I took the head over to my powder-coater and had them put a satin Cerakote clear on it. I figured it will help seal the casting and keep it easier to clean and it should hold up well. It wasn't cheap, but I figure it's a lot better than some of the other options. I was looking at the Eastwood 2K Ceramic high-temp clear, but they don't make it anymore and I figured how hard could this be. It wasn't difficult, but it wasn't cheap either.
For the hell of it, I decided to just put the ceramic-coated exhaust manifolds on as well.
I picked up a bunch of stuff from the plater, so with that done, I could mount the oil cooler. It didn't need to be mounted now, but I figured why not.
Also, with that, I had previously talked to a Porsche shop about having them rebuild my oil cooler lines. I talked to them because they had listed a custom line for a 914 which had an M22x1.5 fitting but apparently they couldn't sell me any, so he said he had the hose, the crimp collars and the crimping tool. All I had to do was get my old fittings plated, bring them and the old hose to them and they would make it happen. I sold the guy a set of BBS E75s a few years ago for a vintage FIA race car they were working on, so it seemed like that connection was going to pay off.
While waiting for all of the pieces to fall into place to start motor assembly, I cleaned up the replacement ignition harness I purchased. It was very supple and in nice shape, so it was worthwhile. Much nicer than my original.
Work finally began on motor assembly June 16. Block was primed and painted. Morning of the 17th, we began with freeze-plug installation.
It pays to have the right tools. Getting these things seated properly is critical. It takes a lot of effort too. Fingers crossed they all seal and we don't have to replace one in the car.
Next, we started with the crank bearings. My original crank was in excellent shape, measured out perfectly for standard bearings. My original bearings weren't even worn. Here's a shot of the plastigauge on the #1 main bearing:
The other six were dead-on, so we were a go with the standard bearings.
Here is a shot of my shot-peened rods.
Everything was within spec for those as well. I had to go to work, unfortunately, so I missed the fitting of the rings and whatnot. By the end of the day, 5 of the 6 pistons were installed. #6 was installed Monday morning due to a problem with the oil rings for that one. At that point, the really time-intensive, focused work was completed.
Of course, I still had plenty to do like reassemble my throttle body and the oil filter housing.
I went to storage and pulled this dogleg off the shelf. Came from a Euro 635CSi that had an engine fire. Pretty low miles, too, and I could assume that it was not the reason the car caught fire.
I spent the next several hours cleaning it up on my outdoor workbench.
With that sorted, I turned my attention toward getting the wiring straightened out in the car. I had talked to Terry about getting the car in to do the headliner and he was booked up solid, suggesting that July 11 was the earliest he could take it. I explained where I was at, behind on everything, and while it wasn't his fault, headliner has to go in before the rest of the interior. He said he'd take it June 27. Great.
So, I put a battery in it and figured I'd either die or see some progress.
I didn't die.
So, that was progress. At the time, I had some lock motors acting up and only the driver window worked. Still, Nothing shorted out and I called it a win considering the last time this car had electricity was August, 2010.
Back to the motor. This time, head assembly!
And voila!
We discovered that you cannot buy the oil pump sprocket anymore. It comes on a new pump, but it cannot be purchased separately. It might have made the decision between spending $475 on pump rebuild parts versus $530 on a new pump, but the only part of the pump that was reused was the pickup, so I guess it wasn't that bad. Febi stopped making it, too, so we ran into some issues. Alex found a new one on eBay, so we waited.
I confirmed my appointment with the upholstery shop. They had me down for Monday, so I made the final push over the weekend to finish up everything I thought was necessary for them to install the headliner. After confirmation, I ordered a tow truck for first thing Monday.
Back at home, I installed all of my stereo wiring and installed my Bosch power antenna. It took several careful, deliberate readings of the instructions, but we finally got it.
Monday, June 27 rolled around and the car rolled onto a tow truck. Oh how I wished Sonny G would have picked up his phone.
I show up and was asked why I was there and why the car was there as I wasn't on the schedule. When we pulled up, it was clear there were many cars there. Fortunately, they took the car and Terry got on it ASAP, after he went through how much work was going to be involved. I showed him a few things on the '75 E12 so he can see how the headliner goes in, as on E12s, the rear of the headliner is a floating piece, not wrapped around the pinch weld, like E28s - not that he knows E28s, but it's an important distinction.
He had a couple of questions later in the day, so he asked I come by to answer them. He had already made progress.
Terry suggested he had a long way to go on it, so I kept working on things on my end. I had a decent batch of stuff at the powder coater, so I picked all of that up.
I put my power steering pump back together.
Then while looking at something on one of the E24s, I happened to notice that one of them had the harness connector I needed for the CTS attached to the CSV. So, I harvested that guy to replace this:
Now that I'm a pro at de-pinning these Bosch connectors, I made quick work of it and replaced the boot, too.
Tuesday, June 28, I got a call around 10am saying the car was ready to go. I went over and had a look.
Installation cost was $700 (with a discount!). Towing was $100. Sewing the headliner was $200 and the fabric cost $150 from BMW (3 meters). There were other people that could have installed it but I didn't want more complaining and excuses suggesting that the headliner they didn't sew was wrong versus a failure in their process or vice-versa. I figured the person who made the headliner should be responsible. Of course the B7 Turbo was a headliner I bought sewn for $75, $150 to install and no towing. It also only took 2 hours to install, so this whole process was sticker shock to me.
Friday, July 1, back on the motor. The oil pump sprocket showed up Friday morning thanks to the USPS last mile delivery where it takes three days to get something after it shows up in your city. Of course, despite the eBay photo showing it coming with the nut, there was no nut. Fortunately, Alex had one. It's an M10x1 jam nut, so not exactly super common.
With that sorted, oil pump was installed, head installed and first torque sequence squishing my $140 headgasket.
While waiting for the second torque sequence, we installed the oil pan.
Finished up the chain, primed the tensioner, installed the upper timing cover.
Valve adjustment done and this motor is ready to go in the trash.
Off the stand onto the hoist. Install the rear freeze plug, then the flywheel.
We loaded it into the back of his Aztek and I drove that to my house and unloaded my motor, then started attaching things to it since I didn't know what else to do with it.
I had to order motor mounts on eBay, so my idea of putting it in the car over the weekend was a no-go.
Mike, the painter, came over Sunday morning to fix a spot under the car next to the transmission. While he was there, he re-textured these for me and I painted them.
Then I worked on the rest of the trunk plastics which are fragile and a pain in the ass.
I thought quite a while about how to put the motor into the car. I was going to put it in from underneath but the reality is that without a lift, it would be a disaster. The problem with going in from the top is the hood and the angle of the motor, but my friend Scott (scarey013) helped me resolve the angle issue. I had thought about using a ratchet strap but I wasn't totally comfortable with it. Sure enough, it worked perfectly. With that ready, the motor was ready to go in. Adam (ldsbeaker) came up from Yuma for a visit and my motor mounts had just arrived, so we fueled up on Waffle House and got to work!
It was at this point we figured out to remove the left front wheel and he just happened to have his impact ready with a 17mm on it, so he's in the background there.
It took maybe 10 min to put the motor in the car. 30 min start to finish from moving the engine hoist to lowering the car off the jack.
Alex came by that afternoon and we torqued the crank nut.
With the motor in the car, that's like a big deal and now I can just work on stuff. I started putting my intake manifold together.
Of course, waiting on parts, so I installed the accessories.
and the harmonic balancer, of course.
I went to the exhaust side and installed the exhaust manifolds and their heat shields.
Back to the intake side.
Either the exhaust on my car is original and just in awesome shape or it was replaced at some point. I looked into buying new, but the car sounded great before and it didn't even show any weak spots, so I borrowed a van from work and took it to the powder-coater to have it ceramic coated to match my manifolds and downpipes.
My next task was to work on installing a transmission in this thing. I wanted to get the engine properly supported rather than leaning against the firewall. I installed the clutch using an alignment tool. Everything went great. Installed the bell housing with a new clutch fork, pivot pin and spring. I was going to go with the stainless pivot pin, but the original lasted this long. I then started doing the final tasks on the transmission. selector shaft seal, new reverse light switch, make sure the fill plug is loose, install the speedo drive, etc. Everything went fine until I got to the last one. I pulled the plug out and found that instead of having a gear on the output shaft that drives the speedo drive, it had a spacer. I looked into what it would take to swap it, since I have the 262 box of rocks from the 530i and found that I'd have to pretty much take the back of the transmission apart unless I wanted to make a special tool on the milling machine I don't have drilling 3.999mm holes for 4mm screws then slicing them at the right angle to grab the gear and pull it out. Plus, that would also require pulling the output flange, etc. So, I went back to the shelf of doglegs and grabbed another one, supposedly rebuilt, that I bought from Al Taylor in '09. It came from an early 6er, so I cleaned it up. Of course, I already used my selector shaft seal on the other one and despite the selector shaft seal being used on 40 different BMWs - even current models, there was no way I could find one in town on a Saturday, so I popped the old one out (from 2006) and decided to tap a new one in while it was installed. So, I got under the car, put the transmission on my right thigh and got it up into position, only to find it stopping about 1/2" from the bell housing. I moved it around, tried turning the shaft (I put it in gear, in case I had to rotate it to get through the clutch). Nothing. I did this four more times over the course of three hours. No luck. I put the alignment tool in each time and it was right on and smooth. I couldn't believe it and while Kyle told me the tools are junk, I refused to believe it. I finally gave up and sent Alex a text asking if there was more than one size of pilot bearing or something. I measured all of mine in the garage at the time (2 265/5, 1 265/6 and a 262) and they were all the same. He said he'd come help me out the next morning. I didn't want to put him out on a Sunday but he insisted.
The next morning, he came by and we spent quite a bit of time on it, ultimately starting from scratch,but using the transmission to align the clutch. That did the trick and we got it within 1/8" and that was enough to snug up with the nuts. It also worked out perfectly that a mechanic of his was at the shop working on his own project, so I could swing by and grab a selector shaft seal! Back in business. I got back to work and put the shifter in.
After that, it was driveshaft time. I wish I could go to the store and buy individual packs of bread - like two pieces. Enough for a sandwich, since I don't want a loaf of white bread. After using white bread for what I used it for, I definitely don't want to eat white bread.
I cleaned up my Beyer reman driveshaft and put it in the car. Unfortunately, it seemed too short. This driveshaft came from the E24 and was about 1000 miles old. I'm not sure it started the fire either.
I didn't get it. Couldn't pre-load the bearing and I had WAY too much of the splines showing. I started wondering if it was the wrong shaft, but compared to the other
E28 265 shaft at the house, it was the same.
I made a trip to storage to grab the original driveshaft from this car. It was in phenomenal shape. center bearing like new, pilot bushing tight like a tiger and the u-joints were silky smooth. I wiped it down and decided to Czech it out before I cleaned it up.
E28 is on the right.
Center bearing is pre-loaded and it looks correct!
I figured out later that the side-loader diff is shorter in length compared to the E28 diffs. I was stuck. Shifter hole was in the same spot, center bearing mount is further back and the diff mount is in the same spot, so the only variable is the location of the input flange, which would add length to the shaft.
So, once that was all done, the motor was properly supported.
Then I installed the downpipes and called it a night.
I put all of the tools away and went to 5erWest. While on the way, I decided to check in again with the Porsche shop about my oil cooler lines, since this is something that shouldn't be taking this long and it's holding me up, since I need to attach the cooler lines with the airdam off, then install the airdam before I put the radiator in so I can get to all of the fasteners. Sure there are other ways to do it, but I shouldn't have to. Turns out, apparently, they had to order a couple different kinds of hose since nothing they had was working. I told him I'd be gone a week and I'd check in when I came back.
While I was gone, I got a shipment notification on my dashboard. It showed up while I was gone, so I opened it when I came home.
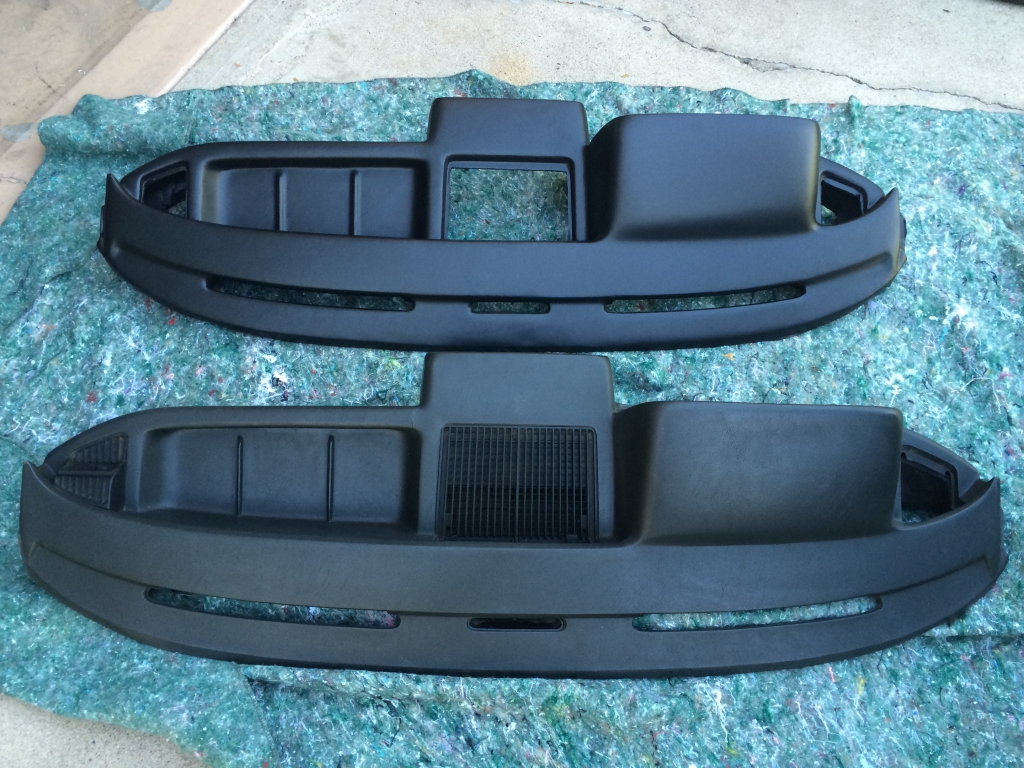
An original dash is in the foreground. They're the same size.
I decided to install the wood.
I'm not sure what I think about it. I see a lot about it that I don't like. Meh. Of course, there's nothing I'm going to be able to do about it, so fuck it, I guess.
So, I got back to work on things I can do something about.
The radiator is only in there to measure the length to cut the overflow hose and make sure my hoses go where they're supposed to. I had to order all of the hoses from the dealer, but they're apparently suggesting that the heater hoses are Euro parts and I have no ETA on those.
So, with that kinda done up front, I decided to wrap up the tasks under the car that would be easier to do without the exhaust in the way. I torqued all of my axle bolts, made a tie-rod adjustment and installed all of the cotter pins for those and then I put my fuel pump bracket together.
Those rubber mountings are $11 ea.
I put the air box together despite waiting on the AFM elbow and the intake boot, but I wanted to see how the airbox looked under the hood. It's been a long time since any of this has been in the car.
You will also note that the hood insulation is installed.
I apparently lost my driver door lock. I found it with some trim clips I pulled off the car years ago and decided to put it in a safe place. No idea where that is, but I managed to get another one from a car in the yard. Despite having several E28 lock cylinders, the E12 ones don't use plastic trim rings, so they're different. I gave up on looking for it as right now, I just don't have the time and I have essentially a matter of days to finish this car, so today, I took the lock over to a locksmith I've known forever and she wouldn't do it. I was frustrated since the place she recommended isn't someone I'd want to deal with, but after talking for a short time, she remembered she got a bunch of weird stuff from a guy who went out of business and amongst it was this:
$10 and it was mine. This wasn't something I really wanted to do myself, but she taught me a lot years ago about locksmithing so I figured what the hell. I might enjoy it even though I'd rather trade money for time at this point.
Later today, I picked up the MTL/MT-90 for the transmission and I had the oil for the diff on hand already. I picked up some more parts and was frustrated that nothing was getting done and I've got work stacking up, so I decided to just work on the car some more.
I filled the transmission and the differential and rekeyed my lock cylinder to the key. Works perfectly, so pretty happy about that. At this point, I'm ready to put the rest of the exhaust in, which I hope to do tomorrow. Would be cool to bleed the clutch and brakes so I can put it back on the ground, but I'm not going to get ahead of myself.
Sorry for such a short update, but it's tough to keep track of every little thing that happens.