Past due for an update. I got the car back from the body shop about 10 days ago. I feel like I haven't made a ton of progress in the time the the car was at the body shop, but now that it's back, I really want to get the momentum going again.
First, one nice surprise is that Roger was able to blend in the bright yellow SEM sprayable seam sealer that I'd used on the underside. Here's what it looked like after I sprayed it:
And here's what it looks like after Roger fixed it:
Turns out, SEM makes a product specifically intended to blend new undercoats with the color of our old stuff:
I also cleaned up the transmission. Before:
And here's after. New seals (input, output & selector shaft), new reverse light switch, all new rubber & bushings for the linkage. Note that the rubber boot at the base of the stick shift was butchered on some prior occasion when whoever was working on the car was unable to figure out how to get the reverse-light switch wiring up from the tranny into the cabin (they just cut a gash in the side of the boot & stuffed the wire through, I guess). So I bought a new boot (not installed yet).
Also, in case it's of interest, here's a pic down the elector shaft hole. There's zero room to push the old seal down in order to press a new one in on top of it. I don't get how some people think it's OK to try to just jam a new seal in on top.
We also painted the engine compartment. Here's the sanding & scuffing in progress and then the painted result:
I also solved a small minor mystery. It's tough to see in this pic, but I'd always puzzled why a block of wood had been inserted into one of the trunk hinges. Turns out that the right trunk hinge had been bent back - as if someone had bent the hood back when it was open. (You can see that the tab at the right side of the pic is slightly bent away from the hinge; the brown thing in between the tab & the hinge is a small block of wood.) The block had been inserted in there to make up for the "hyper extension" of the hinge and keep the hood from opening more than it was supposed to. Needless to say, I have two new hinges in hand. They'll get painted (along with the rest of the trunk) in the coming days (weeks is more likely).
Aaaand here's the car all dolly'ed up getting ready to get towed home.
This was shortly before a minor disaster struck. About a mile into the trip the rear wheels locked up. I was immediately reminded that I'd never filled the diff with new fluid - DAMN! That seemed like a good idea at the time - I figured I'd be more likely to get all the fluids into the car if I did them all in one step instead of trying to remember what I'd put in and what I hadn't. As a result of having no fluid in the diff, the rear pinion gear overheated, expanded and seized up, causing the rear wheels to lock up. Here's a pic of the burnt pinion bearing.
As it turned out, this ended up being a HUGE blessing in disguise. I don't have pics (or videos), but after I got the new bearings pressed in and started to torque down the new crush collar, it became clear that my original pinion bearings had likely been bad all along (or were about to go bad). I can't remember if I posted this earlier, but I replaced the original crush collar at the same time that I replaced the pinion input shaft seal. This was my first time torquing down a crush collar. I followed all the directions I could find. When I was testing the pre-load last time, the static drag torque (torque required to get the pinion spinning) was ~40+ in-lbs, and then even though the running torque was in the correct range (I was shooting for 15 to 20 in-lbs), it was a tiny bit notchy - that is, it spun fine to my fingers, but the needle on the beam-style torque wrench was vibrating.
This go-round, the static drag was maybe 19-20 in-lbs and the running drag was 16-17 in-lbs. (I was shooting for 15 but it snuck up on me quicker this time, too.). Also, the needle on the torque wrench was smooth & steady.
In case it's helpful, based on what I found online, running drag of 14-16 in-lbs is ideal (getting that from a Metric Mechanic PDF), so I think I pretty much hit it.
I also cleaned up the drive shafts. The rear U-joint was stiff, so I ended up replacing the center cross-member & the associated bearings. This drive shaft had already been serviced once before, so the U-joints had already been "de-staked" and replacing the cross-member was pretty straightforward.
I also got my leather dash finished! Damn ... I wish this project was already to the point where all I had to do is just put parts back on the car.
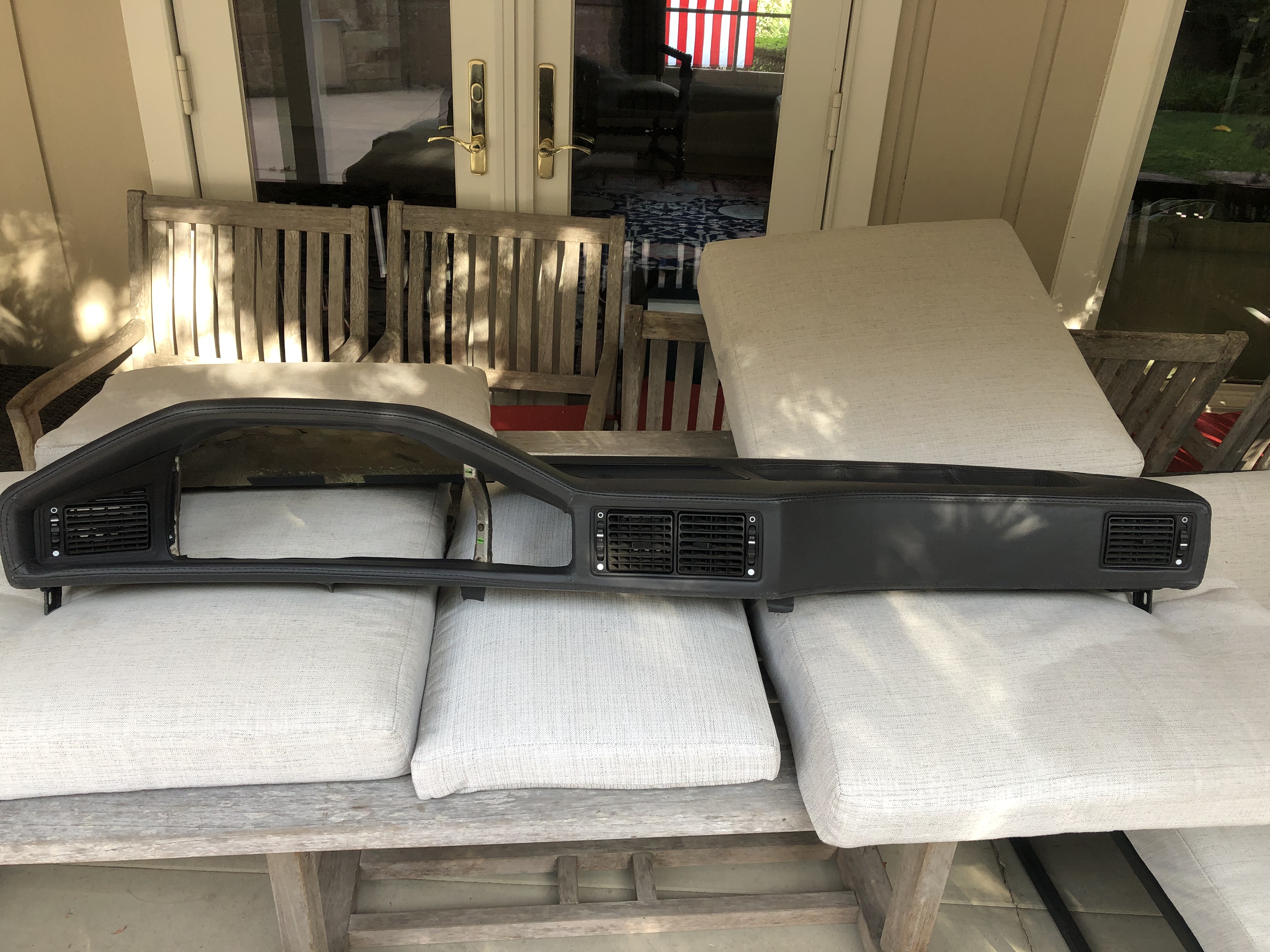