Believe it or not, it's used.

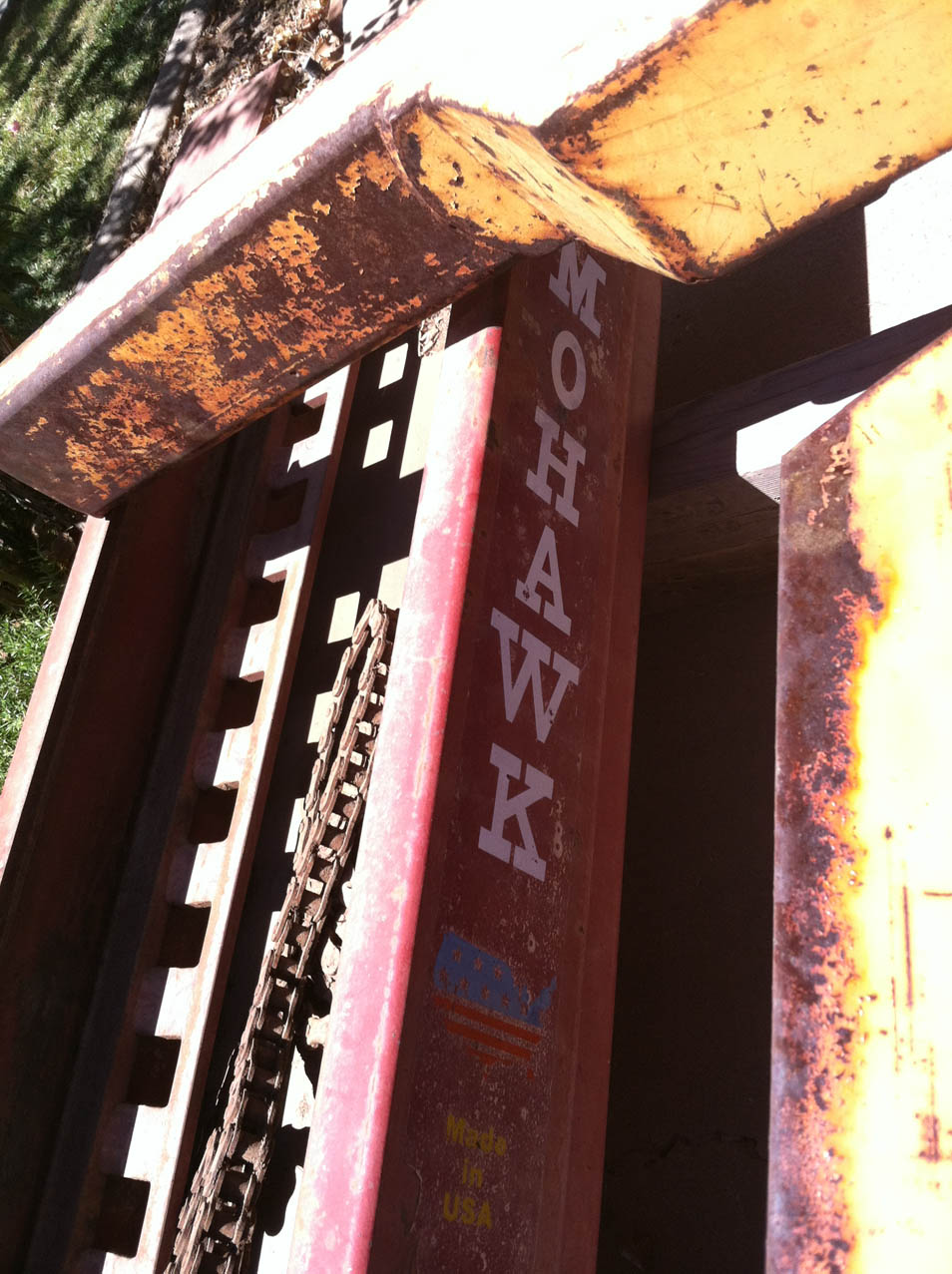
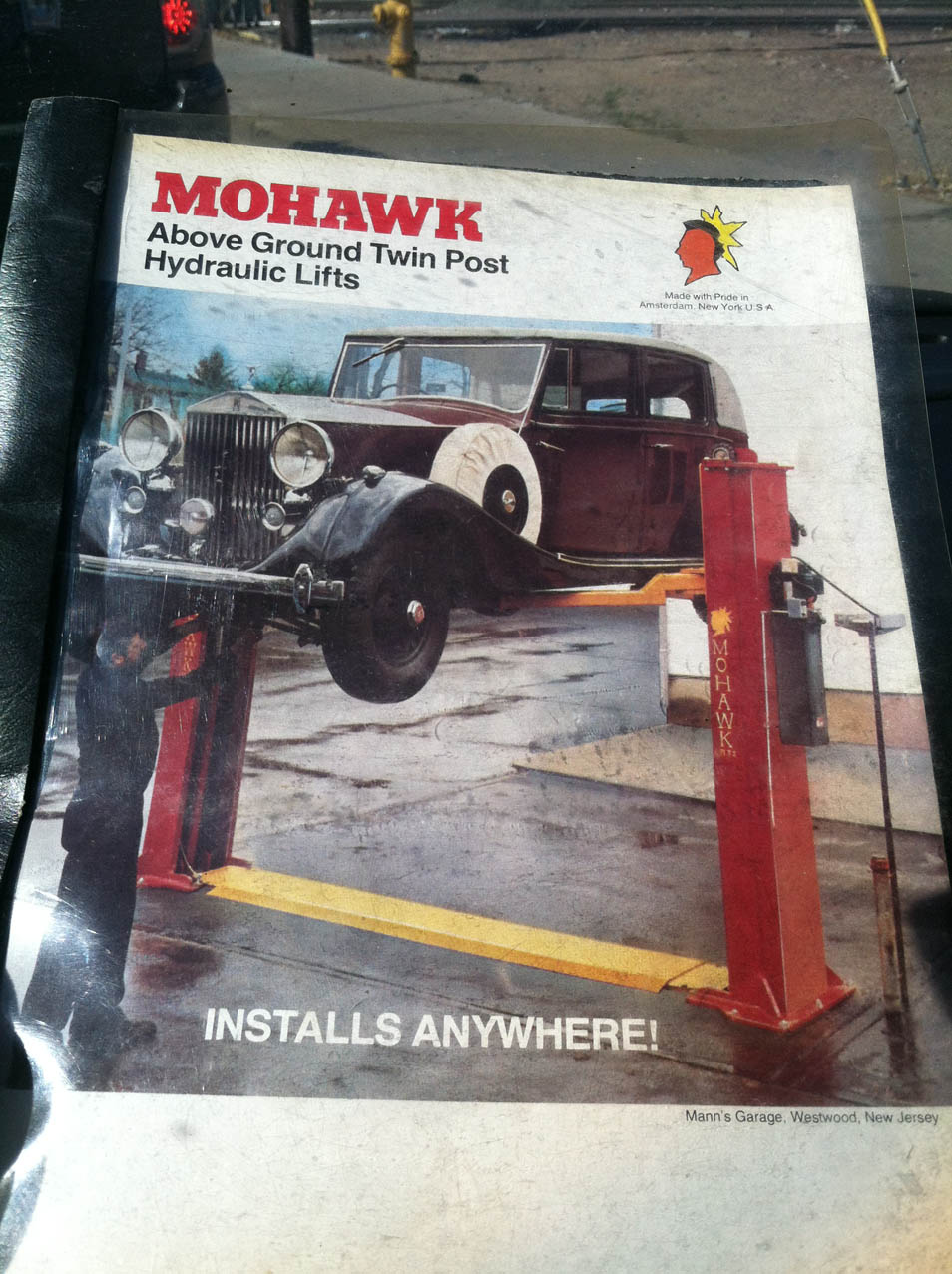
It only weighs 2400 pounds.
It's a Mohawk TP-9. A 9000 pound capacity lift which went into production in 1981. The serial on this one puts it around 1987.
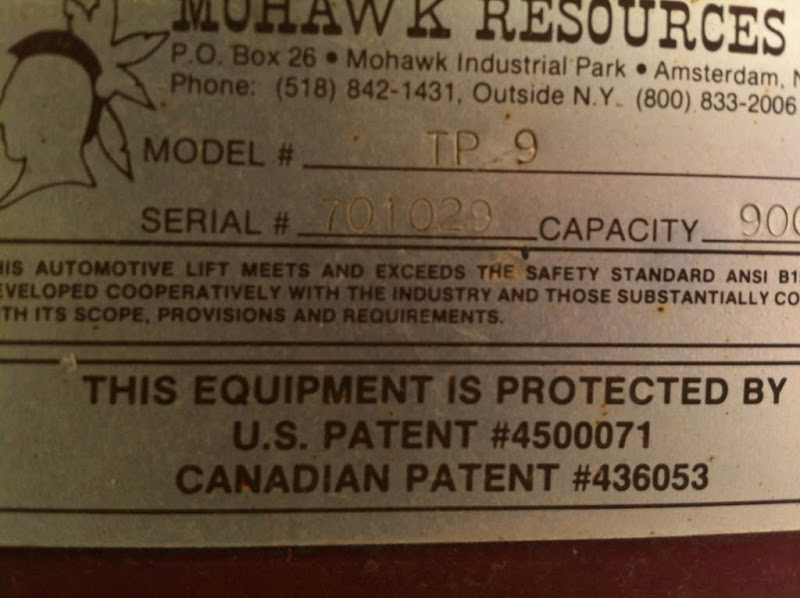
I purchased it from a guy on Craigslist who gave me varying stories on "we're selling the house" and then "I'm moving into the house." Kinda weird. Anyway, his girlfriend (she was pushing 60) owned the lift. Her late husband purchased it from a shop to put up on the side of their house and never got to it, so it sat there.
Here, actually:
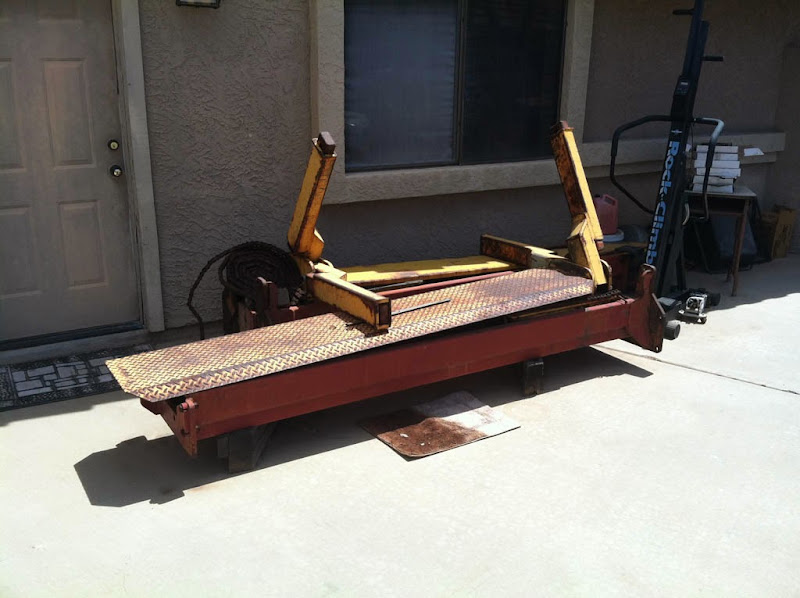
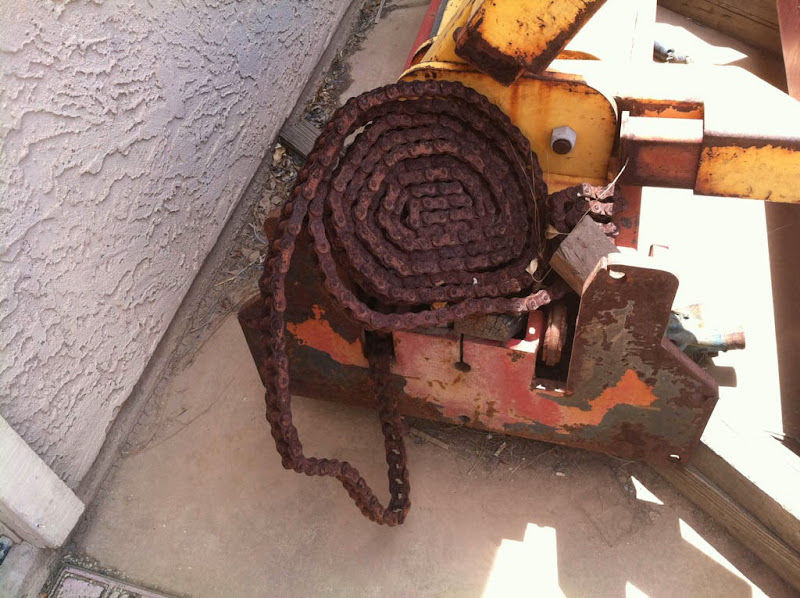
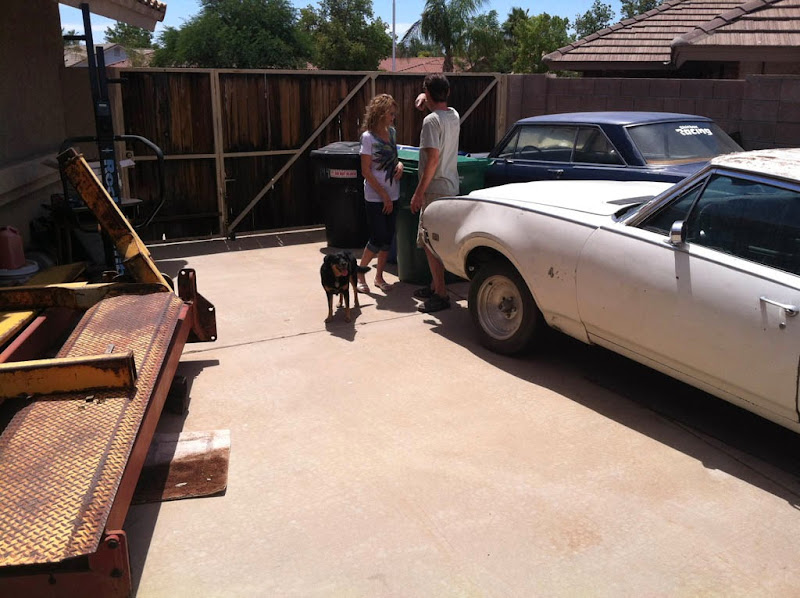
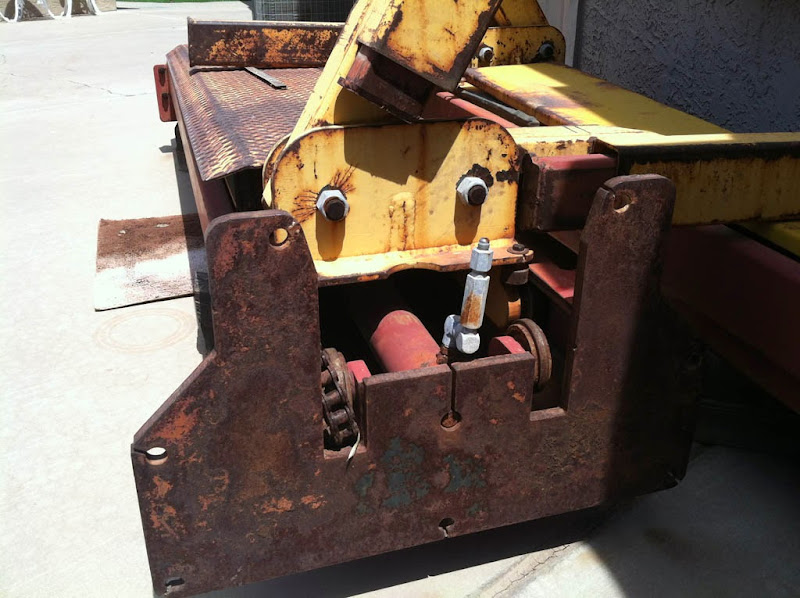
The local dealer was at first reluctant to help me and it took some convincing that this was in fact a Mohawk lift (today's Mohawks are hydraulically-equilized - I'm happy with the chains, thank you very much). Fortunately, after a bit of further convincing they helped me move it from Mesa, AZ to my house, where it has sat for the last six months or so.
All of the rollers and chains were in less-than-functional condition, and I figured given that I wasn't ready to install this thing, I could take my time and work on it myself.
I started by removing the arms since they were somewhat obtrusive. Then I worked to get the carriages off.

With them out of the way and the circlips off, I could then get to the cylinders.
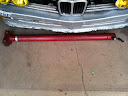
There are six chain rollers and eight carriage rollers. Each of them has a bearing. New from the lift parts suppliers, these run about $80. $90 for the chain rollers. Yeah, so looks like there's a bearing in there, eh? Got the number off of the bearing (a shielded part made by a company called URB in Romania). They didn't move too well.
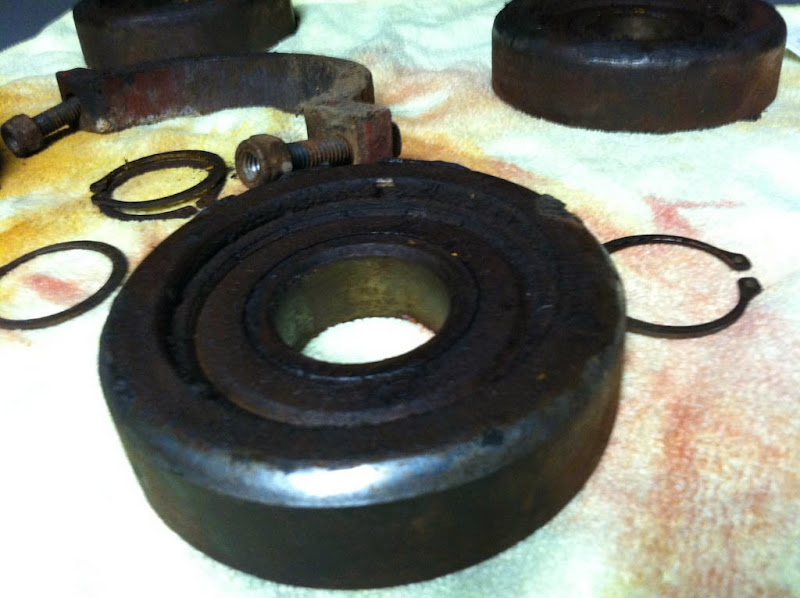
The new lifts come with double-sealed bearings, so I ordered some from eBay. They're made in China, which wasn't something I was terribly excited about but I haven't read much negative about them.
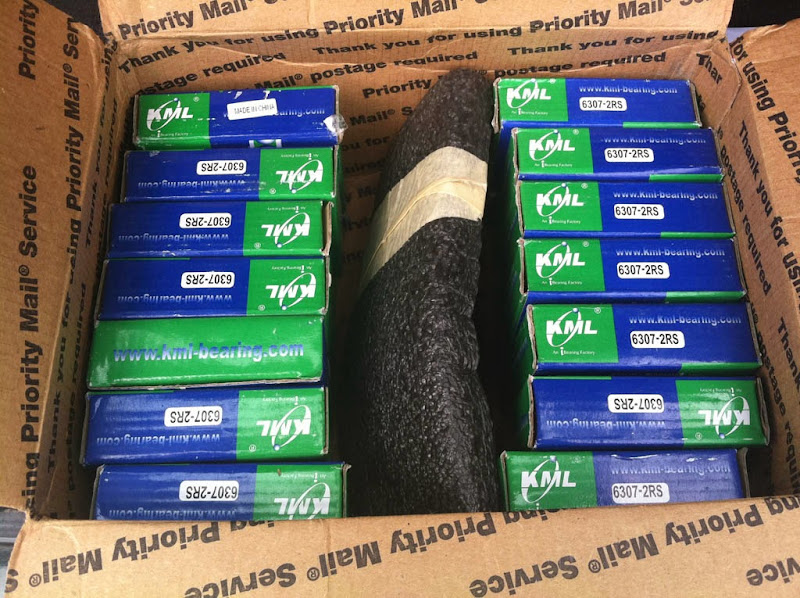
I pressed the old bearings out using my shop press.

Then life got in the way and it's pretty much been sitting since then.
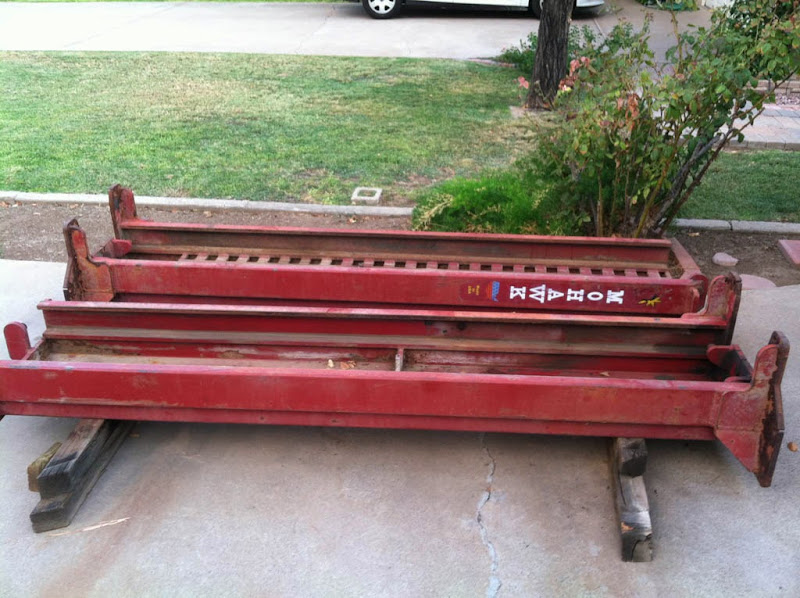
I am well-loved by my neighbors.
Fast forward to December 10. I was coming home in the evening and noticed a neighborhood a 1/2 mile from me was undergoing work for new sidewalk "intersection ramps" that meed ADA specs along with new drainage passages in the intersections. Didn't look like they were totally finished. Great. Looks like the same company that had done similar stuff in my neighborhood and also did a few driveways while they were here. I talked to the homeowners and each were very impressed with the work and inspecting the concrete having been in just over a year, it looks great, as does everything else these guys did sidewalk-wise.
The next morning, I was doing some work at the house and saw a cement truck heading down there. I got in the car and drove down to talk to the guys. Gave them my address and told them what I was looking for.
They came by to see this:
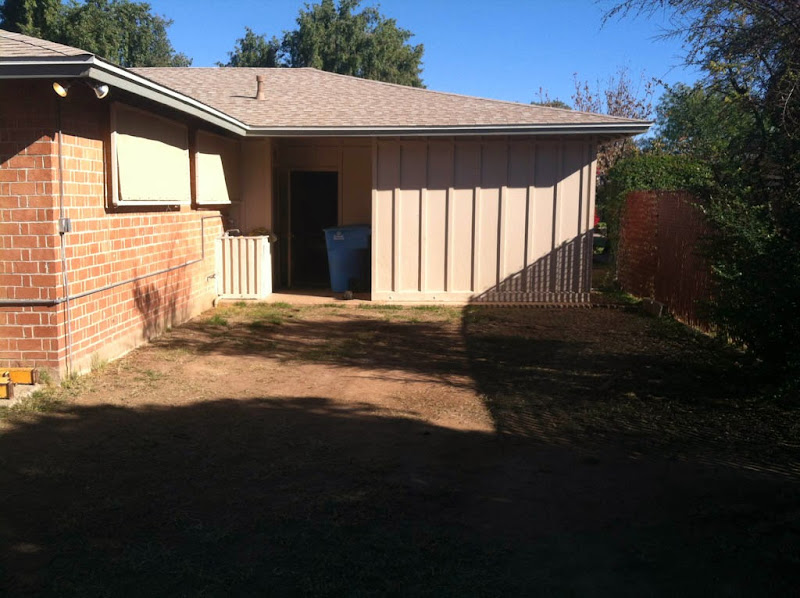
I explained I was looking for. Spec was 4.5" of 4000psi, which I was assured would be sufficient for my purposes. Thanks to my parents getting involved, it ended up being 19x19 4000psi 6" deep with remesh for reinforcement (rebar was not advised by the lift installer, though my dad was pushing for it). Of course, I was on my own for the mesh as their company didn't provide it and they also said that when they pour the concrete at the fire stations, they don't use rebar or anything. Thumbs up on that, we're using the mesh. They gave me a price. It was good enough where I was thinking we could go all the way to the gate, but elected to wait with that until this piece is finished.
They said they could start that afternoon.

They were there until about 7pm. They left and came back the next morning to drop off some wheelbarrows as they couldn't get a chute long enough for the pour. They finished grading, tamped the dirt, then cut and measured the mesh so they could flatten it out.
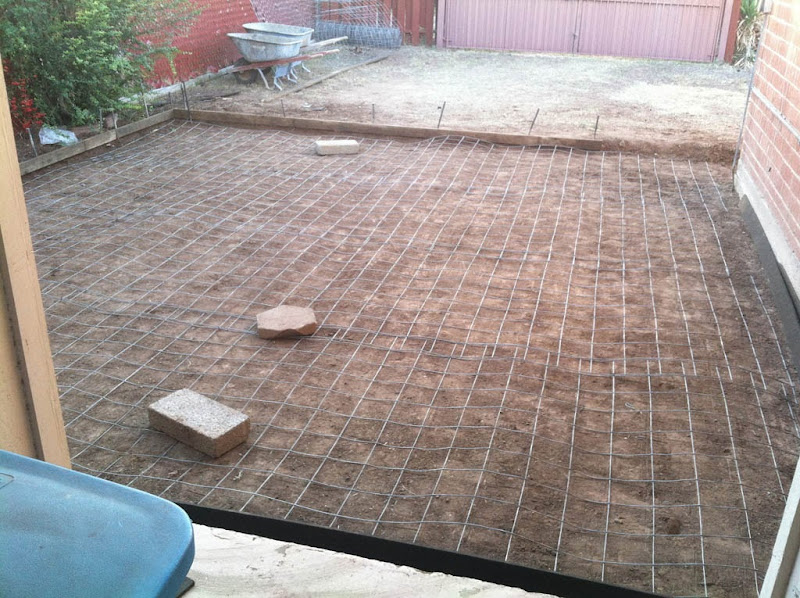
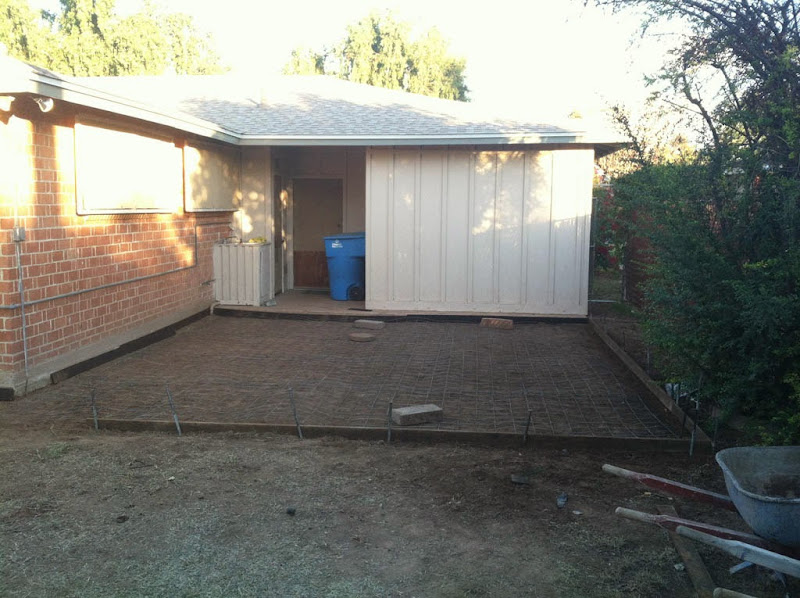
I had them go a bit deeper on the edges. If I didn't, my father wouldn't stop talking about it. Of course, he wouldn't actually talk to the people doing the work, so it got a bit confusing. I finally had my mom make him come over to make sure everything was done the way HE wanted it.
He was fine and ended up being very impressed with the people I enlisted to do the work.
Oh noes! The truck just showed up.
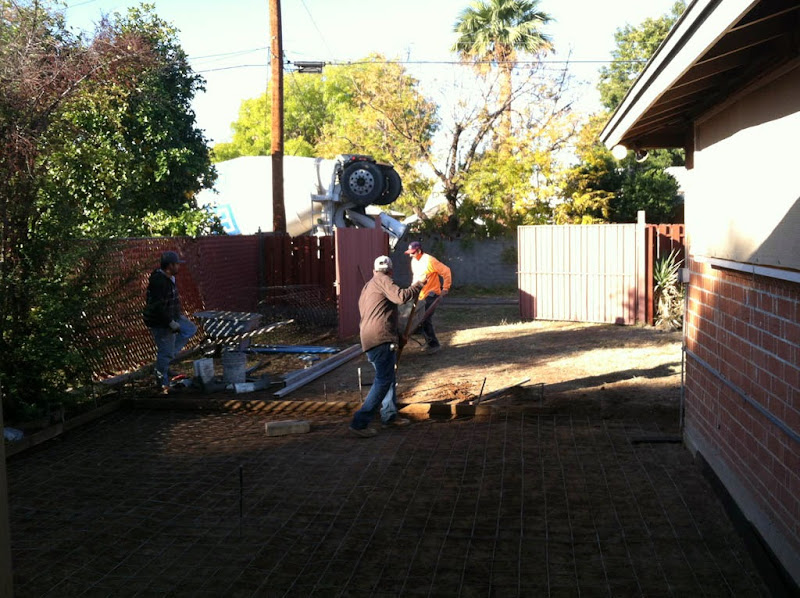
They're pulling the mesh up manually. This guy did a very good job of getting it centered and it certainly seemed to hold it's position.
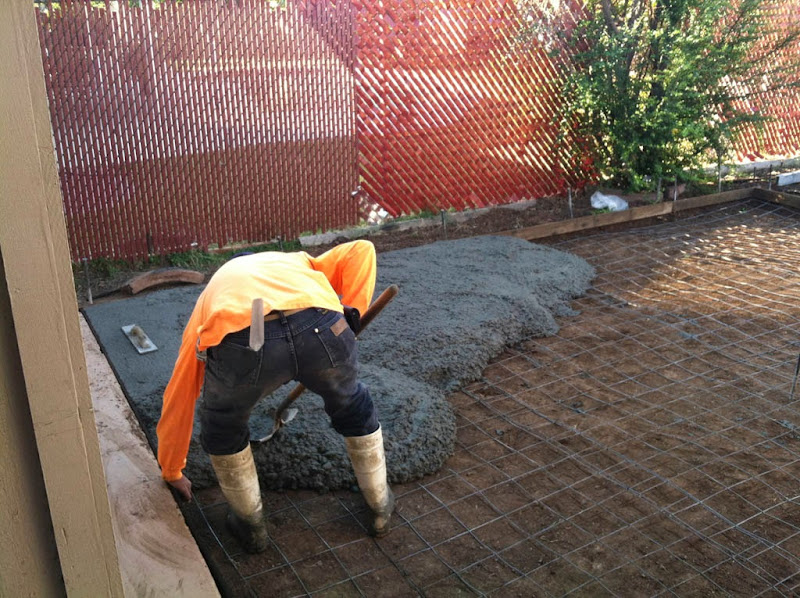
Control joints going in. I was going to have it saw-cut, but decided that if these joints ever became a problem rolling things around, I could fill them with a sealer, but I need to wait for the slab to go through most of it's shrinking phase. The crew were going to do just one each direction, but I explained my life-long love affair with Tic-Tac-Toe, so it had to be done this way.
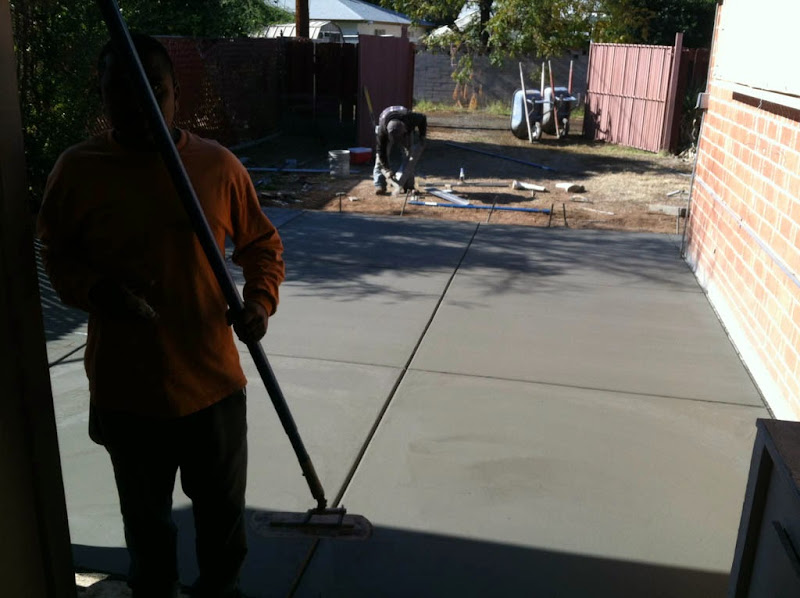
Actually, after measuring the center of gravity on the cars I'd use the lift for, then accounting for sufficient space in front, the lift will sit dead-center on the slab. Since anchors cannot sit less than 6" from a joint, that left us with this setup.
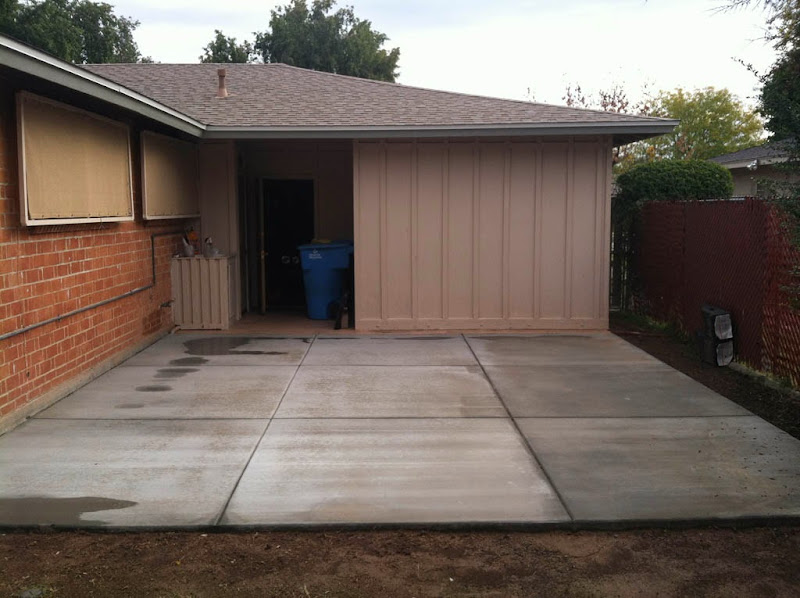
I've been watering it a lot.
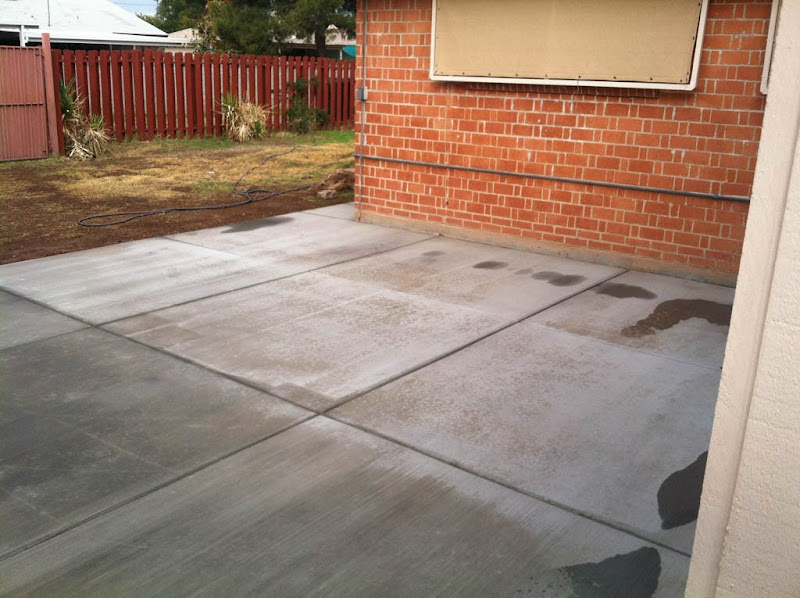
Minimum cure time is 28 days before installing the lift, but I'm going to make sure all of my ducks are in a row first. I'm going to take the cylinders and the pump to a hydraulic shop recommended by the dealer (right down the street from my house

Once the lift is in, I'll work on getting a shade device in place. Of course, like every project, there's much more to do!