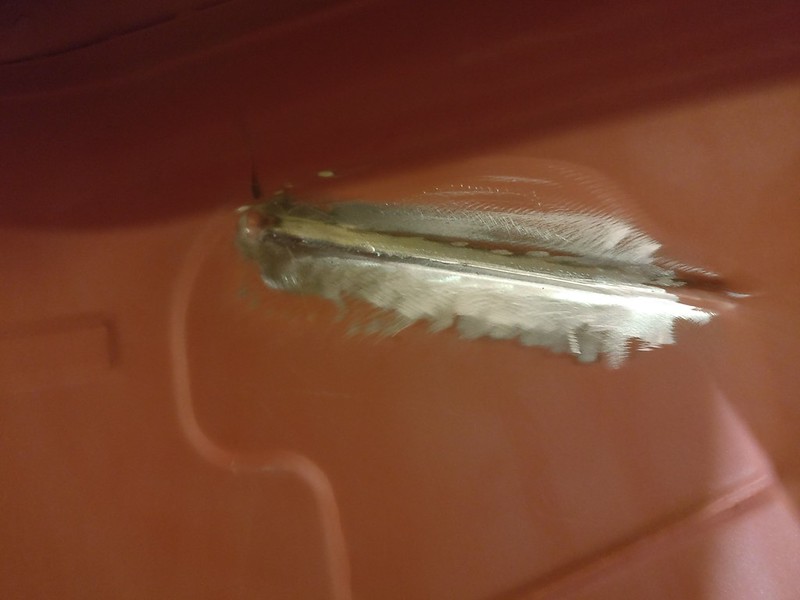
Put back one of the fuel tank brackets

And the front seat beam on the passenger side

Began to cut off the driver side sill so I could do the floors on this side while I still remembered how everything went together. This side had even more rust.

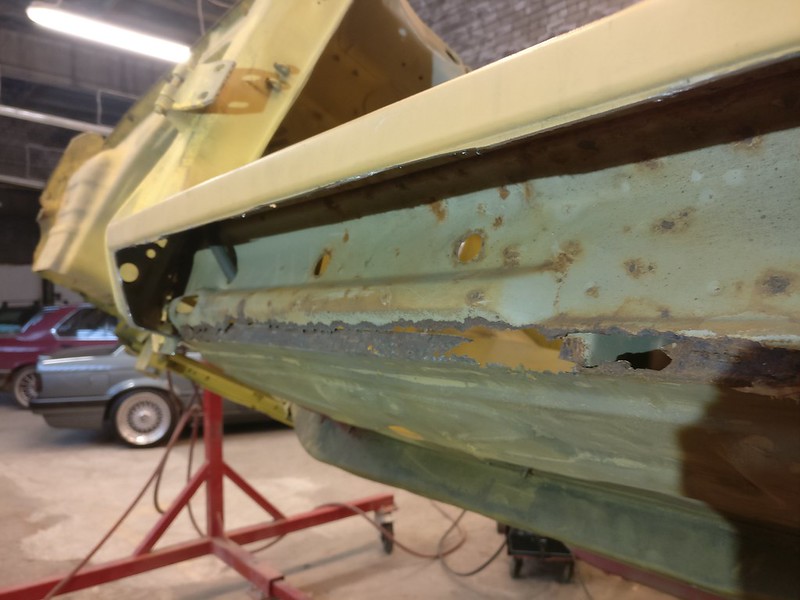

Made this to fix up the front section of inner sill.

A rusty spot on front column got fixed


And welded in the inner sill repair

Some sandwich rust here

And some more

And just like that I ended up here
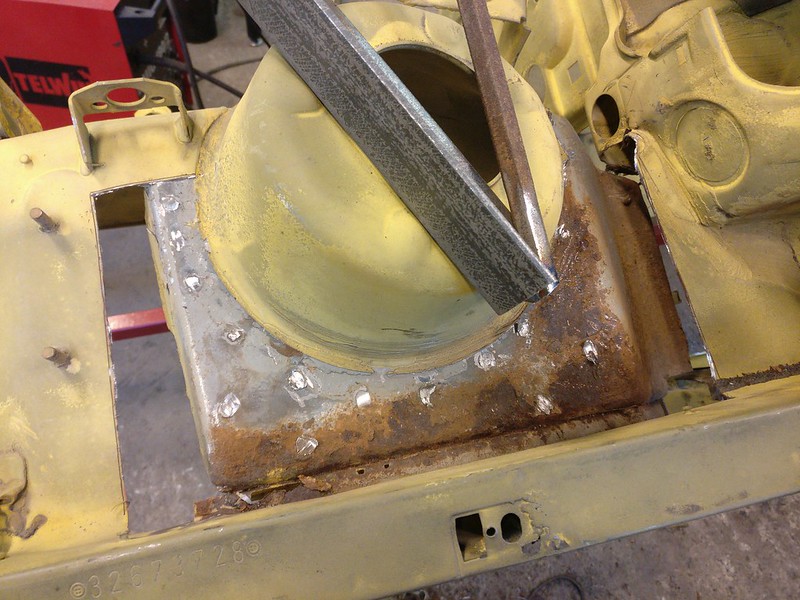
Best course of action would be to sandblast it. So I ordered myself a 75L (20 gal) sandblaster. Those have become quite affordable and it will get its fair share of use during this and any future projects.
To get more done during single paint session I started prepping my side sills so I could prime the insides.
These are some repro side sills made by Klokkerholm. It’s a pity to use repro sills on the car but the right side OEM sill is NLA. Furthermore, OEM sills don’t run full length and you’d have to buy the front and rear column as well. So these will have to do.
I could’ve just drilled some drain holes which could probably even work better as they wouldn’t get clogged as easily but I wanted to replicate the OEM look. So I made these drain holes into the sills. I just have to remember to clean them every once in a while in the future.

Front section of the sills had a few spots where metal was folded on itself.

To avoid moisture getting trapped in there I made small cuts and welded them up.
Then started to remove the primer on the inside. By sanding it down.
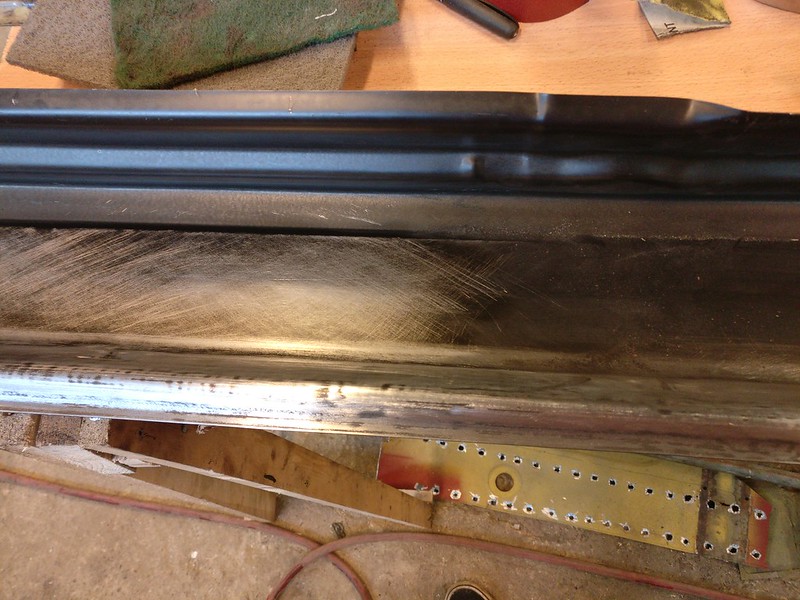
After I had wasted about one and a half hours on sanding a friend came by and asked why didn’t I just use some solvent. It took like ten to twenty minutes to get them clean using solvent. Tip: use a scouring pad dipped in solvent (instead of towel) to remove primer and prep the metal in one go.
So, (don’t quote me on the following) what I learned was that OEM parts come with some really nice quality e-coating on top of them. You do not want to remove it as it’s probably superior to anything you can put on the panel yourself, just roughen it up a little for better adhesion of the next layers. On the other hand, most repro panels come with some really crappy primer on them and you do not want it under your paint. Simple test is to use some solvent and wipe the panel with it. If some of the primer ends up on your towel then it’s not the e-coat.
I had also removed the lifting supports from the old sills. They got sandblasted and then later spot welded to the new sills at my friends workshop (no pictures).
Outer jack points were too far gone so I cut new ones out of some random brackets I got from a hardware store.

I was going to use Standox nonstop 2K primer (U7580). As this is not meant to be used on bare metal I put down a thin layer of my weld through primer. By the way, this red weld through primer (also by Standox) you see me using everywhere is awesome stuff. It’s sticks really well to the metal for a 1K primer. And what’s best, it’s available in spray cans which makes it perfect for someone like me who needs to cover a small detail every once in a while.

And then one of my friends who once was an automotive painter put some of that 2K primer on the panels and on the rear section of the car. He was going to show me some tips on using the paint gun but ended up doing everything himself.


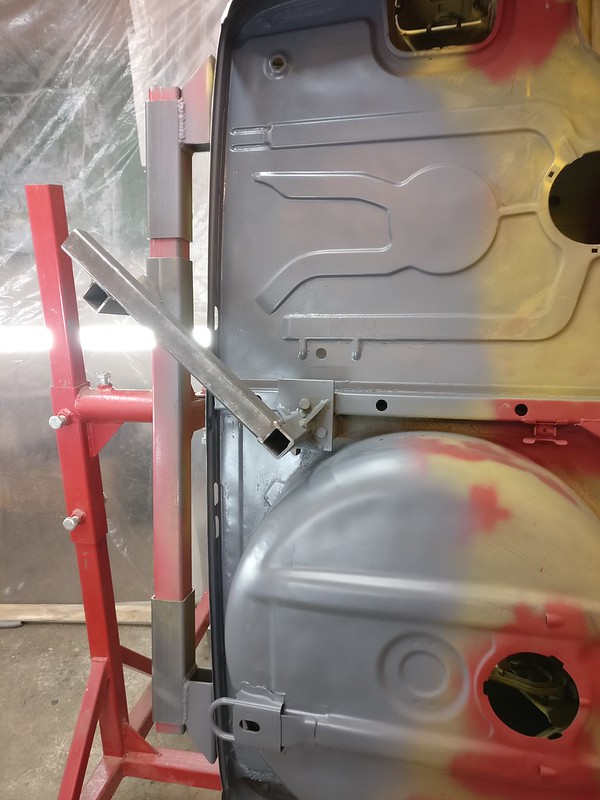
I intended to use 3M 2K panel adhesive to glue the rear valance in the corners instead of plug welding it. This would fill the gap between panels completely so no moisture gets entrapped. So I had to wait until my friend could borrow the glue gun from work.
Then I discovered this crack in my new floor panel.
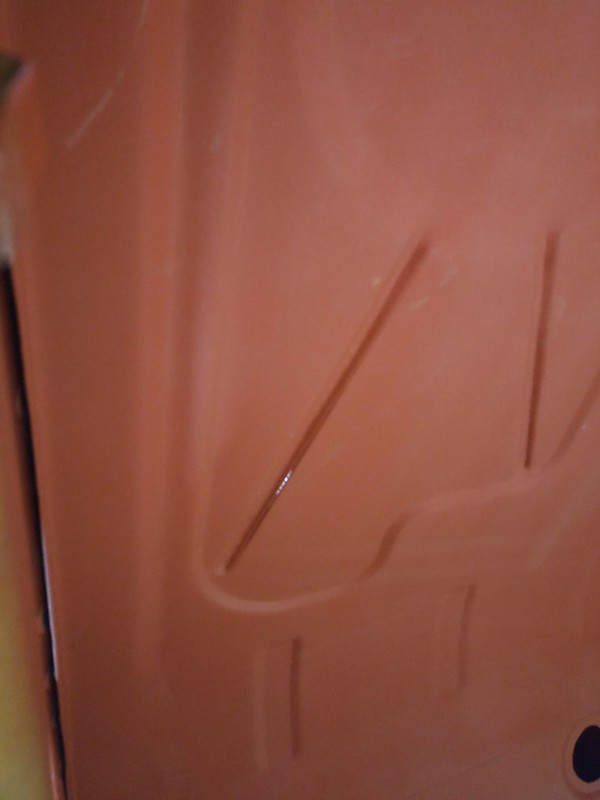

So welded it shut
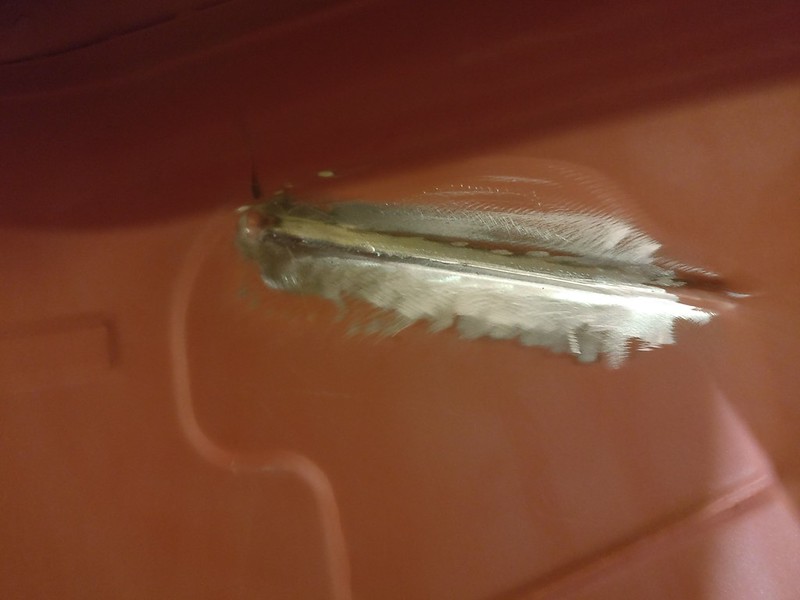
Put back one of the fuel tank brackets

And the front seat beam on the passenger side

Began to cut off the driver side sill so I could do the floors on this side while I still remembered how everything went together. This side had even more rust.

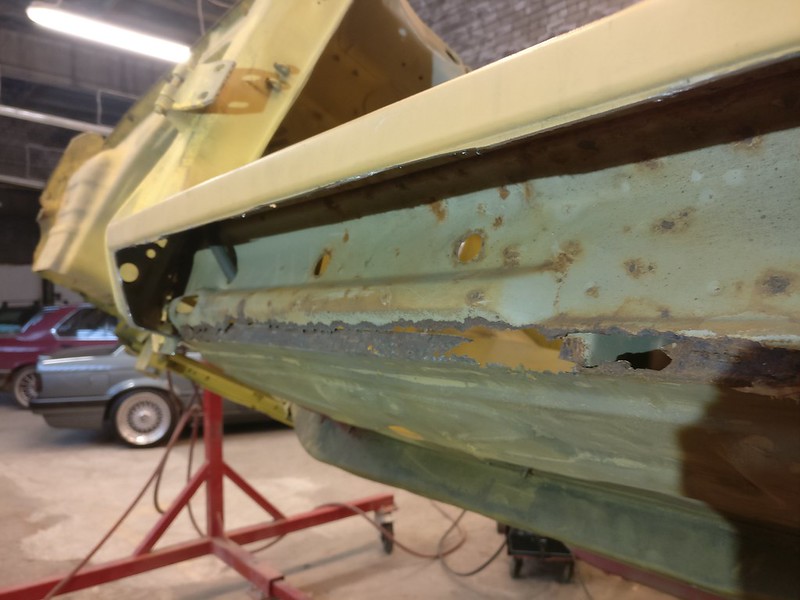

Made this to fix up the front section of inner sill.

A rusty spot on front column got fixed


And welded in the inner sill repair

Some sandwich rust here

And some more

And just like that I ended up here
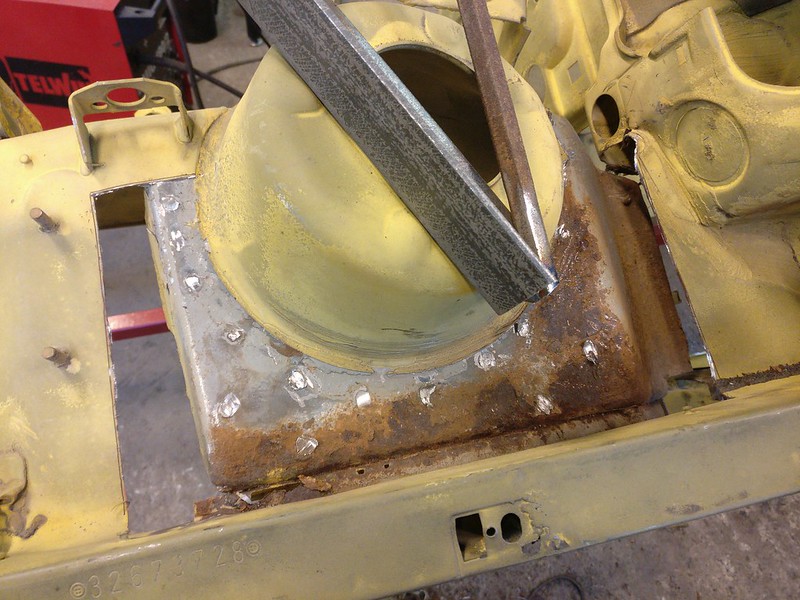
Best course of action would be to sandblast it. So I ordered myself a 75L (20 gal) sandblaster. Those have become quite affordable and it will get its fair share of use during this and any future projects.
Re: Another restoration - 83' 528i
First half of June 2020
To fix the strut tower in position while dealing with the repairs I bolted on a strut bar made of scraps and welded some temporary bars on the side

It was only reasonable to find some more rusty spots to sandblast in one go so I cut open driver’s side rear subframe mount.


Sandblaster made a quick job of removing the rust. Did also clean the rusty spots inside the side sill. I can’t find any after pictures or even a picture of the sandblaster, so you have to take my word for it.
Later, made some patches. Top of front wheel housing:
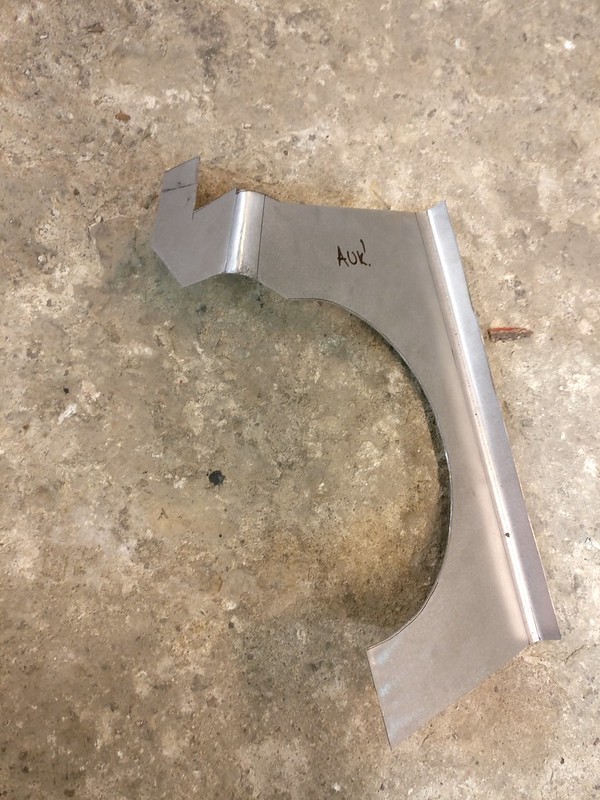

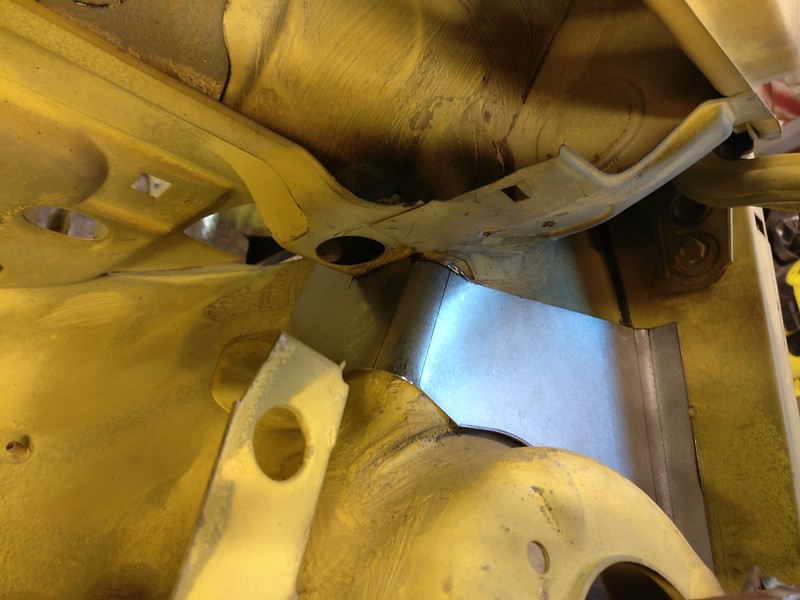
Inner panel on front column where it joins the firewall

Lower piece of firewall

And a new edge for the driver’s floor panel

Passenger side tranny bracket went back on

Patched up rear subframe mount


Finally, my buddy was able to borrow the glue gun from work so it was time to fix up the rear end. First, only the middle section of the rear valance was tack welded. This kept everything lined up while still allowing to bend it away enough on the corners to shoot some adhesive between the panels.


After the adhesive had dried more tacks were made

Then seam welded between the tacks


And after some grinding and hammering I had this

I did get surprisingly little heat distortion in the weld area.
Still needed a bit more hammer and dolly action in the joint area but I was quite happy with the results.
To fix the strut tower in position while dealing with the repairs I bolted on a strut bar made of scraps and welded some temporary bars on the side

It was only reasonable to find some more rusty spots to sandblast in one go so I cut open driver’s side rear subframe mount.


Sandblaster made a quick job of removing the rust. Did also clean the rusty spots inside the side sill. I can’t find any after pictures or even a picture of the sandblaster, so you have to take my word for it.
Later, made some patches. Top of front wheel housing:
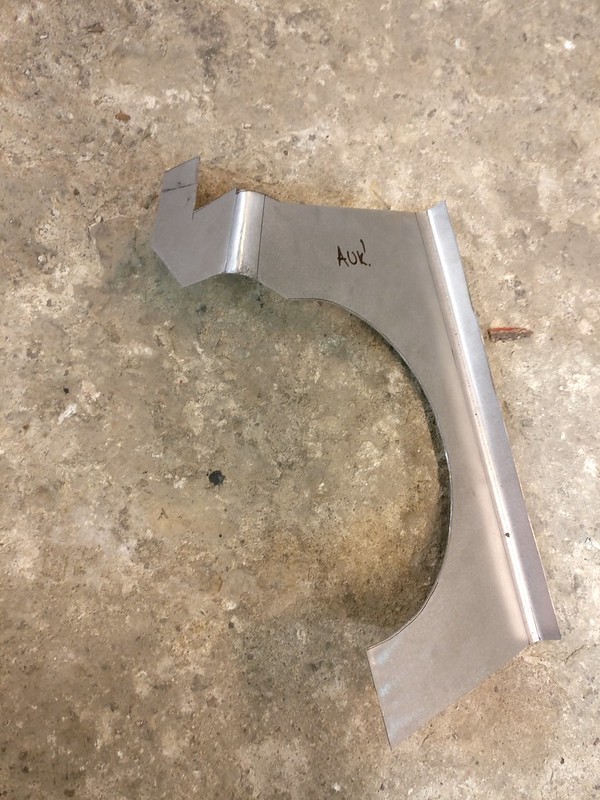

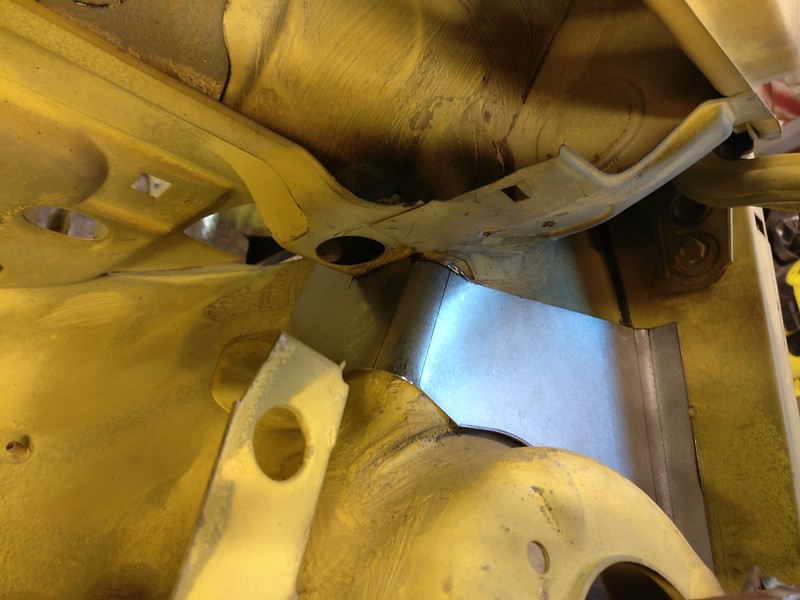
Inner panel on front column where it joins the firewall

Lower piece of firewall

And a new edge for the driver’s floor panel

Passenger side tranny bracket went back on

Patched up rear subframe mount


Finally, my buddy was able to borrow the glue gun from work so it was time to fix up the rear end. First, only the middle section of the rear valance was tack welded. This kept everything lined up while still allowing to bend it away enough on the corners to shoot some adhesive between the panels.


After the adhesive had dried more tacks were made

Then seam welded between the tacks


And after some grinding and hammering I had this

I did get surprisingly little heat distortion in the weld area.
Still needed a bit more hammer and dolly action in the joint area but I was quite happy with the results.
Re: Another restoration - 83' 528i
Second half of June 2020
It was time to weld in all the repair pieces. Not much to comment here, let the pictures do the talking.





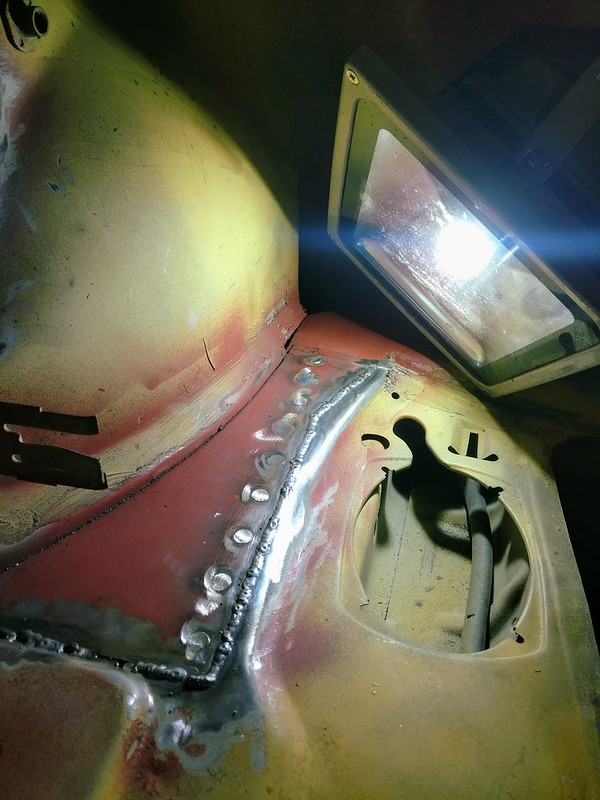



No way I can get any of my tool in there to grind down the weld so I decided to join it close to the flange. This way it gets hidden away by seam sealer later.

Cut off some of the old floor

While full of dirt the frame rail was actually in a better condition than other side. Even this rust-prone joint. Still received the same treatment as the other side.

Cleaning in progress

Then it was time to push and knock out those dents. Not sure what has happened here. Is it damage from lifting the car or has it crashed onto a rock in the past.
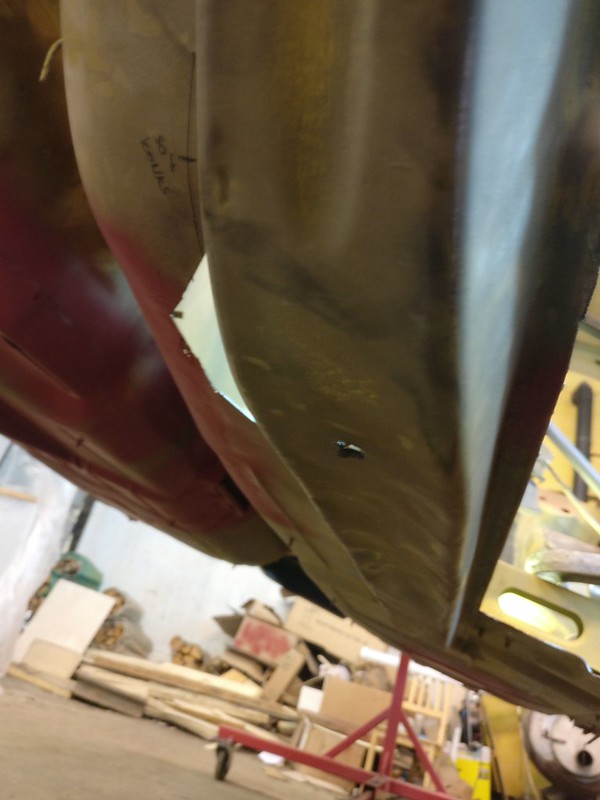
Didn’t bother with smaller dents and kinks but was able to get it pretty straight (after pictures in upcoming posts).
It was time to weld in all the repair pieces. Not much to comment here, let the pictures do the talking.





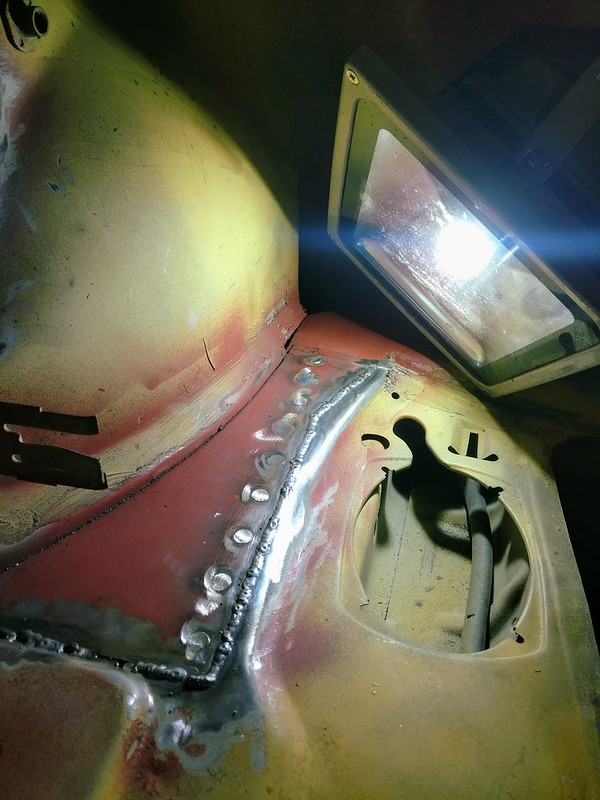



No way I can get any of my tool in there to grind down the weld so I decided to join it close to the flange. This way it gets hidden away by seam sealer later.

Cut off some of the old floor

While full of dirt the frame rail was actually in a better condition than other side. Even this rust-prone joint. Still received the same treatment as the other side.

Cleaning in progress

Then it was time to push and knock out those dents. Not sure what has happened here. Is it damage from lifting the car or has it crashed onto a rock in the past.
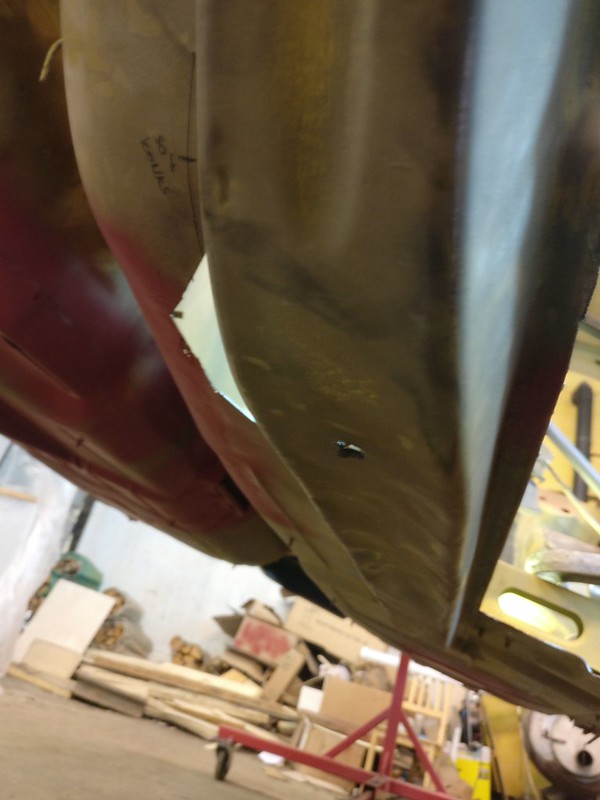
Didn’t bother with smaller dents and kinks but was able to get it pretty straight (after pictures in upcoming posts).
Re: Another restoration - 83' 528i
Every post further establishes you as a hero I aspire to be. Wow.
-
- Beamter
- Posts: 9056
- Joined: Apr 13, 2006 11:18 PM
- Location: Council Bluffs, IA
- Contact:
Re: Another restoration - 83' 528i
You sir are beyond ambitious! I tip my hat to you. 

Re: Another restoration - 83' 528i
July 2020
Wrapped up the work on rear valance - some hammering on weld line and a coat of primer

Added new edge to the floor repair panel. I decided to join the firewall and floor pieces off the car to make it a bit easier. Also added some extra sheet metal to the rear of the panel (and lost the focus on my camera in the process).


This piece should fill a substantial part of that hole.

Cleaned and prepped the frame rail

Sprayed some 1K epoxy primer I had lying around on the inside and weld-through primer on the flanges of frame rail. Same was done on the other side earlier.

After a lot of frustrating hours it was finally in. Replaced a large portion of metal where the panel covers frame rail. It had ton of extra metal there and it was oil canning. I was hoping I could push it against the frame rail and make the plug welds but the metal just bulged up next to the welds. Also, you can see that the large rounded rectangle of that panel is too wide and sits too close to the frame rail so fuel and brake lines won’t both fit there any more. I’ll probably route one set of lines over that rectangle unless I come up with something better.




Front flange of the seat beam was rotten and got replaced
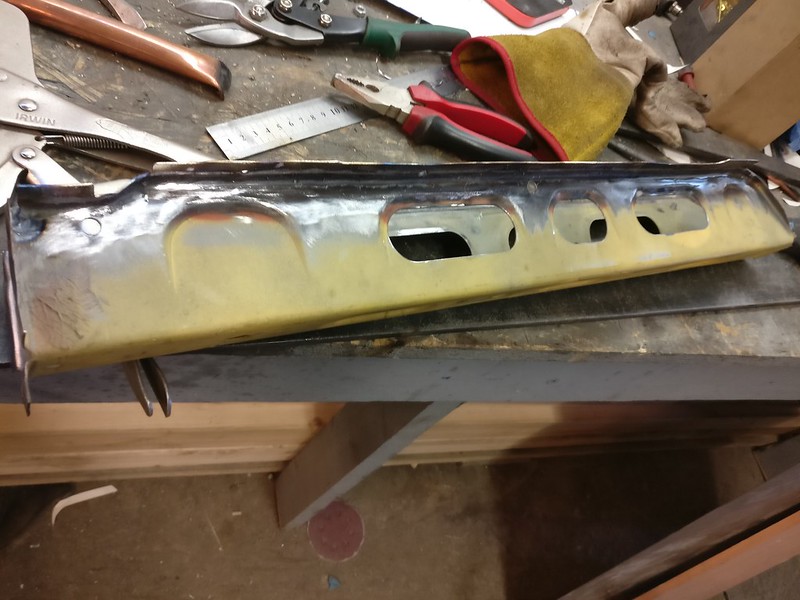
I am going to use these rivet nuts to mount brake and fuel line clips. I also tried welding them on the panel which would really give OEM look but it wasn’t easy and I don’t think it’s worth the effort. Don’t mind the damage on the rivet nut. Back then, I didn’t have correct tool yet and used some bolts, nuts and bench vise to install it.


Wrapped up the work on rear valance - some hammering on weld line and a coat of primer

Added new edge to the floor repair panel. I decided to join the firewall and floor pieces off the car to make it a bit easier. Also added some extra sheet metal to the rear of the panel (and lost the focus on my camera in the process).


This piece should fill a substantial part of that hole.

Cleaned and prepped the frame rail

Sprayed some 1K epoxy primer I had lying around on the inside and weld-through primer on the flanges of frame rail. Same was done on the other side earlier.

After a lot of frustrating hours it was finally in. Replaced a large portion of metal where the panel covers frame rail. It had ton of extra metal there and it was oil canning. I was hoping I could push it against the frame rail and make the plug welds but the metal just bulged up next to the welds. Also, you can see that the large rounded rectangle of that panel is too wide and sits too close to the frame rail so fuel and brake lines won’t both fit there any more. I’ll probably route one set of lines over that rectangle unless I come up with something better.




Front flange of the seat beam was rotten and got replaced
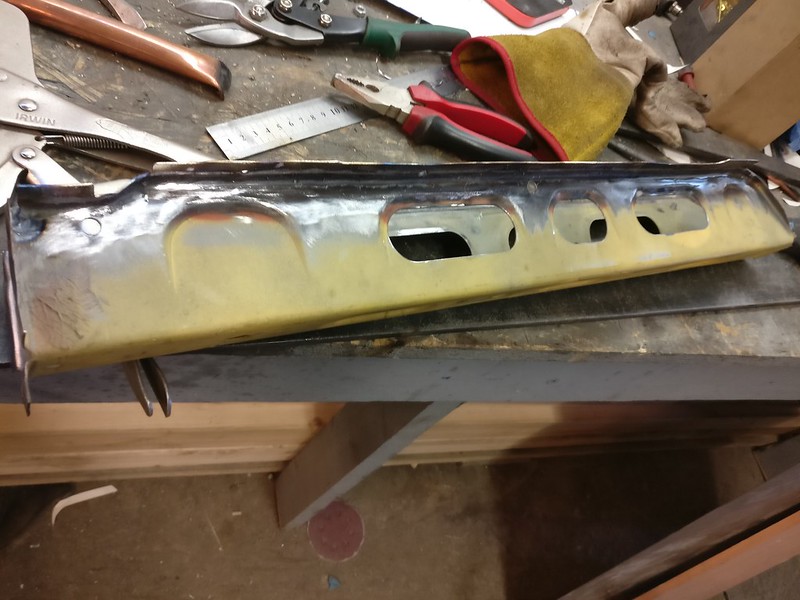
I am going to use these rivet nuts to mount brake and fuel line clips. I also tried welding them on the panel which would really give OEM look but it wasn’t easy and I don’t think it’s worth the effort. Don’t mind the damage on the rivet nut. Back then, I didn’t have correct tool yet and used some bolts, nuts and bench vise to install it.


-
- Posts: 966
- Joined: Oct 26, 2017 3:36 PM
- Location: Fleming Island FL
Re: Another restoration - 83' 528i
Most (99%- dare I say 99.9%) of us will never get this deep into the chassis. Incredible work. Thank you for documenting! Looking forward to the progress and how you approach the trim, driveline and electronics. Should keep us entertained for a while!
Re: Another restoration - 83' 528i
Not so long ago I was pretty sure I’ll never do any body/chassis work. Then this project came along, and it turns out to be a really enjoyable although time-consuming activity.Bonsaibacker wrote: Sep 13, 2020 8:32 AM Most (99%- dare I say 99.9%) of us will never get this deep into the chassis.
Early August 2020
It was time to get all the floorboards finished. After some examination I realized that there’s no need to completely remove the rear seat beam on driver’s side. End of the frame rail was in pristine condition and I could access other rusty areas without removing it.
Front beam back in place and a few patches made



A buddy gave me the idea to join this patch where the beam is. There are two shorter seam welds instead of one long weld from the factory. A small victory - almost OEM look without the need to grind the weld down.


And on with the final piece of floor board and rear section of inner sill to fill this hole.



Decided to put the sill patch in first to have better access to the weld from the inside

Followed by the floor patch




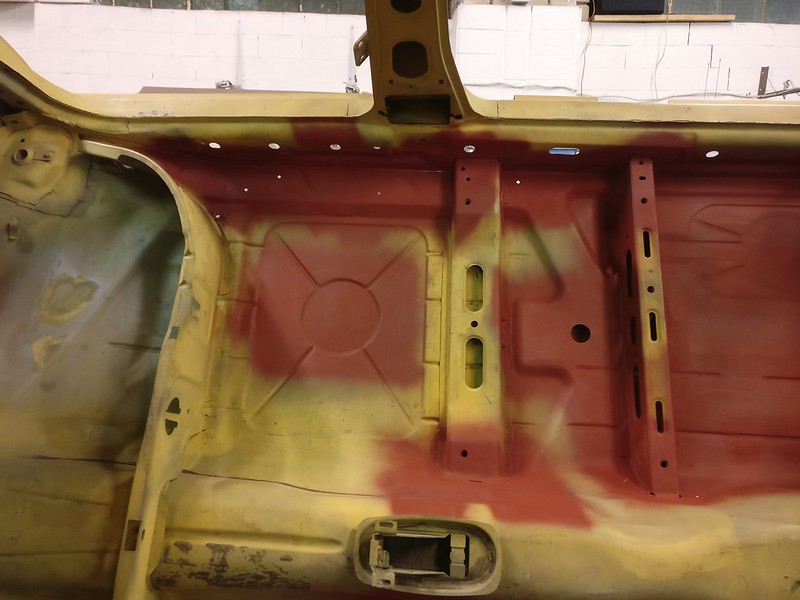
And a picture of the whole cabin to sum it up. Floorboards are done (with an exception of a few holes for rivet nuts and some other attachments).

Re: Another restoration - 83' 528i
Incredible work, thanks for posting. If you plan to install AC in the future, it is the perfect timing to drill a hole for the evaporator. It is a bit complicated, when you have the tranny in place. Don’t ask how I know this...
Re: Another restoration - 83' 528i
Curious about something: Are you making any "improvements" as you go? E.g. beefing up known weak spots like the sway bar mounts?
Re: Another restoration - 83' 528i
And the B-Pillar to roof joints.cek wrote: Sep 14, 2020 5:51 PM Curious about something: Are you making any "improvements" as you go? E.g. beefing up known weak spots like the sway bar mounts?
Re: Another restoration - 83' 528i
I wasn't aware cracking sway bar mounts is a thing.cek wrote: Sep 14, 2020 5:51 PM Curious about something: Are you making any "improvements" as you go? E.g. beefing up known weak spots like the sway bar mounts?
Did a quick search and it seems people were using M5 mounts for fronts but those are NLA now. Any other preferred method to reinforce those? Is it the slot for the tab that usually gives in?
I have old style mounts in the rear. Should be able to fabricate something for these if that's recommended.
According to the bushings I have ordered my sway bars should be 17mm front and 15.5mm rear but I can remeasure to be sure. I have no plans to upgrade the sway bars in the near future but you'll never know and it would be nice to eliminate any possible issues now.
I have read about that but I wasn't able to find any pictures of the issue online. On my chassis those joints look good. Or maybe I am looking in the wrong place. Do you happen to have any photos of such cracks? I can take a few of mine in the upcoming days if anyone bothers to mark up the problematic spot.
Are there any other weak points I should be aware of? Steering box mount, rear subframe and clutch pedal bracket are in the agenda. Anything else chassis related?
And since the Q&A rounds began, is this how the brake and fuel lines are routed in the rear? Blue for brake lines, pink for fuel lines and dots mark the mount points.

While I probably don't respond to every comment, know that I really appreciate your feedback. Thanks!
Re: Another restoration - 83' 528i
It is very much a thing especially the rear mounts when larger bars are installed.taavipa wrote: Sep 15, 2020 4:39 AM I wasn't aware cracking sway bar mounts is a thing.
Did a quick search and it seems people were using M5 mounts for fronts but those are NLA now. Any other preferred method to reinforce those? Is it the slot for the tab that usually gives in?
I have old style mounts in the rear. Should be able to fabricate something for these if that's recommended.
According to the bushings I have ordered my sway bars should be 17mm front and 15.5mm rear but I can remeasure to be sure. I have no plans to upgrade the sway bars in the near future but you'll never know and it would be nice to eliminate any possible issues now.
There is guy here that starting fabricating new BMW M5 style 25/19mm mounts:
viewtopic.php?p=1480778#p1480778
I am not sure about using smaller bars with these (maybe with an oversized bushing?).
The larger bars do offer a noticeable handling improvement but do introduce increased stress on the known weak mounting method from BMW. There is no other method than welding the fronts on. For the rears you can box frame the factory mounts and do a full weld to the chassis; it is the best way.
I have no photos (nor have seen any yet) but it was discussed in this thread recently, which is why it came to mind:taavipa wrote: Sep 15, 2020 4:39 AM I have read about that but I wasn't able to find any pictures of the issue online. On my chassis those joints look good. Or maybe I am looking in the wrong place. Do you happen to have any photos of such cracks? I can take a few of mine in the upcoming days if anyone bothers to mark up the problematic spot.
viewtopic.php?f=3&t=153387&p=1481140&hi ... r#p1481140
With all the work you're doing and you're evident welding skills, it would be easy enough to do a close exam of those joints and look very closely. It seems to me you could do some added plates over them just to be safe. With all the rot you have on the rockers, I would pay close attention to the bottoms of those B-Pillars as well. This joint is a main stress and transfer point on an E28 frame.
I have been admiring your work as you are a skilled bodyman with welding prowess I can only aspire to, but, and don't take this the wrong way, wouldn't it have been easier to start with a better shell? The level of body rot on this one seems excessive and the amount of time and energy you're expending just to return it to baseline is equally as excessive. Did you consider stopping and finding one better at any point? I have to imagine that even importing a solid US shell would have been both quicker and cheaper in the long run than all the work you're pouring into this one. Again, I mean no disrespect as you're a great craftsman and wish you were close to me so I could avail of your skills for my own projects. I don't think I am alone in that I would have considered this body a loss once the extent of rot was discovered.
Interested in your thoughts on this now that you are into this far.
Re: Another restoration - 83' 528i
These mounts do look really nice!vinceg101 wrote: Sep 15, 2020 12:29 PM It is very much a thing especially the rear mounts when larger bars are installed.
There is guy here that starting fabricating new BMW M5 style 25/19mm mounts:
viewtopic.php?p=1480778#p1480778
I am not sure about using smaller bars with these (maybe with an oversized bushing?).
The larger bars do offer a noticeable handling improvement but do introduce increased stress on the known weak mounting method from BMW. There is no other method than welding the fronts on. For the rears you can box frame the factory mounts and do a full weld to the chassis; it is the best way.
Currently, overall plan is to get the car back on the road without exceeding the budget too much and then work on improvements and things that are (relatively) easy to access. Sway bar mounts seem to go into the you-better-do-it-now category. On the other hand, sway bars themselves don't. I now have something to think over.
I will go over the joints again and in the meantime let's hope somebody will post a picture in that thread. Bottoms of the B-pillars are fortunately in good condition, thanks for the tip.vinceg101 wrote: Sep 15, 2020 12:29 PM I have no photos (nor have seen any yet) but it was discussed in this thread recently, which is why it came to mind:
viewtopic.php?f=3&t=153387&p=1481140&hi ... r#p1481140
With all the work you're doing and you're evident welding skills, it would be easy enough to do a close exam of those joints and look very closely. It seems to me you could do some added plates over them just to be safe. With all the rot you have on the rockers, I would pay close attention to the bottoms of those B-Pillars as well. This joint is a main stress and transfer point on an E28 frame.
I was expecting this question to pop up sooner or later and I believe it deserves a thorough answer.vinceg101 wrote: Sep 15, 2020 12:29 PM I have been admiring your work as you are a skilled bodyman with welding prowess I can only aspire to, but, and don't take this the wrong way, wouldn't it have been easier to start with a better shell? The level of body rot on this one seems excessive and the amount of time and energy you're expending just to return it to baseline is equally as excessive. Did you consider stopping and finding one better at any point? I have to imagine that even importing a solid US shell would have been both quicker and cheaper in the long run than all the work you're pouring into this one. Again, I mean no disrespect as you're a great craftsman and wish you were close to me so I could avail of your skills for my own projects. I don't think I am alone in that I would have considered this body a loss once the extent of rot was discovered.
Interested in your thoughts on this now that you are into this far.
It definitely would have been easier to find a better shell. And if your main goal is to get a nice car that is exactly what you should do, no arguing there.
Now, I wanted to try my hand at sheet metal work and for that purpose maybe an older/rarer car would be a better fit. But I also really wanted an E28 so (at least to me) it makes sense. I've been doing chassis work on that car for a little bit more than a year now (more intensly from the beginning of 2020) and I haven't felt overwhelmed or bored yet. If something feels too difficult at the moment I can just put it aside and come back to it later with more experience and new ideas I have gathered in the meantime. Seeing it all coming together just makes me want to put even more work into it.
While bodywork is extremely time consuming it doesn't cost much if you do the work yourself (OEM panels would be an exception here). I do consider this time well spent and I am enjoying the process.
A whole other story is finding a good chassis in this country (I'll leave imports for later). I have kept my eyes on local car sales portals and forums/FB pages after buying this car. The prices of E28s are through the roofs, people are asking thousands of euros for cars that could very well be in worse state than mine. I actually joined my friend to check on few of those, nothing good. The price tags on more decent vehicles (at least based on photos) are usually closer to 10k. And they do not pop up often.
I should have got an E28 maybe five years earlier. I wasn't actively following the scene back then but I am quite sure the same thing happened with the E28s (and E30s) that's going on with E36s and E34s at the moment. There's quite a large group of people (mostly young lads) that buy those to trash them during winter months. If the car doesn't end up bent around a tree or with a blown engine it might survive for another season. Otherwise it gets dismantled for parts. And often even quite decent cars go down that way as it's an easy way to make a buck. To be honest, it is getting hard to find a decent E36 or E34.
I have stumbled on some old ads dating back to 2010 and earlier where E28s with near perfect chassis were torn apart and sold for parts. It's a sad sight.
Importing a car could be an option. But I am afraid the situation is not that much better in neighboring countries. Getting it from someplace further away is quite an adventure by itself. Unless you pay someone to bring you the car you have only seen on pictures. I know a guy who did just that and got an E28 imported from Sweden a few years back. Can't say it was in any better shape than mine. Only way I would import a car without actually seeing it is if there's someone I trust to examine it for me.
Re: Another restoration - 83' 528i
@taavipa, I love your attitude and am grateful that you are sharing your experience with us. Please carry on!
Re: Another restoration - 83' 528i
You are more or less correct in the general routing. I just scoured through my files and found these photos from Rear End Rebuild from 2014. I don't have specific final photos of the brake lines, but you get to see some of them in these photos:taavipa wrote: Sep 15, 2020 4:39 AM And since the Q&A rounds began, is this how the brake and fuel lines are routed in the rear? Blue for brake lines, pink for fuel lines and dots mark the mount points.

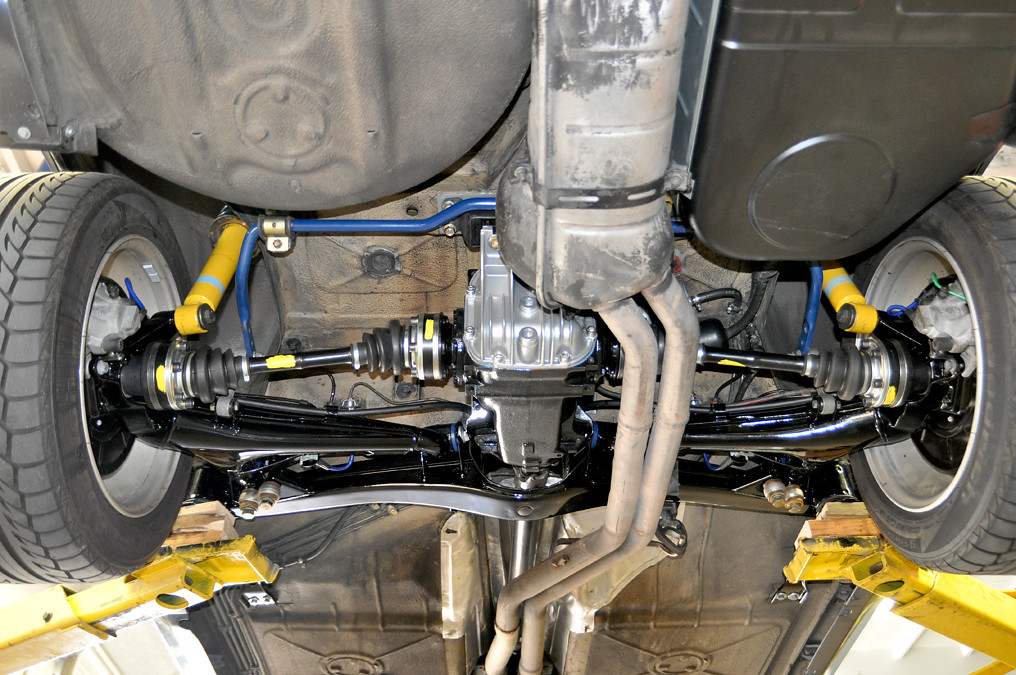
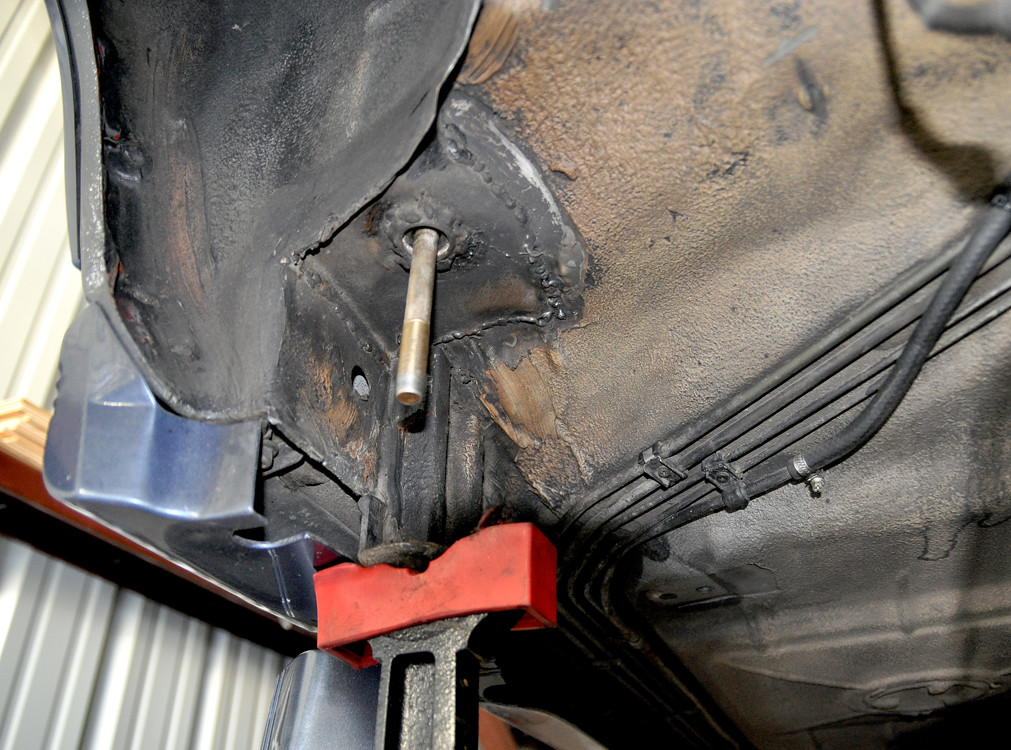


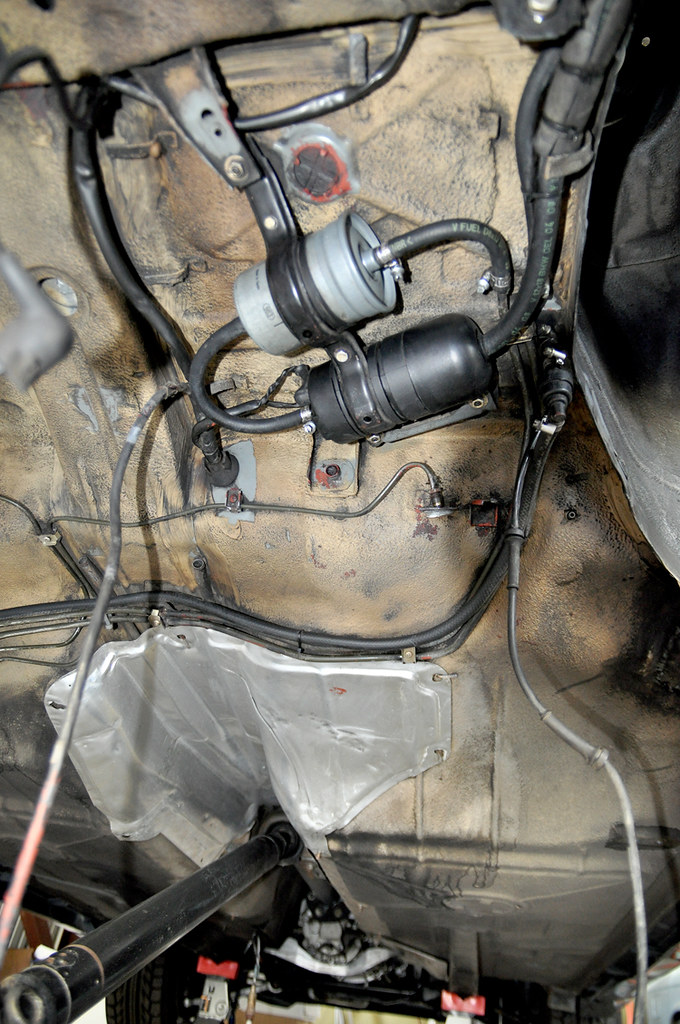
In the second to last photo you can see the reinforced boxed Rear Sway Bar mount they did when the previous owner installed the Dinan sway bars. You can also see what other body welding repairs happened to this car from previous body rot: notice the re-welded Rear Sub Frame mounts.
Re: Another restoration - 83' 528i
I couldn't agree more. Thanks for the thoughtful response and your reasoning; clear concise logic like this is rare these days.cek wrote: Sep 15, 2020 4:26 PM @taavipa, I love your attitude and am grateful that you are sharing your experience with us. Please carry on!
In for the updates.

Re: Another restoration - 83' 528i
@vinceg101 and @cek, those pictures are exactly what I needed, thanks guys!

My conclusion at the time was that any condensate should be able to escape through the slot between mount and bottom panel.
I have once done the mistake to clog some drain holes on a car with sound insulation panels so now I am really careful with such things.
In addition, I didn't see any evidence that the bottom layer of sheet metal was actually attached to the mount from the factory.
Just to share some great content and to elaborate some more on the subject of finding a good chassis to begin with.
Possibly some of you might already be familiar with his work but check out this thread on retro-rides forum: https://forum.retro-rides.org/thread/11 ... 28-m5-blue
While this car was showing some dangerous signs, it could pass as a half-decent chassis in my opinion. Especially, in an online ad. If you bother to scroll through the whole thread, you can see how many rust issues the car actually had. Of course, I wouldn't dare to compare saving an M5 to saving an 528i.
Other than that, this guy does wonderful work using just basic tools and hands out a lot of useful tips. I have learned a great deal following his threads on that forum (he has one about an E12 M535i and a few others).
This is how I intended to weld them at first. But when I cut away the rotten bottom layer I discovered a drain hole (at least I think it's a drain hole) in the next layer. Take a look at that photo

My conclusion at the time was that any condensate should be able to escape through the slot between mount and bottom panel.
I have once done the mistake to clog some drain holes on a car with sound insulation panels so now I am really careful with such things.
In addition, I didn't see any evidence that the bottom layer of sheet metal was actually attached to the mount from the factory.
Just to share some great content and to elaborate some more on the subject of finding a good chassis to begin with.
Possibly some of you might already be familiar with his work but check out this thread on retro-rides forum: https://forum.retro-rides.org/thread/11 ... 28-m5-blue
While this car was showing some dangerous signs, it could pass as a half-decent chassis in my opinion. Especially, in an online ad. If you bother to scroll through the whole thread, you can see how many rust issues the car actually had. Of course, I wouldn't dare to compare saving an M5 to saving an 528i.
Other than that, this guy does wonderful work using just basic tools and hands out a lot of useful tips. I have learned a great deal following his threads on that forum (he has one about an E12 M535i and a few others).
Re: Another restoration - 83' 528i
My take is that is not a drain hole, however I'm not sure what it would be. It would be located in the cabin, specifically in the rear seat well and kind of in the back corner against the wheel well bulkhead. I do not recall any hole in either of my cars back there nor underneath either car. Even if water were to accumulate in the rear seat well, there are holes in the vertical wall that would release water onto the rear seat floor (and then to the drains in the floor pan).taavipa wrote: Sep 16, 2020 6:00 AM This is how I intended to weld them at first. But when I cut away the rotten bottom layer I discovered a drain hole (at least I think it's a drain hole) in the next layer.
My conclusion at the time was that any condensate should be able to escape through the slot between mount and bottom panel.
I have once done the mistake to clog some drain holes on a car with sound insulation panels so now I am really careful with such things.
In addition, I didn't see any evidence that the bottom layer of sheet metal was actually attached to the mount from the factory.
Don't worry about it is my opinion.
Re: Another restoration - 83' 528i
You must be right. I took a look at the mount from cabin side today and the top layer has another hole in it. I can't see how this could possibly function as a drain. So I'll probably weld the floor panel to the mount and use the holes to spray some cavity wax between the layers after the car is painted.vinceg101 wrote: Sep 16, 2020 11:37 AM My take is that is not a drain hole, however I'm not sure what it would be. It would be located in the cabin, specifically in the rear seat well and kind of in the back corner against the wheel well bulkhead. I do not recall any hole in either of my cars back there nor underneath either car. Even if water were to accumulate in the rear seat well, there are holes in the vertical wall that would release water onto the rear seat floor (and then to the drains in the floor pan).
Don't worry about it is my opinion.

But damn sway bars and their mounts.
I was going through the photos posted yesterday when I realized that the newer rear mounts face the opposite direction compared to the old ones. So I visited realoem and go figure - new and old rear sway bars do also differ. And of course the 15.5mm rear sway bar I have sourced goes with the new mounts. I do have another rear sway bar but that one measures only 12mm. The thickest older sway bar I could find on realoem was 14mm.
Furthermore, turns out my front sway bar is also a skinny one - 16mm with a thick coat of paint.
Interestingly enough, realoem lists some front sway bars "up to 09/83". I don't recall any changes in front axle throughout the production years that could possibly need a sway bar in different shape. Or have I missed something?
You can spot the differences on that photo. Newer sway bar has longer arms and the bend is off center to clear the newer diff mount.

So my options for the rear, as I see it, would be:
- Reinforce the older mounts I currently have. This way I could run my humble 16/12mm setup until I could source a 14mm rear bar and whatever I see fit for the front. I looked around online and it seems to me all aftermarket options are made keeping the newer cars in mind. Some were listed for 82 and up but I suspect that they actually won't work with older mounts. Only way to get something thicker than 14mm would be a custom-order.
- Fabricate some custom rear mounts. OEMs are NLA. And actually the cross-beam they attach to also differs from older cars. My buddy's 86 sits right next to mine so I can crawl under it and take all the measurements I need. Only question that remains is: would the newer sway bar clear my old style diff mount? This would allow me to use my 15.5mm sway bar now and in the future I'd have plenty to choose from.
Re: Another restoration - 83' 528i
Could possibly be a locating hole for a pin in the production line assembly jig, allowing that piece to drop on the pin and to easily align before welding.vinceg101 wrote: Sep 16, 2020 11:37 AM My take is that is not a drain hole, however I'm not sure what it would be. It would be located in the cabin, specifically in the rear seat well and kind of in the back corner against the wheel well bulkhead. I do not recall any hole in either of my cars back there nor underneath either car. Even if water were to accumulate in the rear seat well, there are holes in the vertical wall that would release water onto the rear seat floor (and then to the drains in the floor pan).
Don't worry about it is my opinion.
Re: Another restoration - 83' 528i
Mid-August 2020
Next up was passenger side rocker panel.
Lucky for me I have a buddy who’s in sheet metal fabrication and car restoration business. He’s currently restoring an alloy body Alfa Romeo 6C from the 30s and he’s done a few e-type Jags and other cars in the past. He was happy to help me out with the rockers. His experience was more than welcome and while you probably could do the rockers alone, I find it’s actually more of a two man job to fit them.
I first removed the remnants of old side sill so I could do a clean up before my friend came over. I didn’t realize back then that it would actually be a good idea to fit the doors before removing old sills as it would make adjusting them easier. But to be honest, I did this later on the driver’s side and since my old rockers were anything but straight (partly because I had abused them when fixing inner sills) this wasn’t that helpful.

After many long hours of adjusting the doors we were content with how they sat. The idea of installing the doors if car is already painted scares me. One small wrong movement and you have nicked you fresh paintjob.
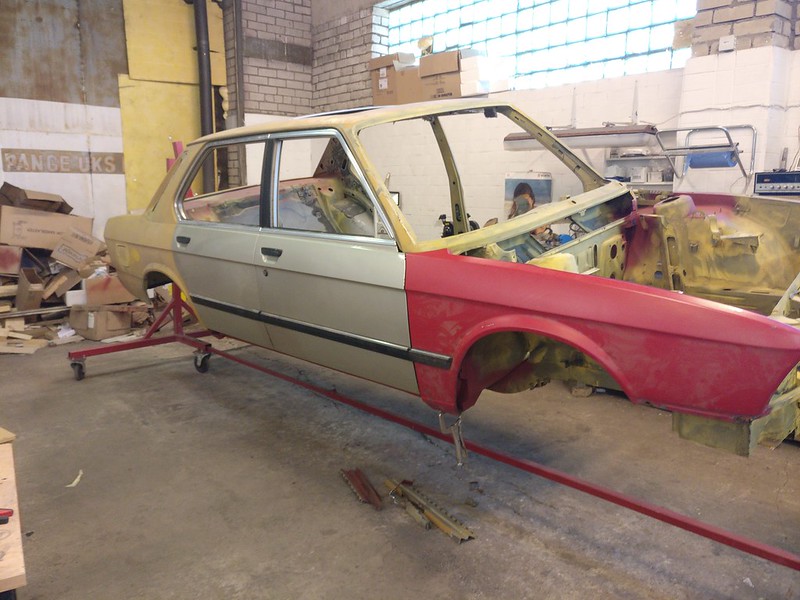
Those repro sills were quite awful to fit. The depression for B-pillar was off by 5-6mm. Angles of some bends were off. The step in front where the sill panel gets covered by front wing was crooked. The depression or hole in the B-pillar area that should accommodate the front lower corner of rear door when you open it was completely missing.
The front joint line was chosen so that no weld would be on the bottom of the sill where it would disrupt water getting to the drains. Unfortunately, rear weld line had to cross the outer face of the sill. The joint of rear wheel arch and side sill is brazed together from the factory so you can’t weld it there.
Anyway, we got the new sill fitted and tacked in place

Next task was to remove the doors and do all the welding
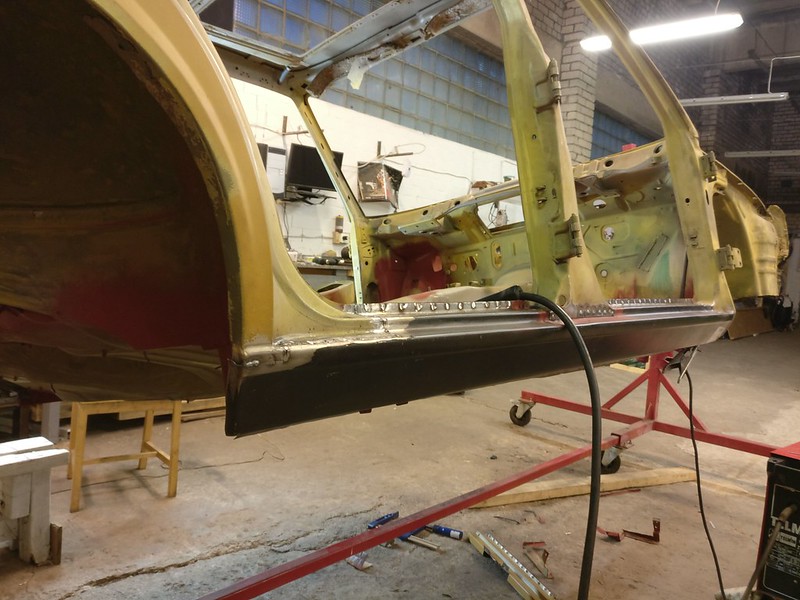

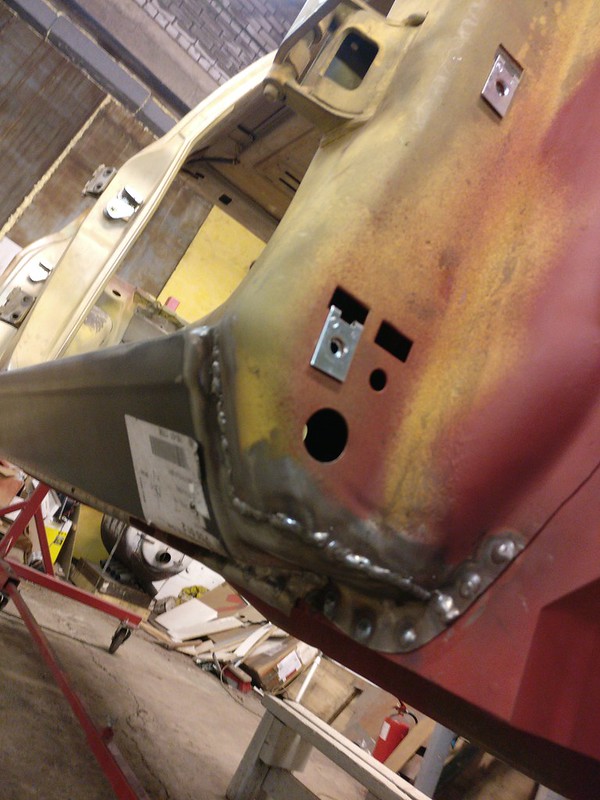

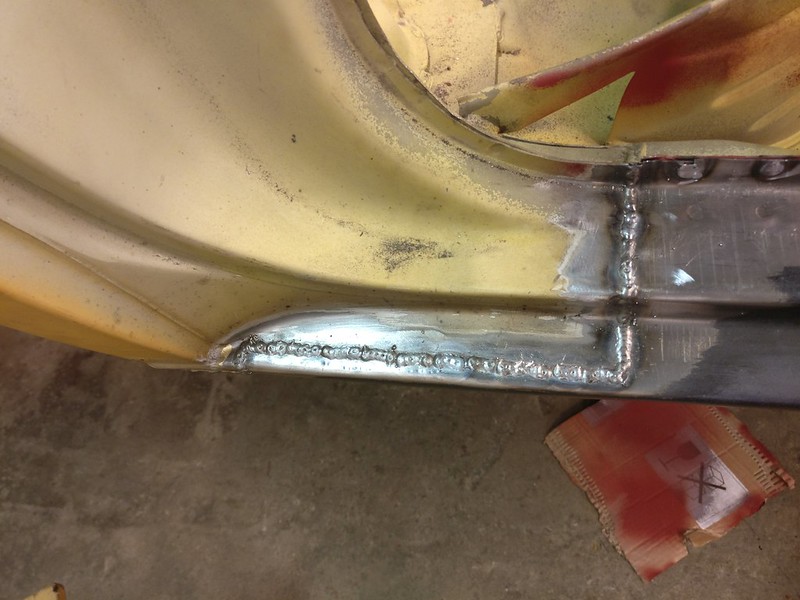

Then some grinding and primer later we had this

I guess some warpage is inevitable when welding the sills like that, especially with no access to the inside to stretch the metal back out.

Also made some new wiring harness clips

And installed them

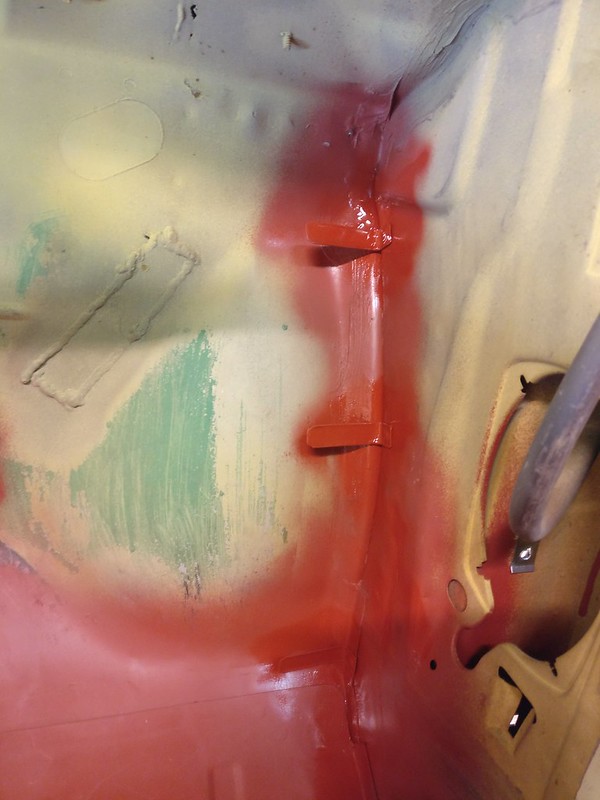
I think the passenger's side had only two of those clips from the factory (top and bottom). But I see no harm in adding an additional clip there.
Next up was passenger side rocker panel.
Lucky for me I have a buddy who’s in sheet metal fabrication and car restoration business. He’s currently restoring an alloy body Alfa Romeo 6C from the 30s and he’s done a few e-type Jags and other cars in the past. He was happy to help me out with the rockers. His experience was more than welcome and while you probably could do the rockers alone, I find it’s actually more of a two man job to fit them.
I first removed the remnants of old side sill so I could do a clean up before my friend came over. I didn’t realize back then that it would actually be a good idea to fit the doors before removing old sills as it would make adjusting them easier. But to be honest, I did this later on the driver’s side and since my old rockers were anything but straight (partly because I had abused them when fixing inner sills) this wasn’t that helpful.

After many long hours of adjusting the doors we were content with how they sat. The idea of installing the doors if car is already painted scares me. One small wrong movement and you have nicked you fresh paintjob.
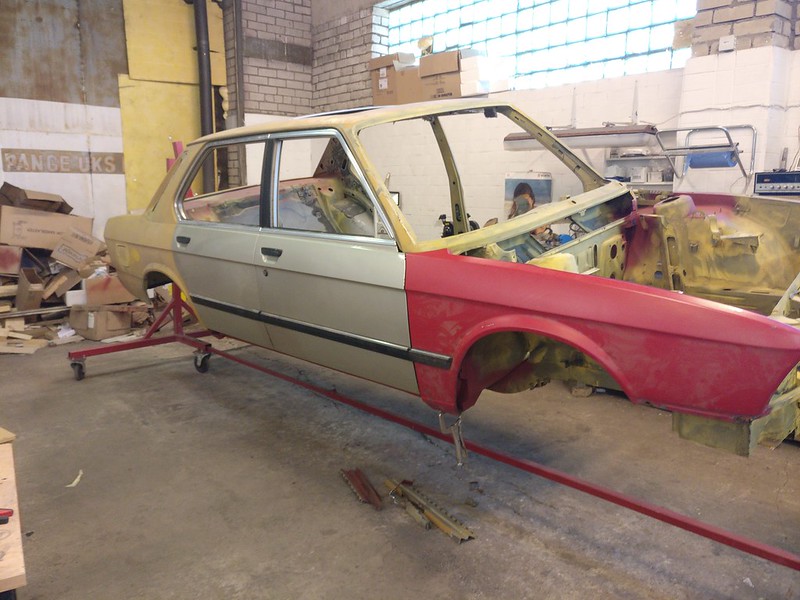
Those repro sills were quite awful to fit. The depression for B-pillar was off by 5-6mm. Angles of some bends were off. The step in front where the sill panel gets covered by front wing was crooked. The depression or hole in the B-pillar area that should accommodate the front lower corner of rear door when you open it was completely missing.
The front joint line was chosen so that no weld would be on the bottom of the sill where it would disrupt water getting to the drains. Unfortunately, rear weld line had to cross the outer face of the sill. The joint of rear wheel arch and side sill is brazed together from the factory so you can’t weld it there.
Anyway, we got the new sill fitted and tacked in place

Next task was to remove the doors and do all the welding
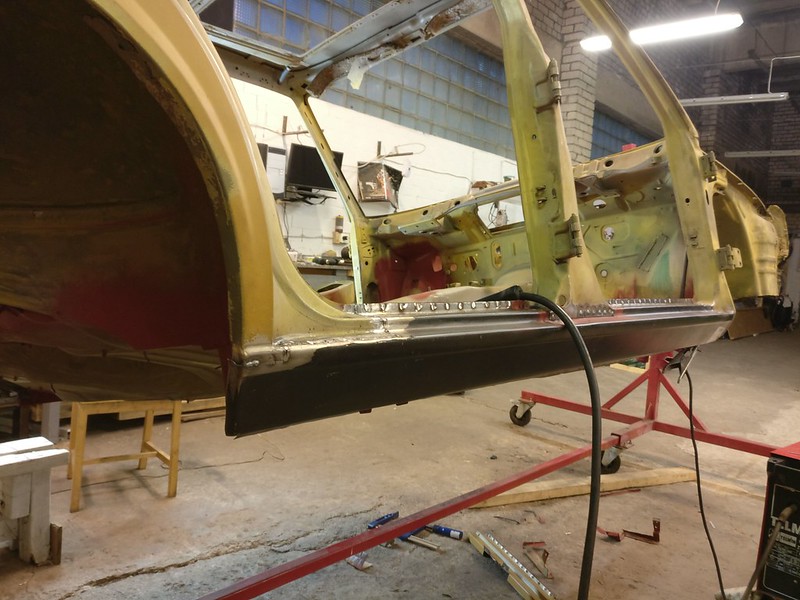

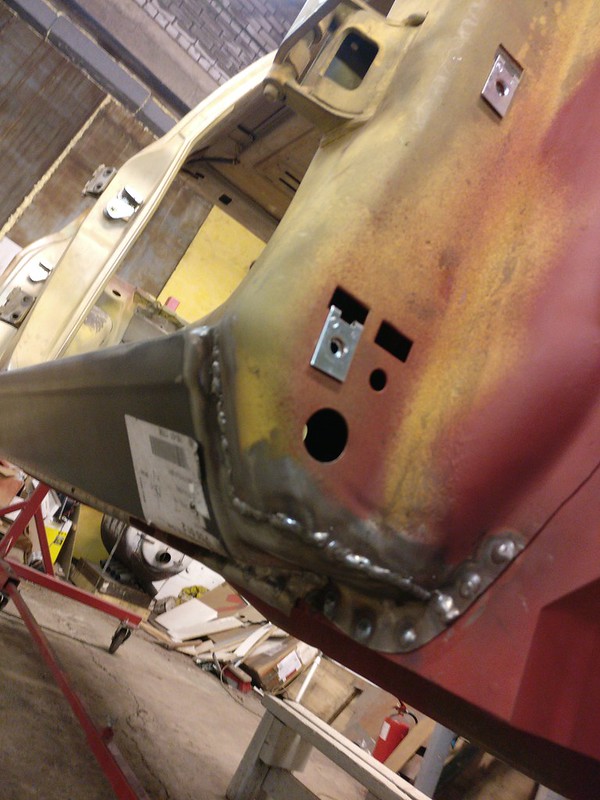

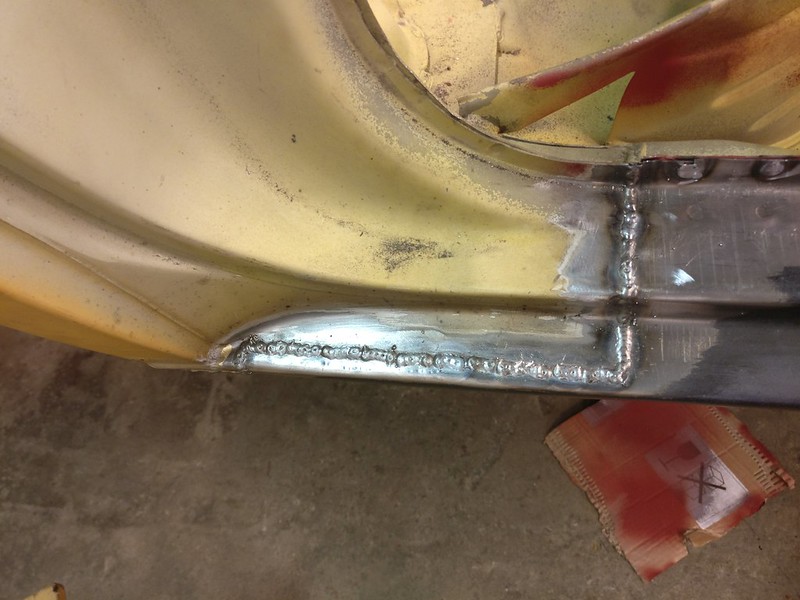

Then some grinding and primer later we had this

I guess some warpage is inevitable when welding the sills like that, especially with no access to the inside to stretch the metal back out.

Also made some new wiring harness clips

And installed them

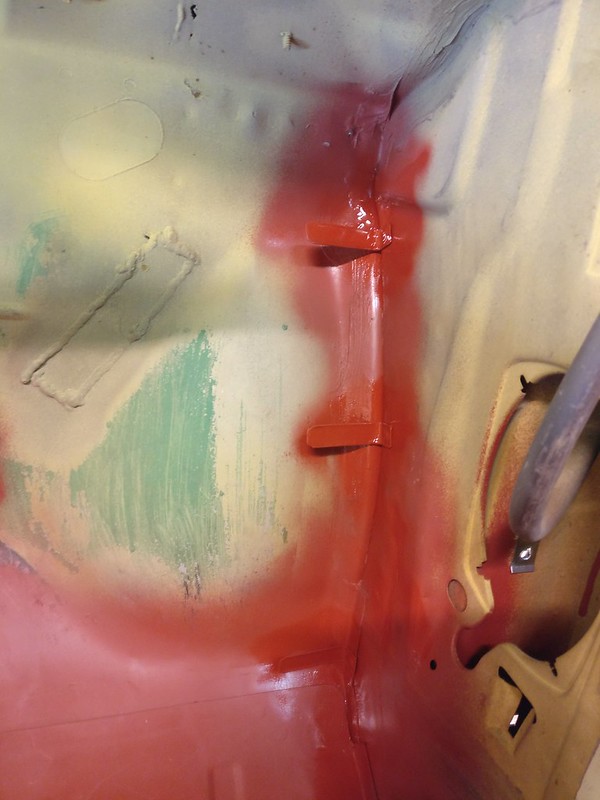
I think the passenger's side had only two of those clips from the factory (top and bottom). But I see no harm in adding an additional clip there.