Thermal Management
Posted: Jul 18, 2017 12:18 AM
In my quest for cooler charge air, I've upgraded most of the water to air components in my system. Last winter I installed a high(er) flow electric water pump designed and fabricated a larger reservoir with welded in AN bungs and a large screw on cap. I wanted a larger and more efficient front mount heat exchanger (radiator) as well. I've run quite a few different set-ups over the past 10+ years: first an oil cooler, then a hacked up civic radiator then a smaller cheapo chinese radiator. They all worked decently and kept MATs reasonable low but they were all kinda hacked to make it fit either from a mounting or routing standpoint. I looked high and low for a prefabbed unit but couldn't find exactly what I wanted. I'm sure somewhere, there is a catalog unit that is pretty close, but I knew what I wanted so I decided to make it myself.
I've wanted to undertake this project for a little while but haven't had the equipment to do so myself until this past year. In the past 12 months I purchased an AC/DC TIG welder and a press brake that bends everything from super thin sheet metal to 5/8" thick bar.
I finally had a weekend free from the office so I made some progress:
I started with a 16" (w) x 18" (h) x 2.25" (t) radiator core from Bell Intercoolers. They don't advertise these on their website so it took several phone calls to figure out exactly what they can make. It took about a month for them to get the core in and "make" it. I believe they order core in bulk that is 16" x 2.25" and then cut it to the desired height and then weld plates on the top and bottom.
The most challenging part of this project was that I wanted the inlet and outlet on the same side of the core.
Here is the core next to the existing heat exchanger. The front area is 288 in^2. This is a 100% increase in cooling area compared to the existing unit. As noted it is also 25% thicker.
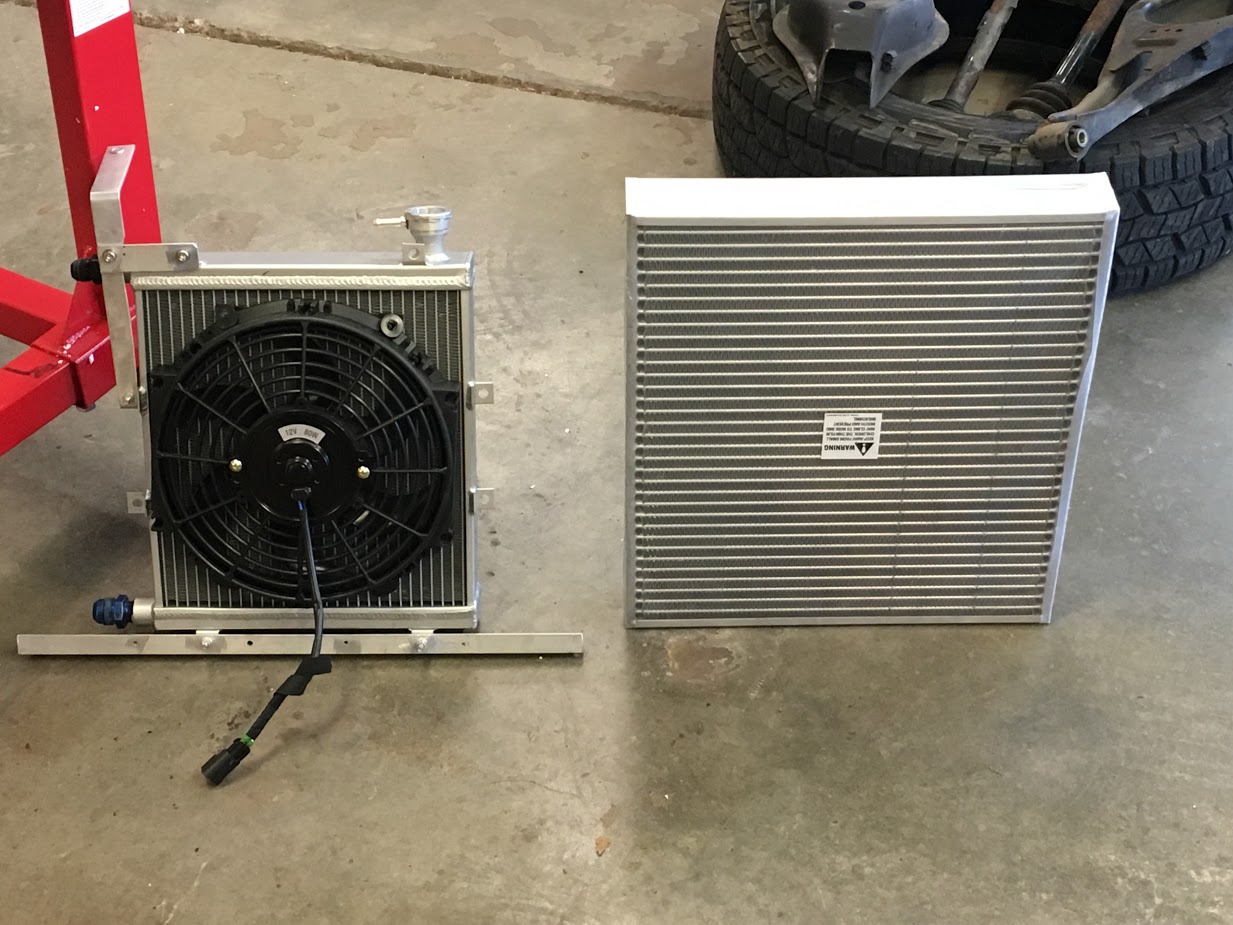
Its tight but it fits pretty nicely without having to cut or mangle the bumper support:
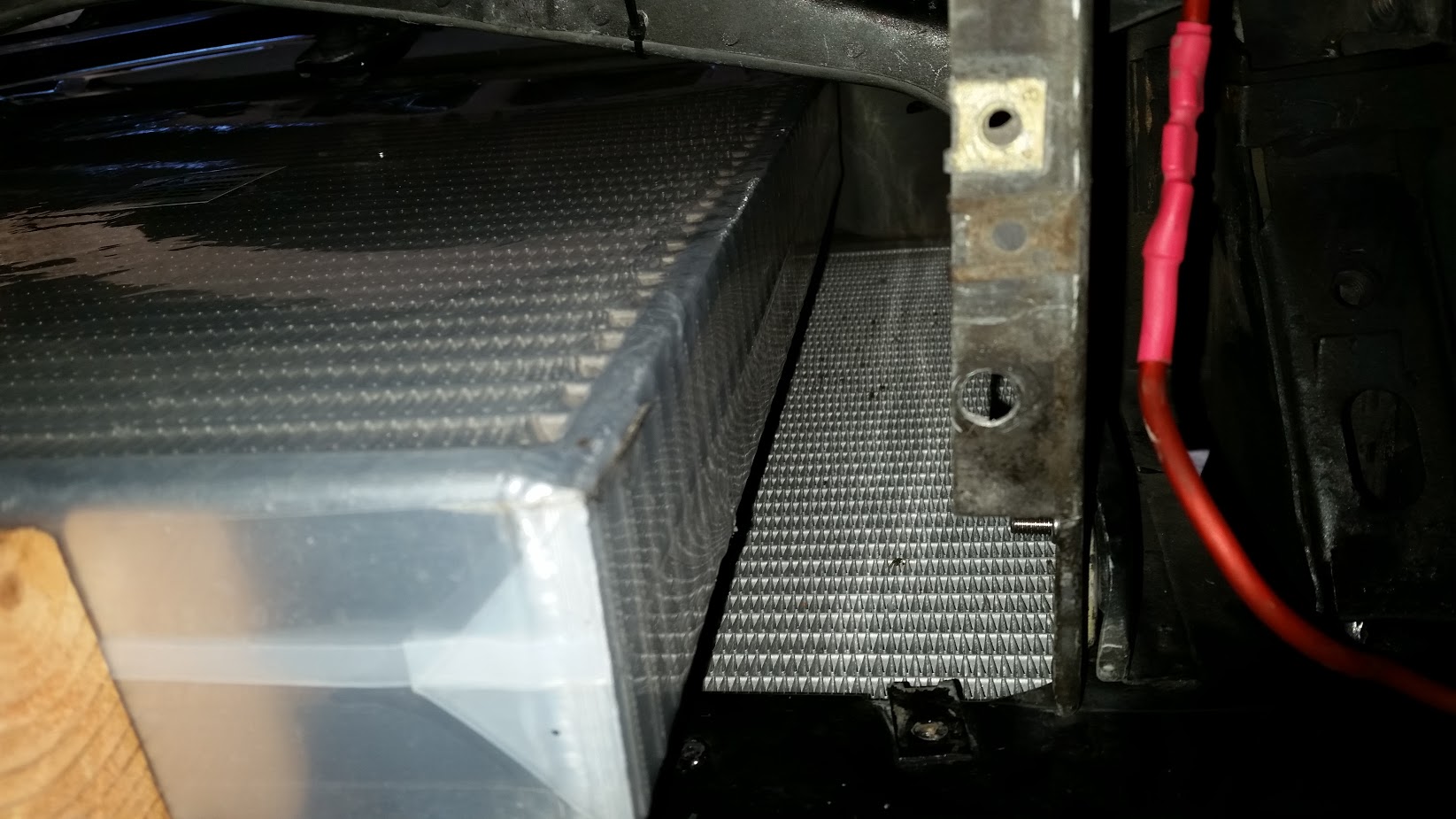
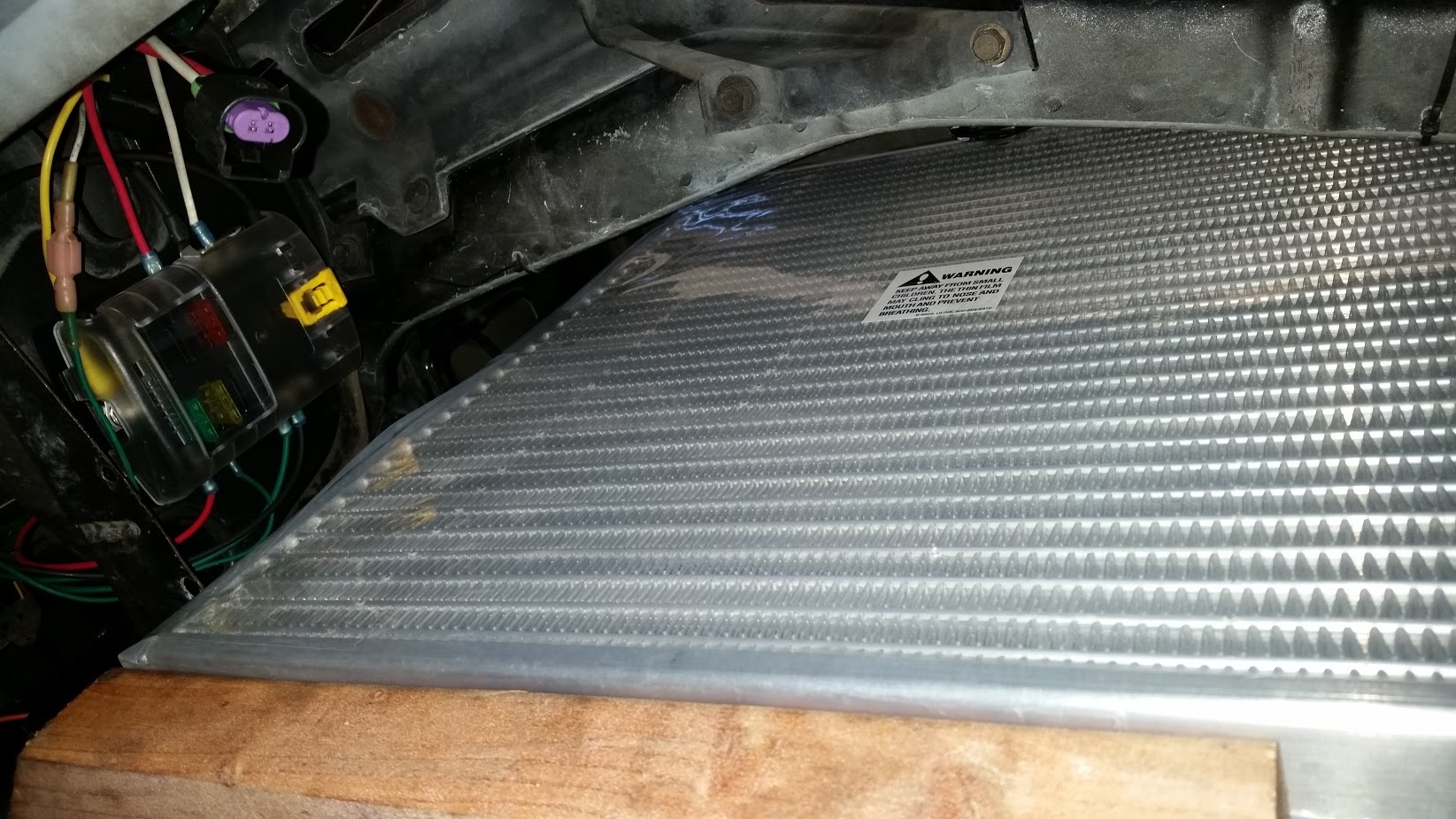
This gave me the opportunity to use my sheet metal bender. I'm pretty happy with the consistency of the bends across 18". I used 5052 aluminum in 1/16" thickness to construct the end tanks.
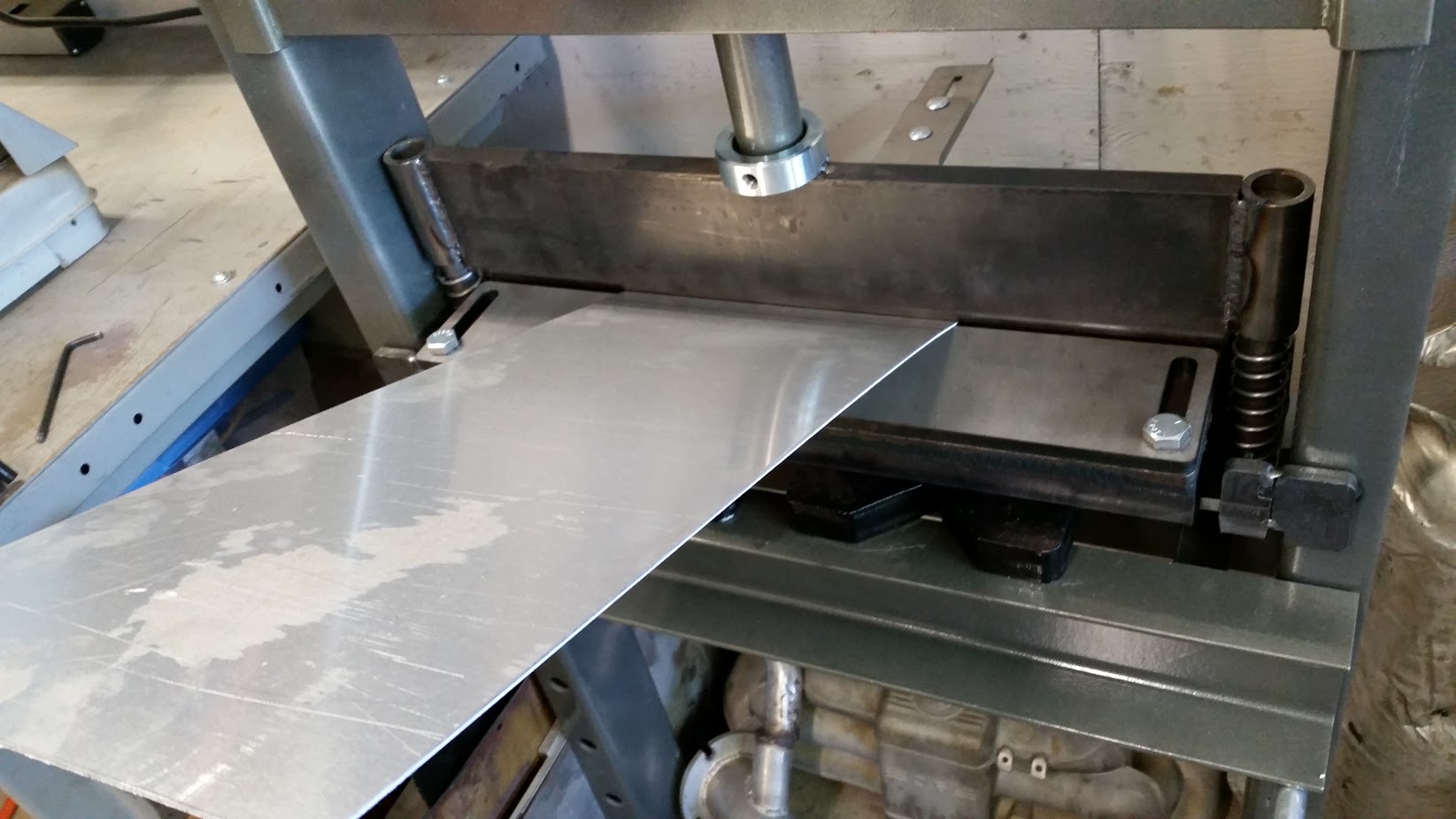
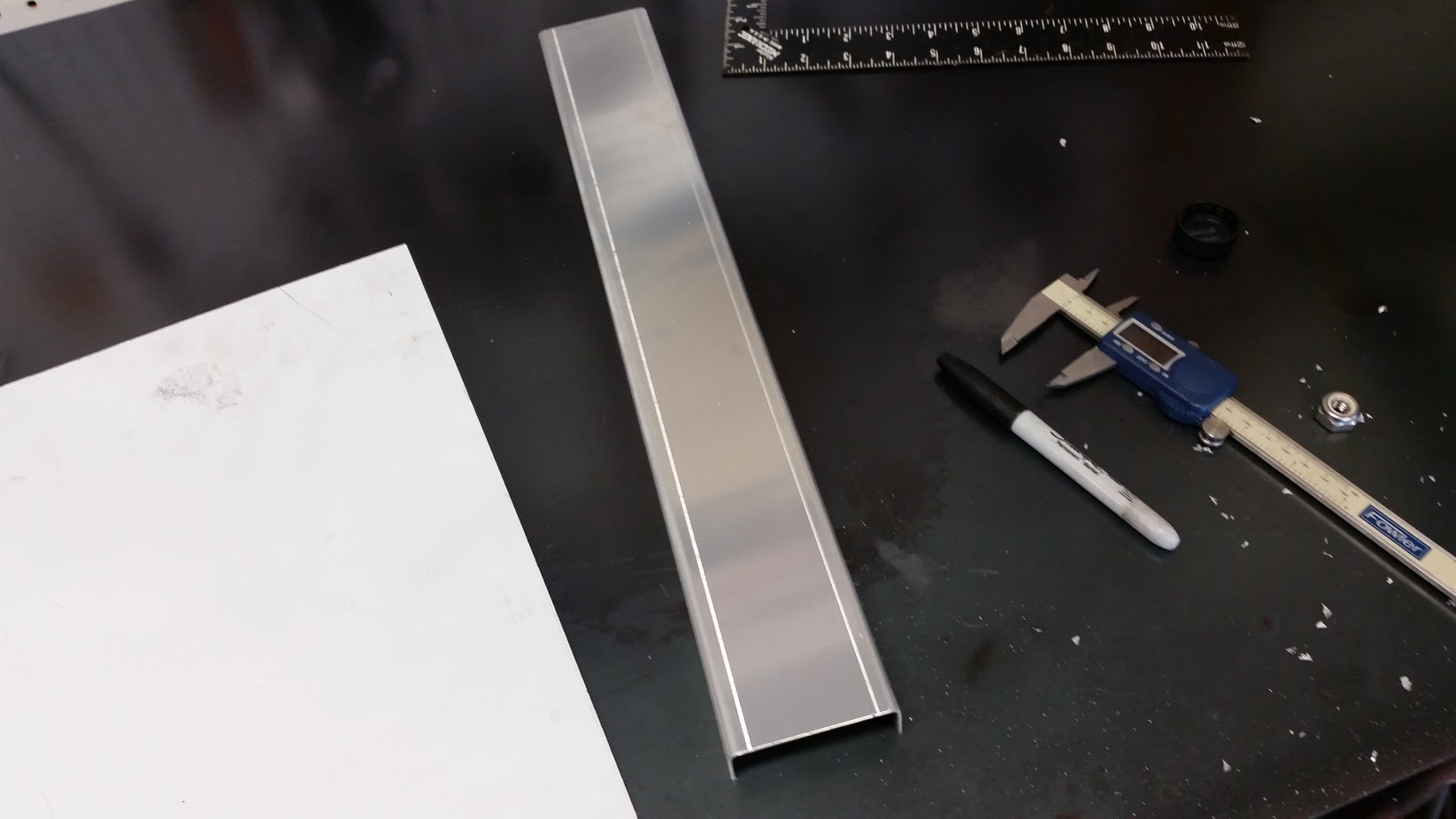
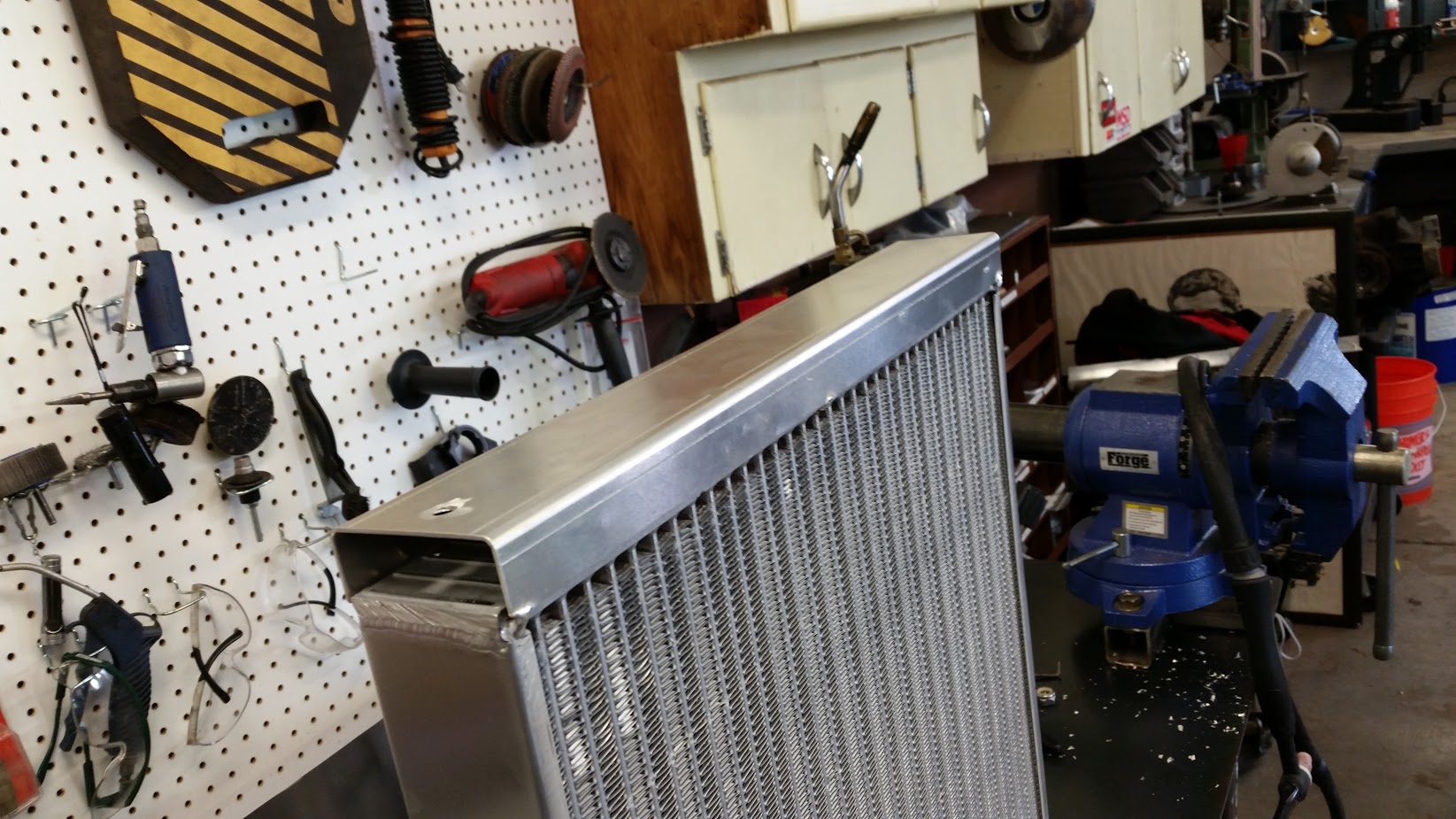
I settled on -12AN fittings as that is the same size as pump.
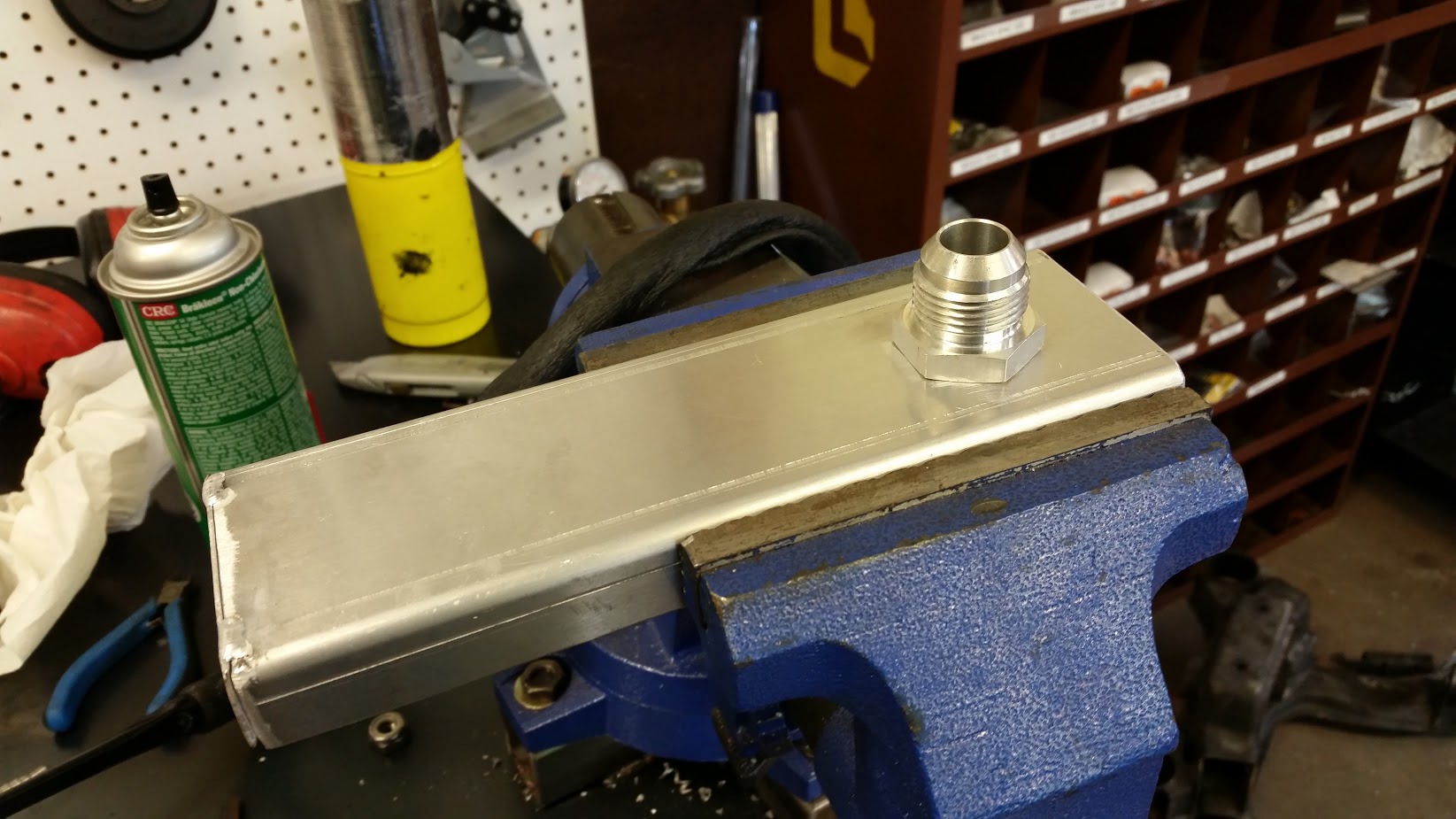
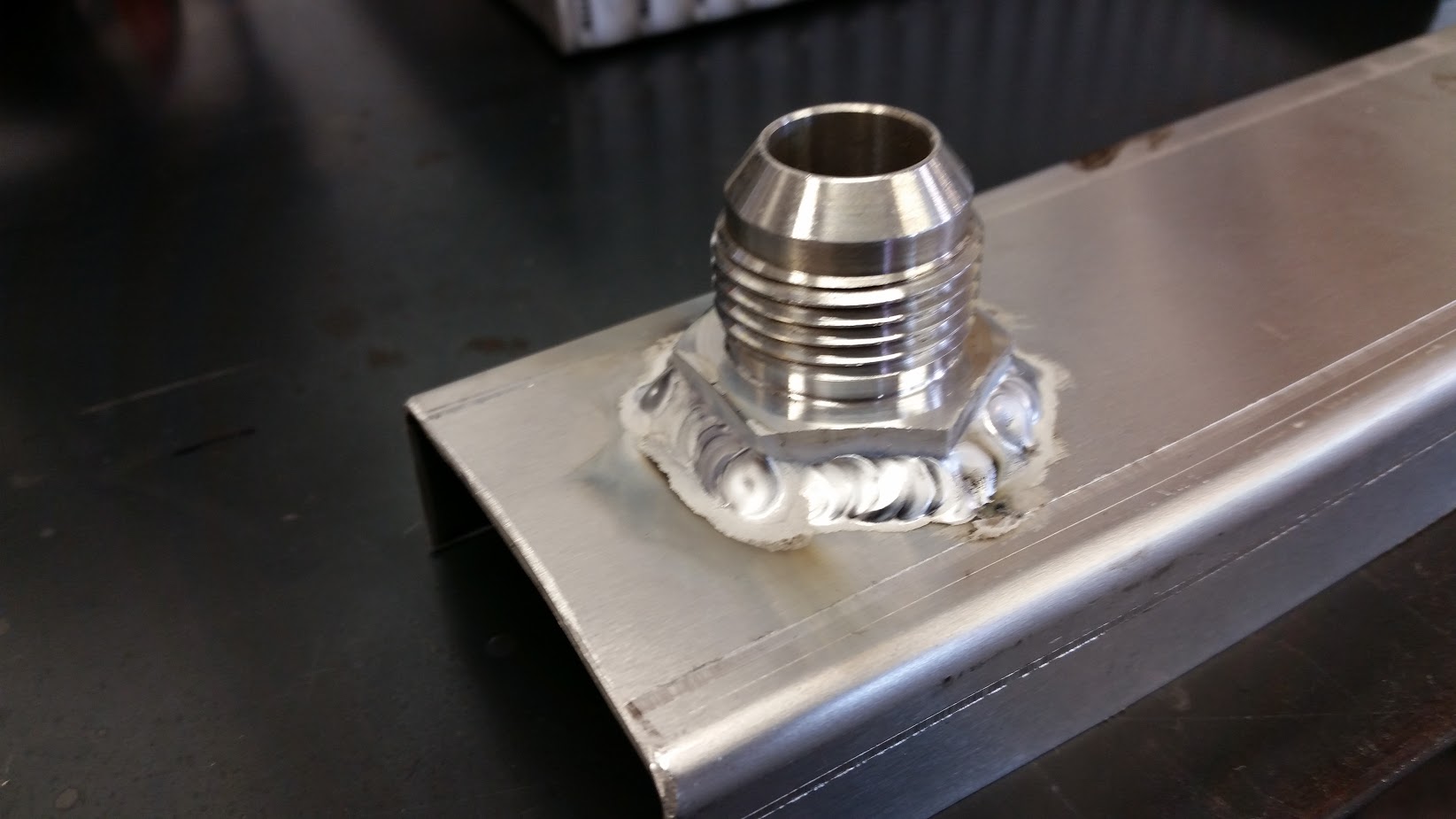
Separating the inlet and outlet tanks on the same side was a little challenging to weld. I had to pump quite a bit of heat into it.
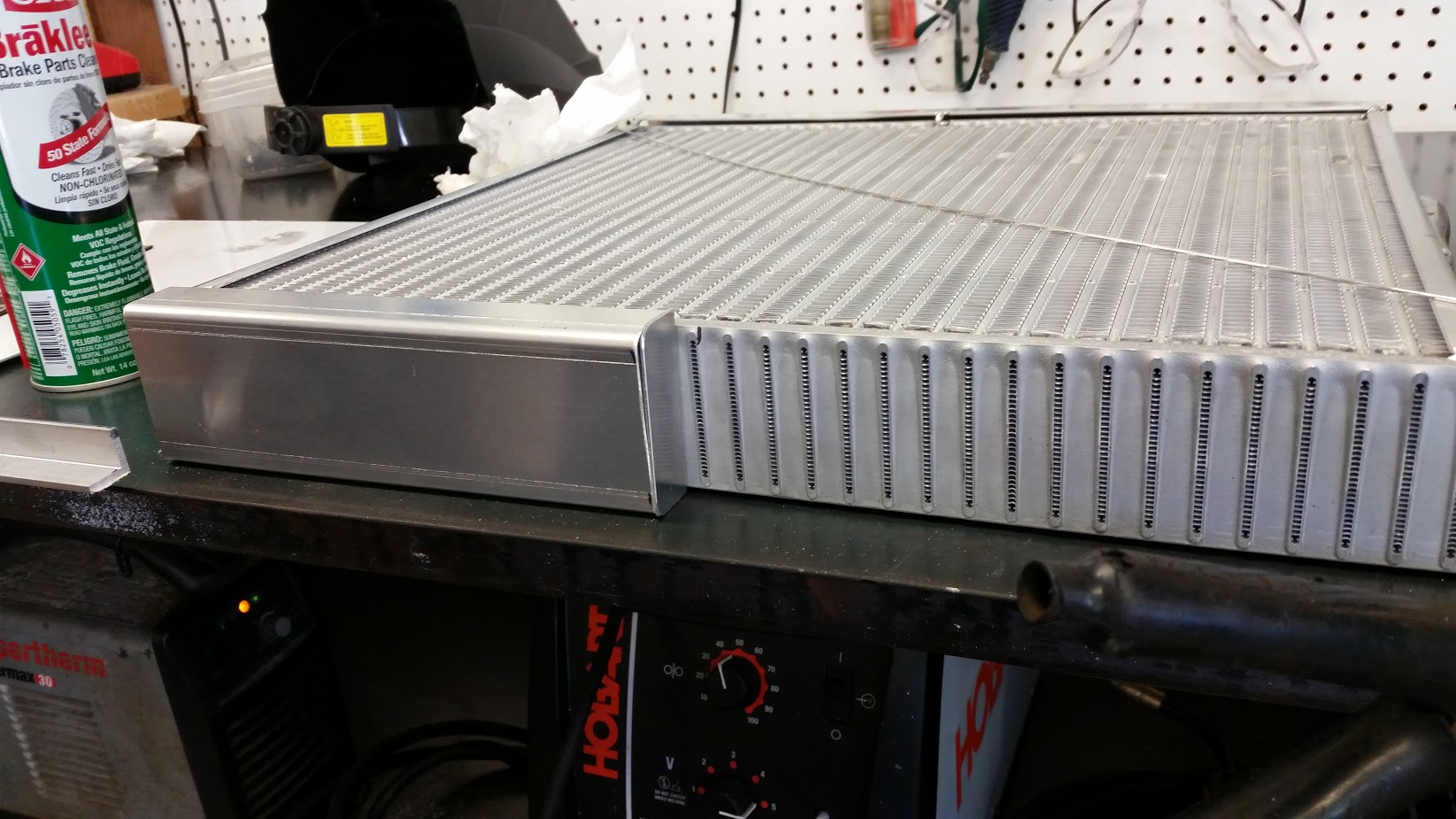

While I was waiting for the welds to cool, I added some gold reflective tape to the bottom of the intercooler. I've never been too sure of its effectiveness but I got it cheap so why the heck not:
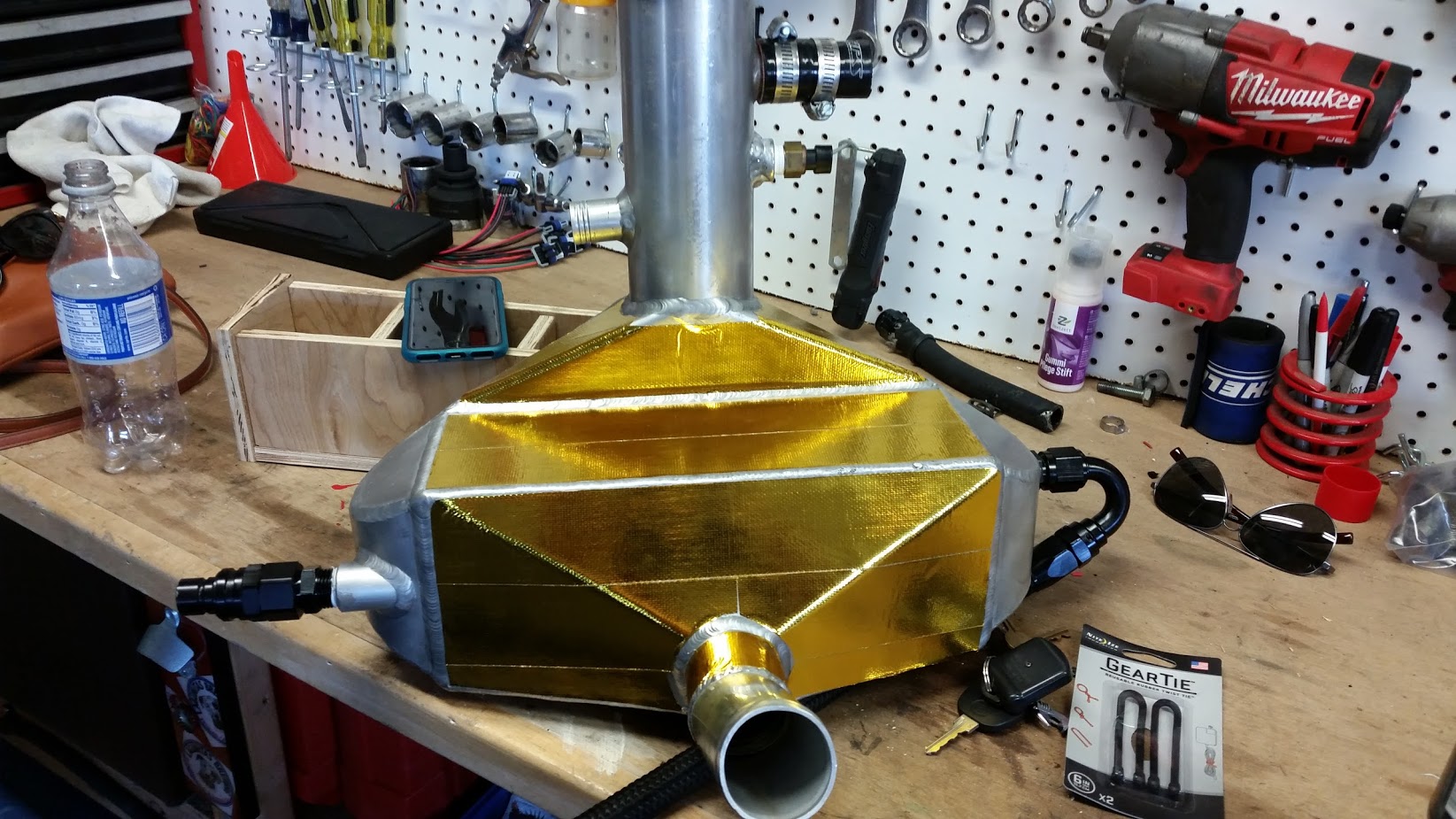
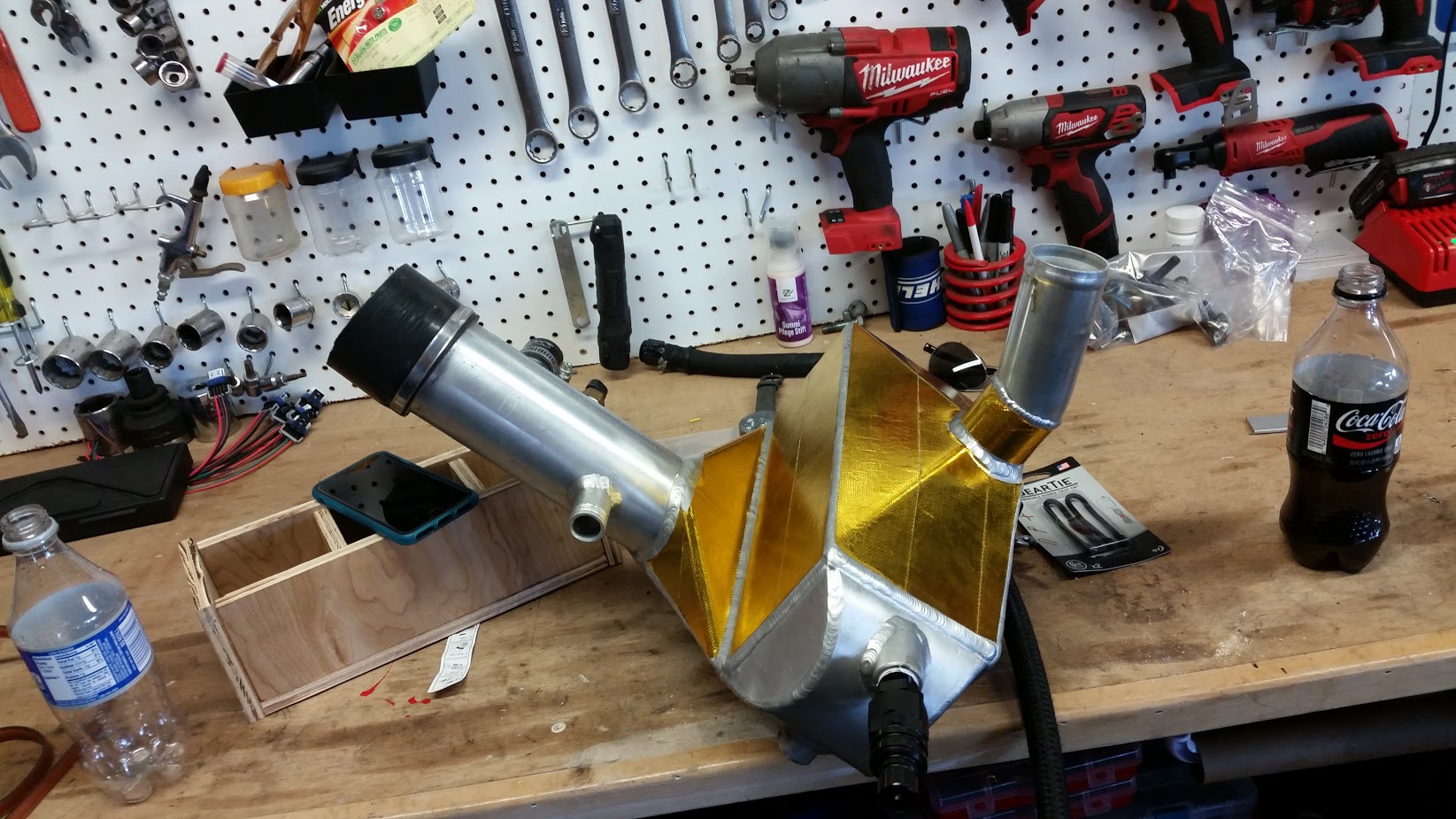
It took a while to chase down some pin hole leaks but I finally got everything to seal with ~20psi of air applied to the drain hole.
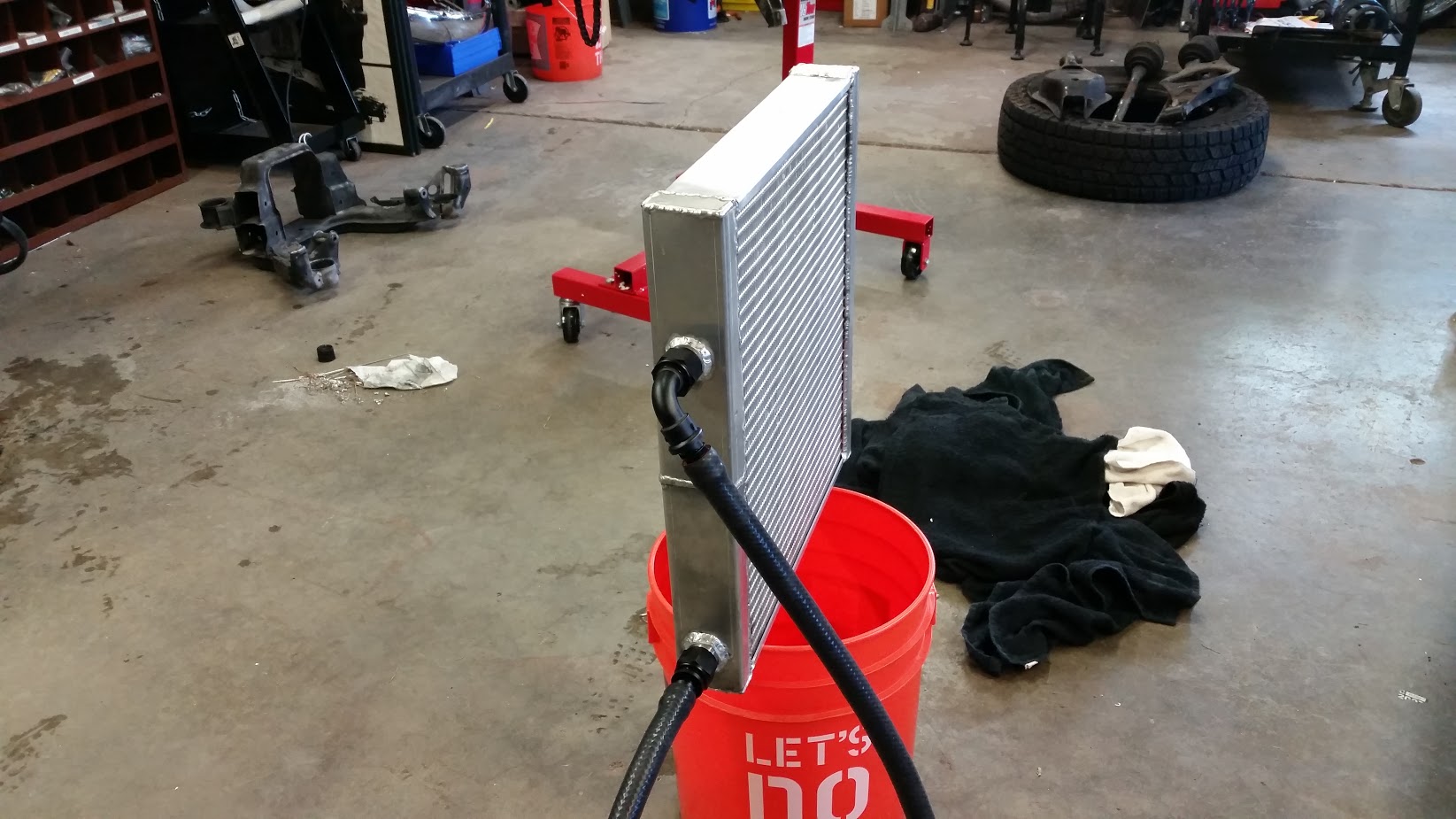
I still need to add a bleed screw to the top of the end tank and then add mounting provisions. Hopefully that gets done this coming weekend. I'll update when I have more to show.
I've wanted to undertake this project for a little while but haven't had the equipment to do so myself until this past year. In the past 12 months I purchased an AC/DC TIG welder and a press brake that bends everything from super thin sheet metal to 5/8" thick bar.
I finally had a weekend free from the office so I made some progress:
I started with a 16" (w) x 18" (h) x 2.25" (t) radiator core from Bell Intercoolers. They don't advertise these on their website so it took several phone calls to figure out exactly what they can make. It took about a month for them to get the core in and "make" it. I believe they order core in bulk that is 16" x 2.25" and then cut it to the desired height and then weld plates on the top and bottom.
The most challenging part of this project was that I wanted the inlet and outlet on the same side of the core.
Here is the core next to the existing heat exchanger. The front area is 288 in^2. This is a 100% increase in cooling area compared to the existing unit. As noted it is also 25% thicker.
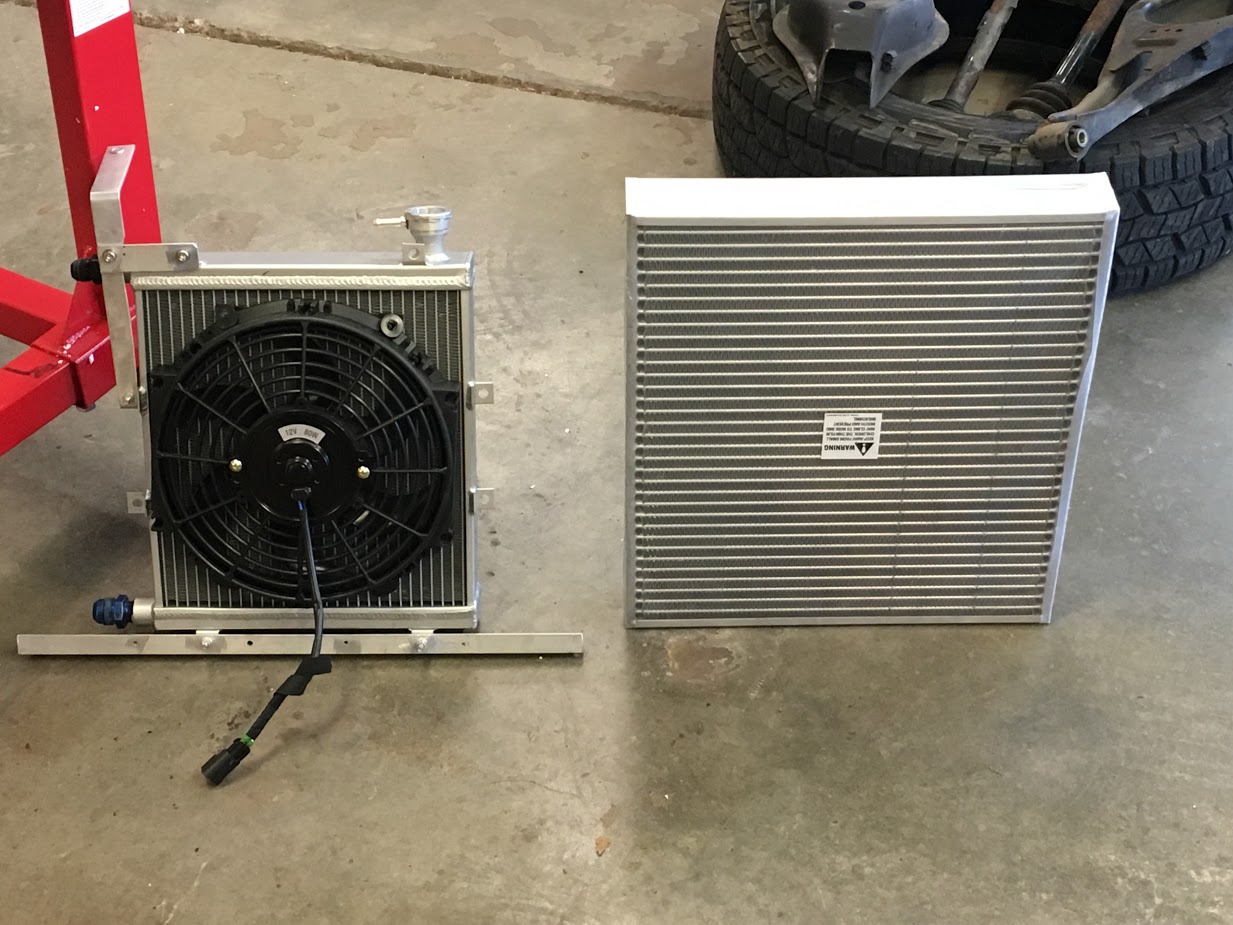
Its tight but it fits pretty nicely without having to cut or mangle the bumper support:
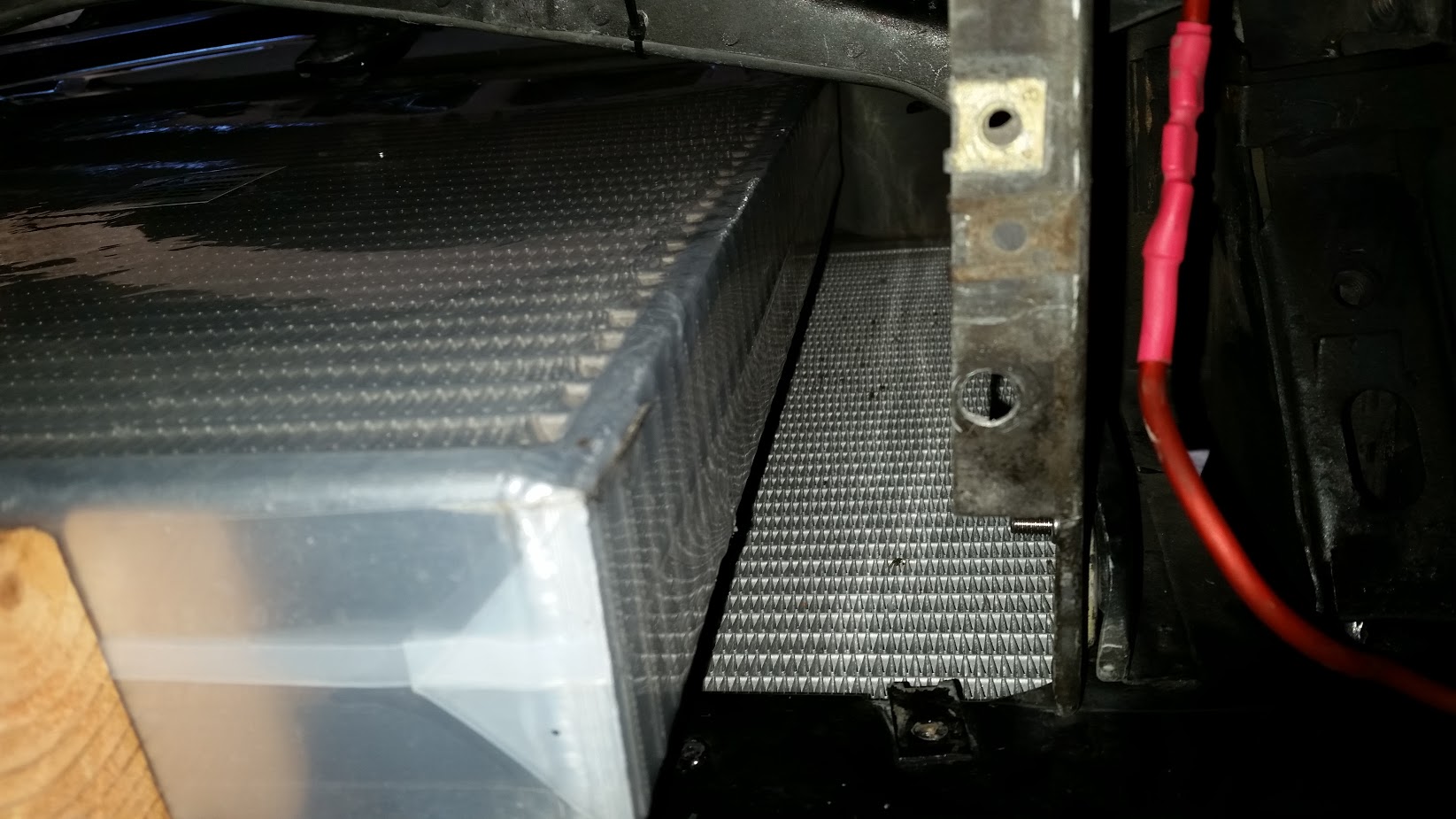
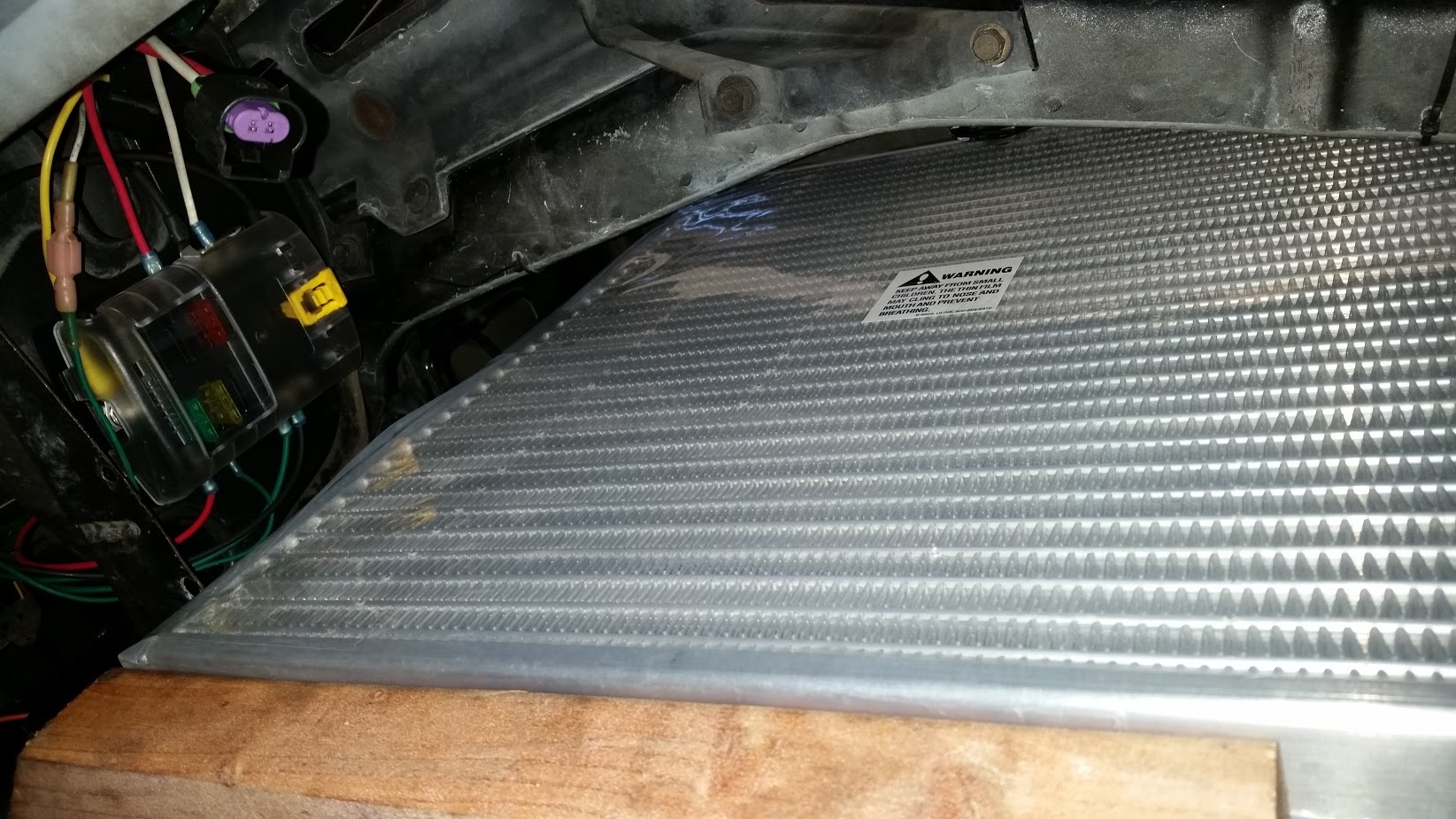
This gave me the opportunity to use my sheet metal bender. I'm pretty happy with the consistency of the bends across 18". I used 5052 aluminum in 1/16" thickness to construct the end tanks.
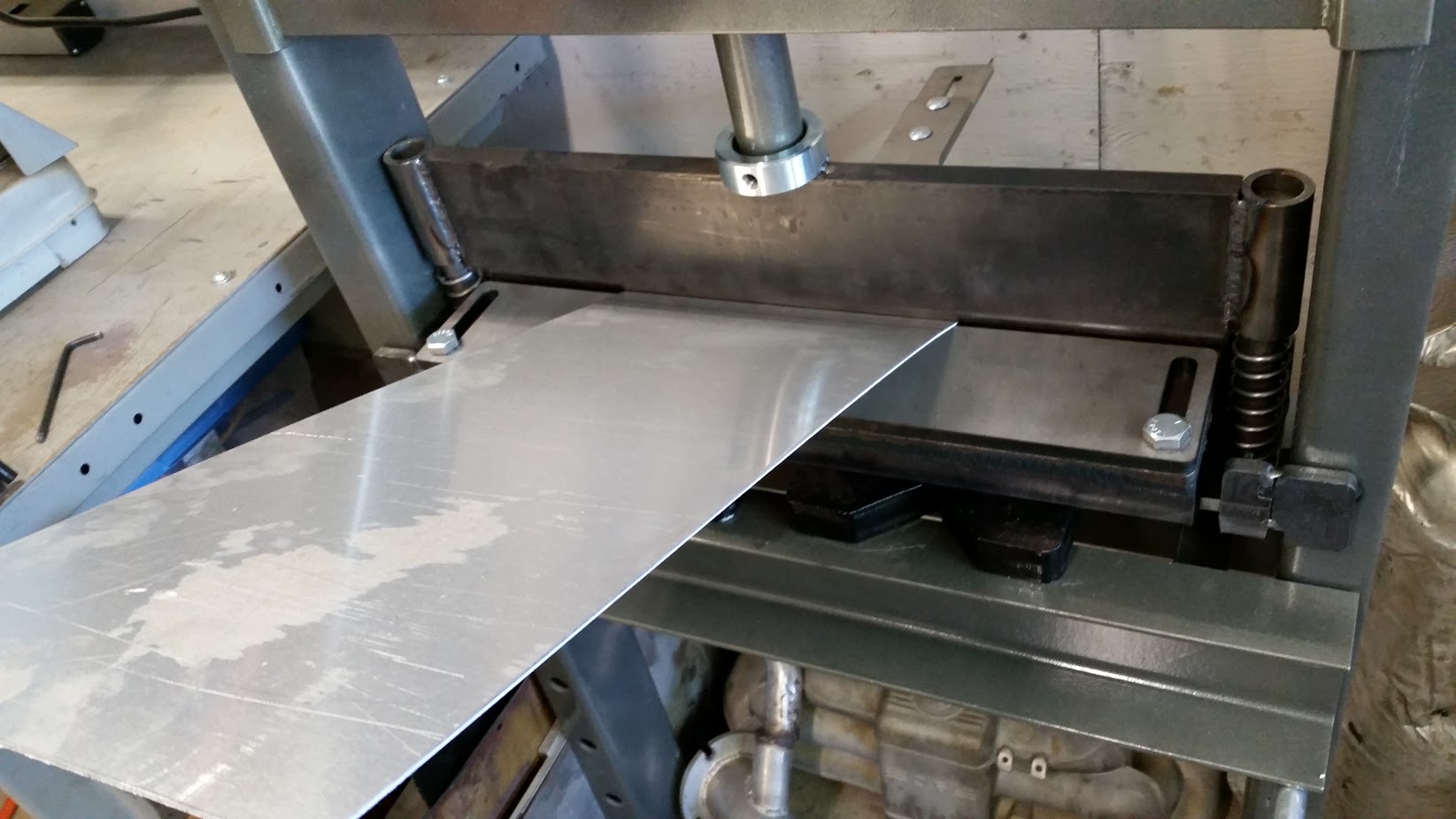
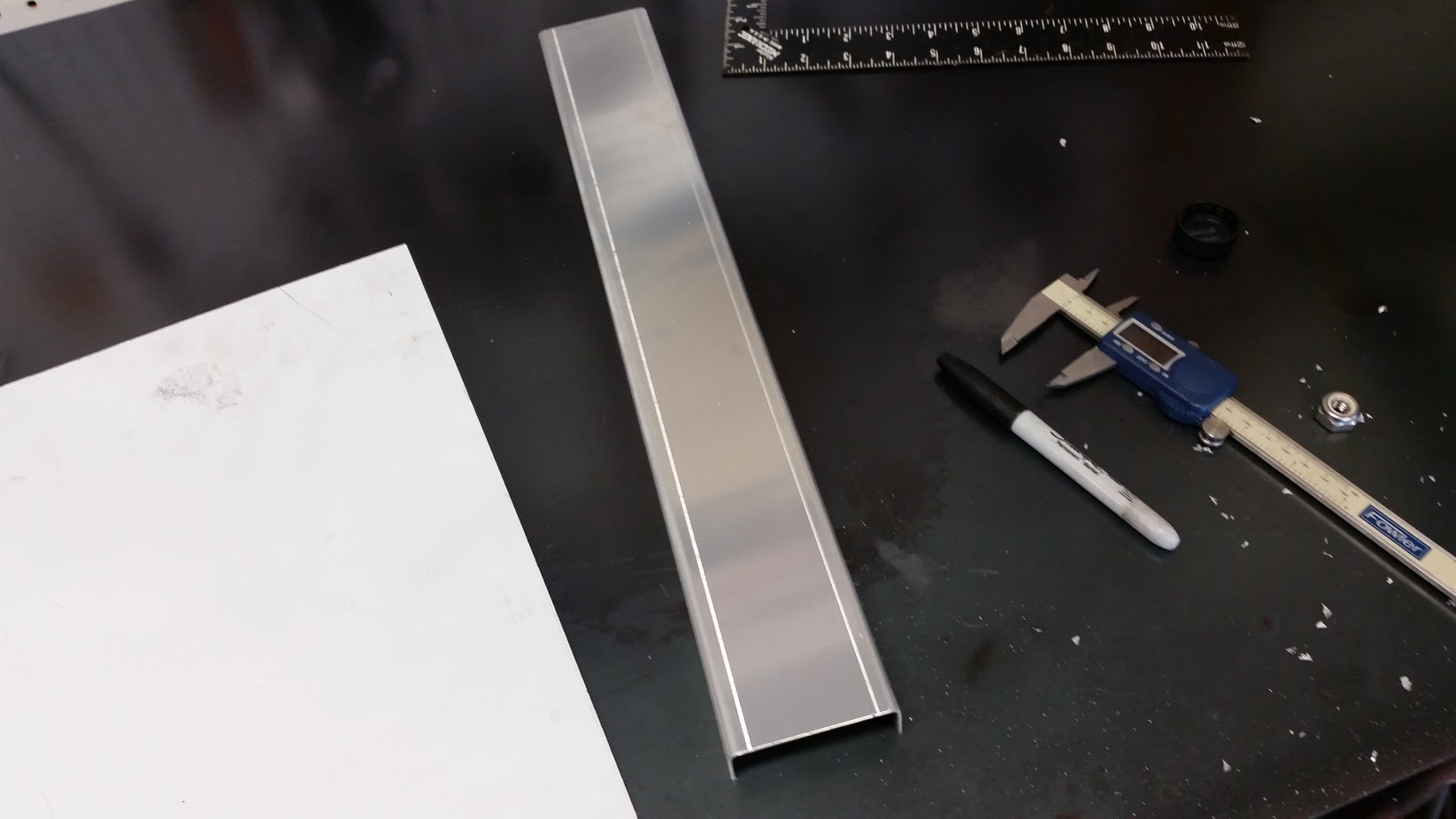
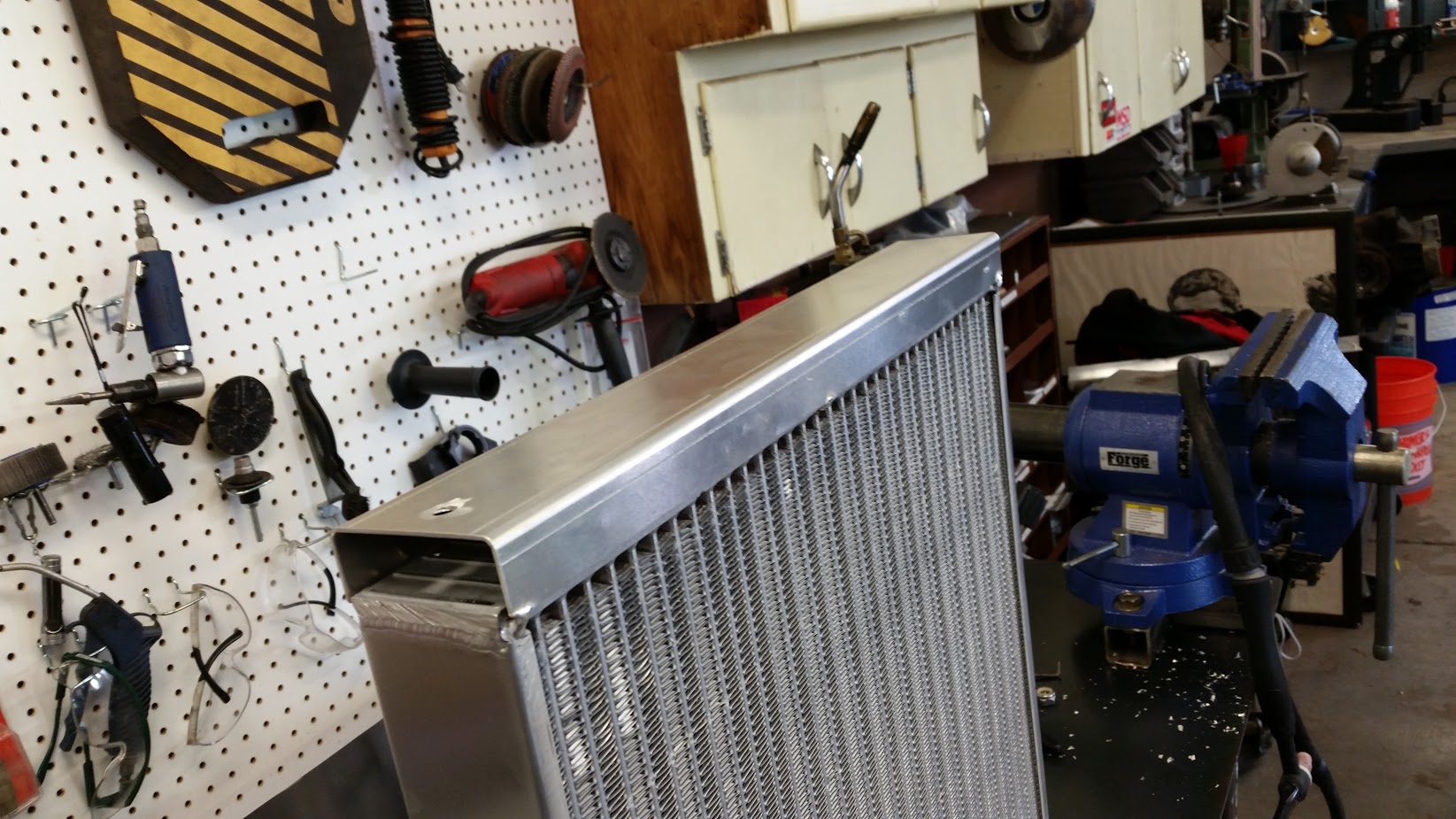
I settled on -12AN fittings as that is the same size as pump.
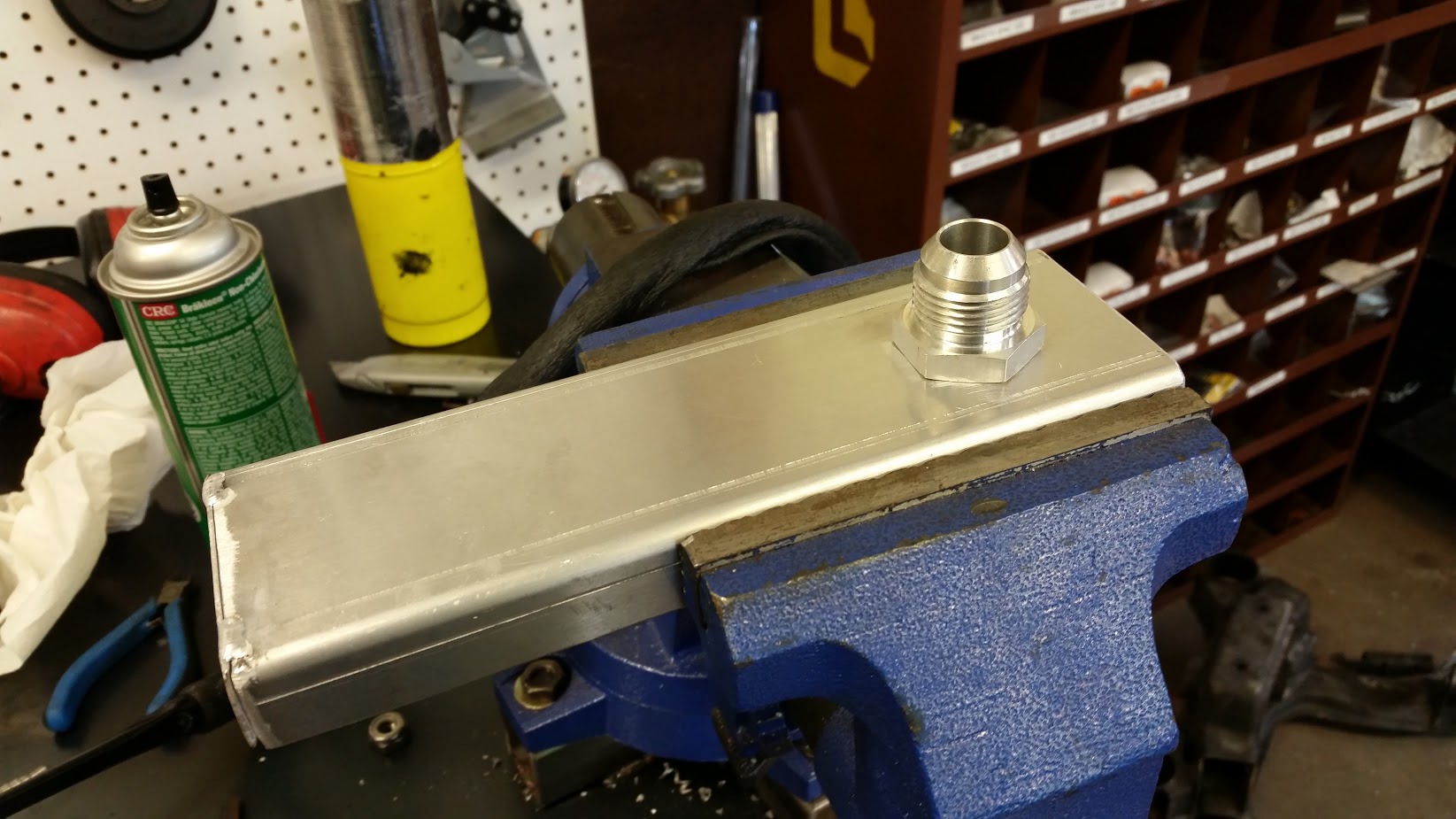
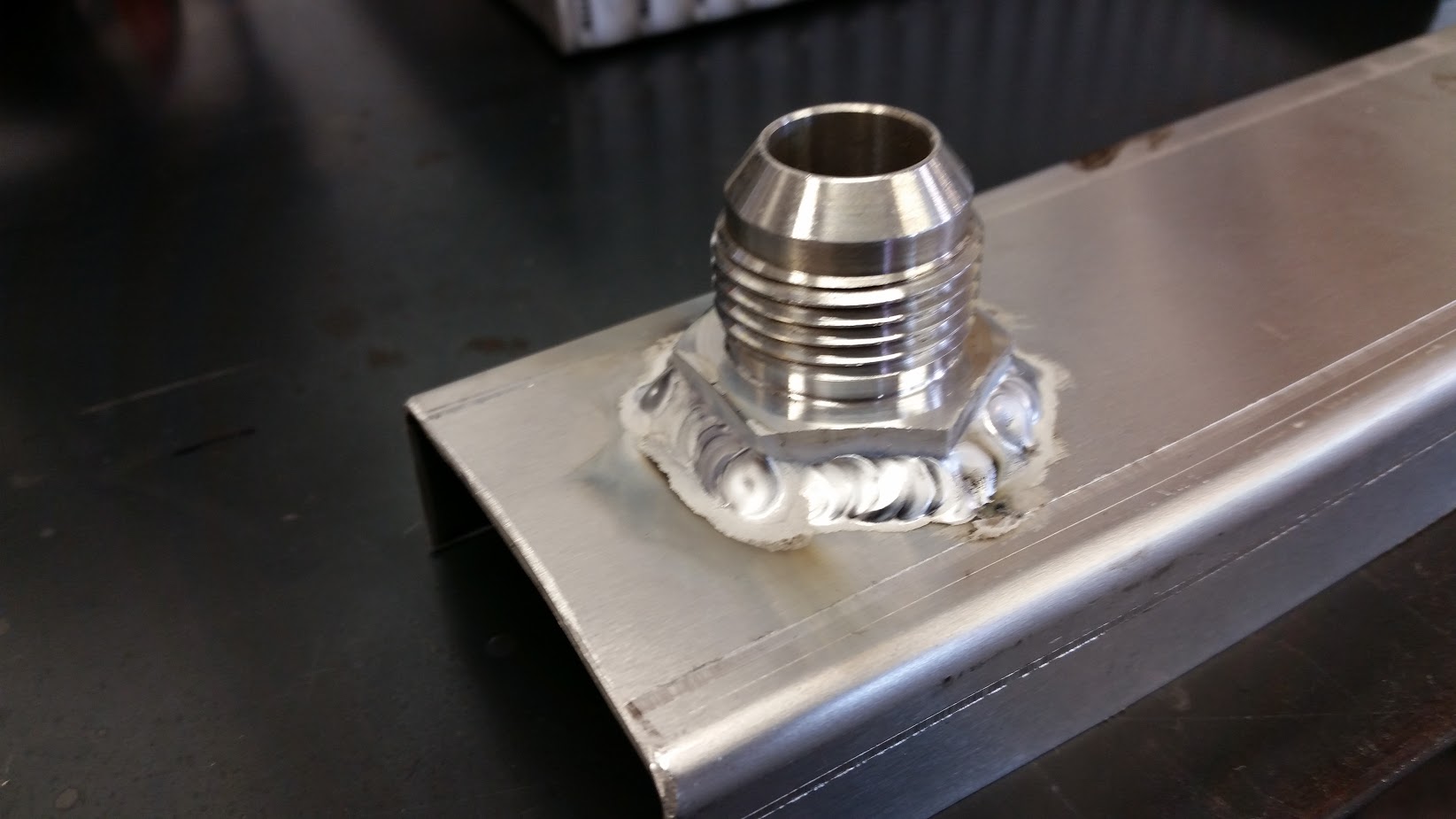
Separating the inlet and outlet tanks on the same side was a little challenging to weld. I had to pump quite a bit of heat into it.
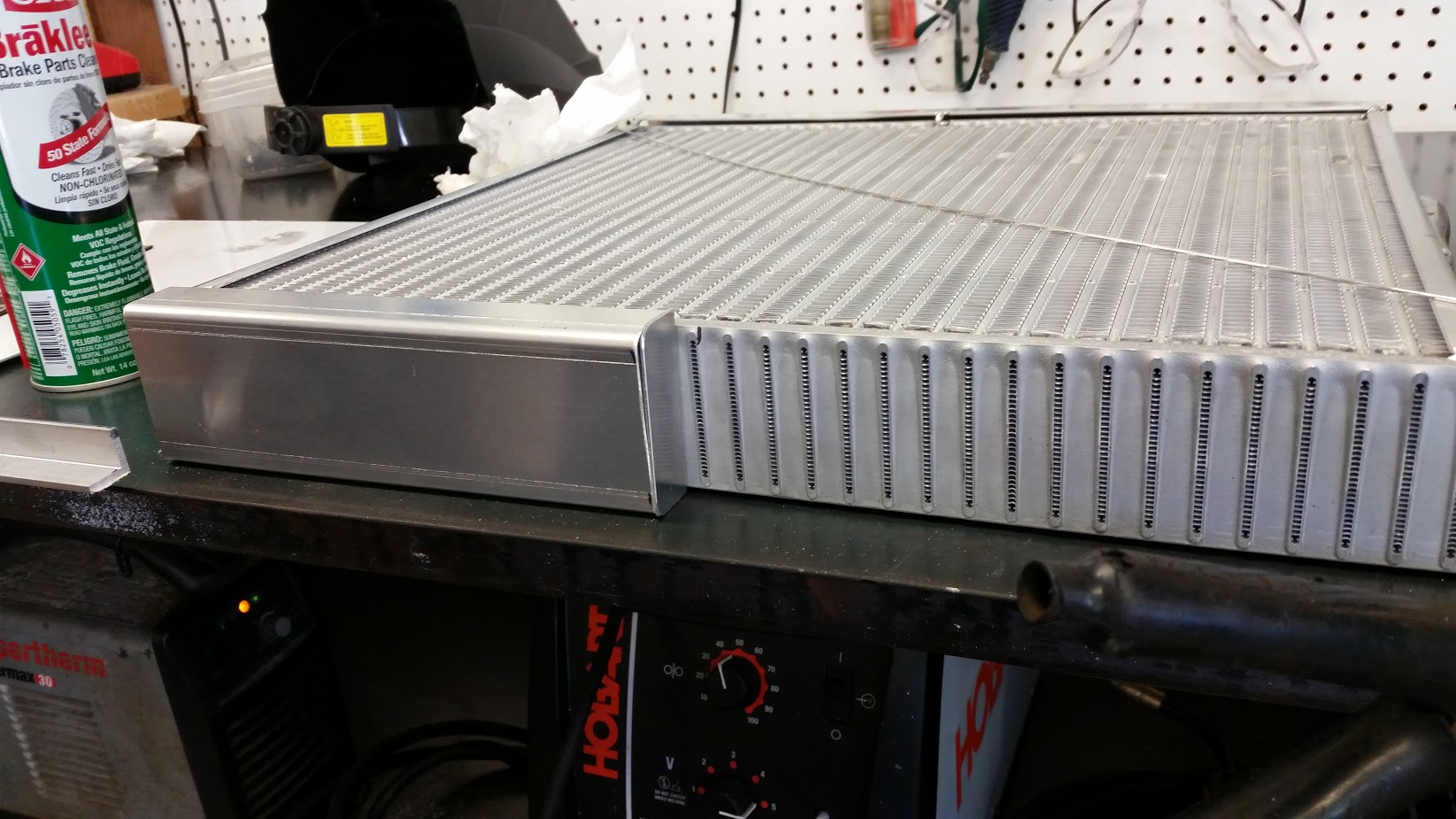

While I was waiting for the welds to cool, I added some gold reflective tape to the bottom of the intercooler. I've never been too sure of its effectiveness but I got it cheap so why the heck not:
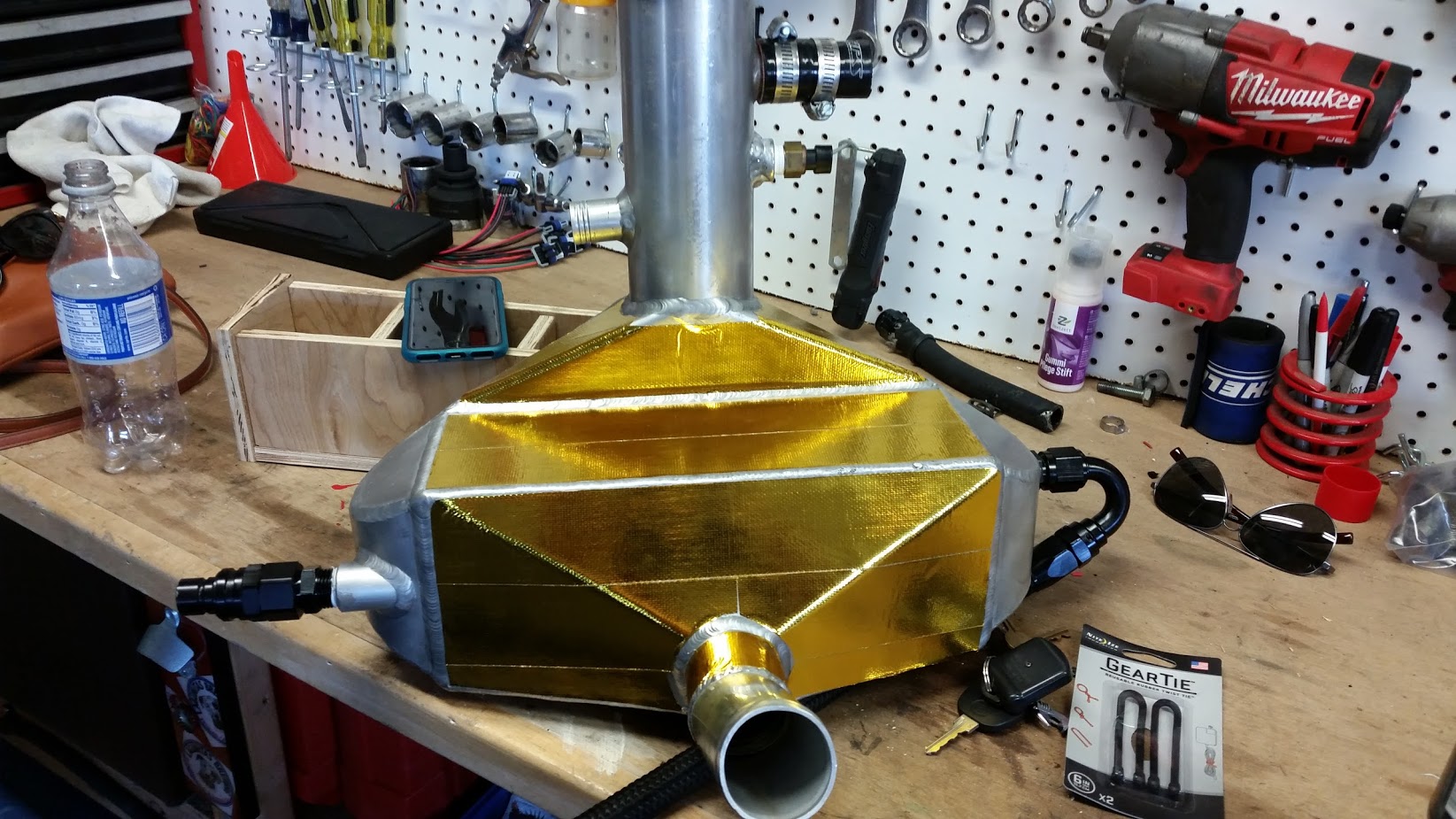
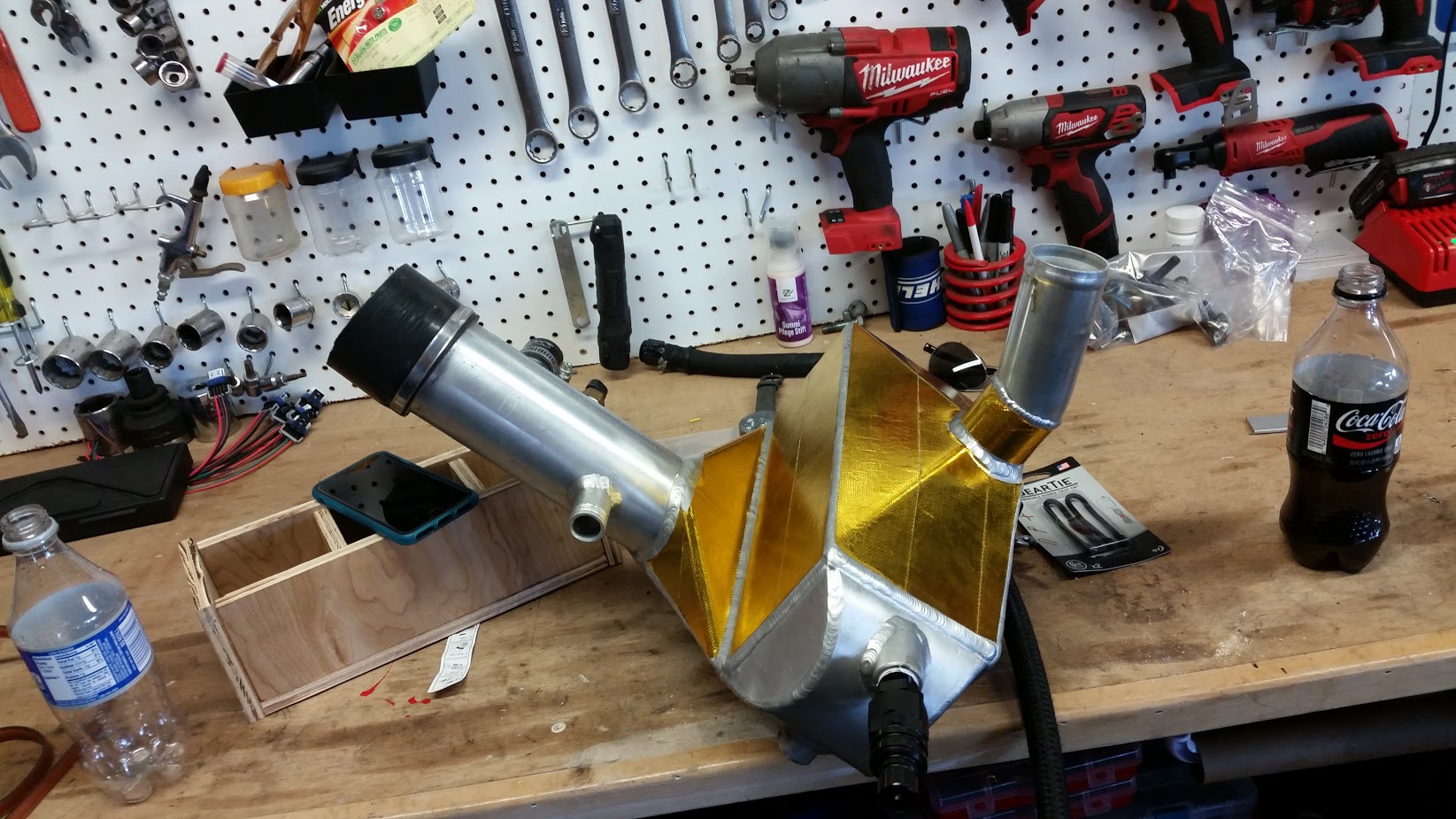
It took a while to chase down some pin hole leaks but I finally got everything to seal with ~20psi of air applied to the drain hole.
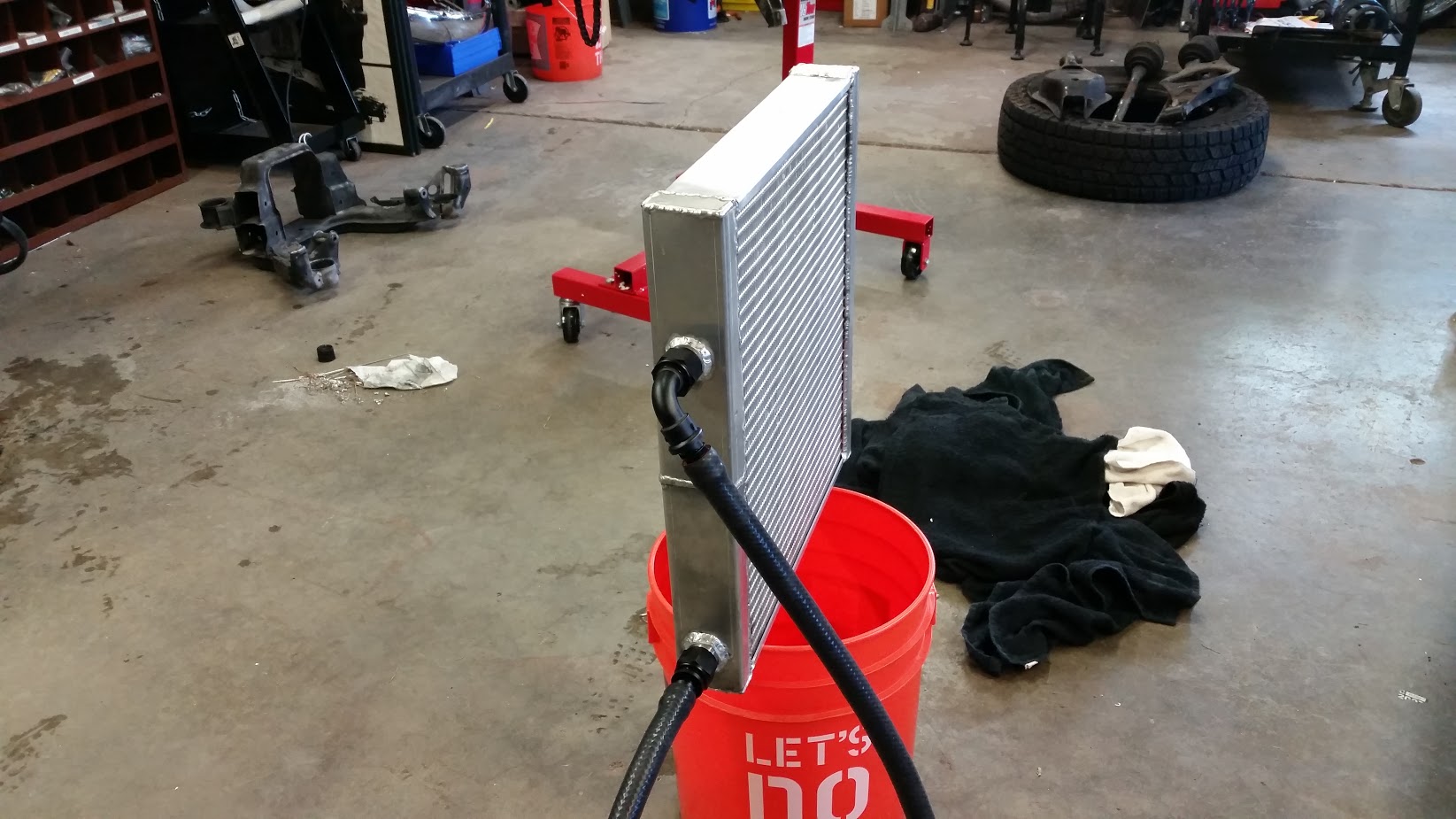
I still need to add a bleed screw to the top of the end tank and then add mounting provisions. Hopefully that gets done this coming weekend. I'll update when I have more to show.