Hidden Rust Area!
When you're doing something in the trunk, take a look at
the license plate light bulb fixtures and check for cracks in the lenses around the mounting screws on the back side of the
fixtures. Also, are the screw heads rusty?
The lens is cracked in several places and the retaining screw
was badily rusted. Since the bulb in the fixture is hard to replace, I suspect it was replaced by removing the fixture and
the screws were over tightened, when the fixture was placed back in position. It's a hard spot to view, without getting down
on your hands and knees.
The hole that the fixture fits in, had started to rust due
to the rusty screw and nut. It is shown here with rust inhibitor applied (left) and with touchup paint applied and the new
lens and hardware mounted back in the hole (right).
I used stainless steel hardware, with small neoprene faucet
washers under the head of the screws and nylon washers under the nuts. This helps seal the screw head against the lens, while
protecting the lens from excessive pressure. The nylon washer keeps the nut from damaging the painted surface. The screw
threads were given a dab of clear nail polish to lock the nut from moving, but allowing future removal.


|
New lens & gasket with stainless steel screws and neoprene washers. |
Replacing
Hood Insulation Pads A dirty, messy job, best done on a cool day. Cover the engine
bay with an old sheet and remove as much of the old pads as you can with 3-inch steel putty knife, being careful not to gouge
the paint underneath. A thin layer of foam and the adhesive will remain... you can't get it all off at once.
I use 3M General Purpose Adhesive Cleaner 08984. I use the quart can and a small sprayer to soak an area the width of the pad
and about 8 to 10-inches high. The smaller 15-oz. spray can product is usually not enough for a complete job, thus the quart
size product. As a side note, this 3M Cleaner is an excellent bug and tar remover, much more effective than most such products,
especially on your front air dam, where we tend to forget about all the stuff that collects there in the summer.
Depending on the temperature, the cleaner will dry pretty
quickly, if it's much above 70 degrees. Keep the sun off the hood. Use a sharp plastic putty knife, which will not scratch
the paint. Final clean-up can be made with some rags or paper towels soaked with the cleaner to get the remaining residue
off.
Make sure you do this work in a well ventilated area,
as the cleaner is pretty volatile!
The factory pads are labeled "Left" and "Right". This
is as viewed from the drivers seat, not as you stand in front of the hood. Be careful with your pad placement... these things
are very sticky and you won't be able to remove or shift the pads position, if you make a mistake.
The process I use, having installed pads on a half-dozen
hoods, is to partially remove the protective backing at the bottom of the pad, about 8 to 10 inches, folding it back to reveal
the sticky backing. While holding the bottom away from the hood, position the top and one side so it is aligned properly,
then carefully allow the pad to come down on the bottom. With the bottom tacked to the hood, fold the top of the pad toward
you and carefully remove the rest of the backing and slowly press the pad in place. I use a 2x4 block to apply firm pressure
to all of the pad surface, to make sure the adhesive is in good contact, especially the edges.
Try doing this first
without the backing removed, so you can see how the pad has to be positioned. Once you are comfortable with handling
the pad in this fashion and getting it positioned properly, partially remove the protective backing and give it a shot. Good
luck!

|
Left and right sides cleaned, center in progress. |

|
New hood insulation pads installed and latches cleaned. |
The new center hood pad appears to be for a 535 series, since
there is a cut-out for the coolent expansion tank cap, which is on the opposite side of where the 528e expansion tank is located.
The part number is the same for both the 535 and 528e center pad, so a 528e center pad appears not to be available.
The front seal strip (top of picture) has also been replaced.
On my '83 there are only three holes in this area for the plastic retainer clips, at the center and each end, while the replacement
seal comes with five clips. Two additional retainers between the center and end retainers. I carefully drilled two 9/32-inch
holes for the additional retainer clips, painting the holes to prevent rust.
How hot is it?
Our E28 coolant temperature gauge doesn't really tell us,
in degrees F, just how hot is the coolant at the various places the needle points? Here's some info Shawn D. and I have developed,
based on our individual tests, that had results that closely match.

UPDATE August 9, 2011
(Link to info about water hose deterioration)
Troubleshooting Temp Gauge or Overheating issues At
this time of the year, E28 questions about engine overheating, temperature gauge accuracy or suspect gauge readings, are very
popular questions. One of the best trouble shooting tools for this, as well as other heat/cold related problems is an accurate
InfraRed Thermometer, such as this Sears Craftsman unit which I've found works well. It is also sold as the Extech 42510 product.
Water Hose Electrochemical Degradation (ECD)
ECD is evident in almost all cooling system hoses, according
to research conducted by the Gates Corporation, as discussed here. However, not very many DIY people appear to know much about this. I have seen this hose problem on quite a few E28s, as
well as on other younger vehicles at this time of year, so I wanted others to know about this and how to properly check hoses
for this problem... before it leaves you stranded!

Used to measure the temperature at the base of the outlet
hose to the radiator (as shown above where the laser pointer is), the meter is indicating 195.0 F degrees (out of focus due
to my camera lens depth of field at F stop used), and the instrument cluster temp gauge is dead center, on my 528e. You
could also measure the radiator output temp at the bottom hose radiator connection and determine if the radiator is functioning
properly, given ambient air temp and fan speeds.
For example, on my car after a thorough warm up and with
an ambient air temp of 82F (27.8C) the InfraRed thermometer reads the following. All
measurements made with the Laser pointer positioned approx. one-inch behind the house clamp and 4-5 inches from the surface
being measured, to insure that the area being tested is not too small or too large and produces accurate and repeatable
results. Different brand InfraRed units may require different measurement positions, depending on their optics.
Upper hose at engine to radiator - 195F (90.6C) Lower
hose at radiator - 145F (62.8C). With AC on - 156F (68.9C)
If you've got a steady hand, you can also read the temperature
of your air conditioned air, by holding the instrument 4-inches from a vent, aiming diagonally at one of the vent blades.
I've confirmed this with my other temperature measuring instruments. And lastly, you can use it to measure inner and
outer tire tread temps, while working to find the best tire pressure at the track, or on the road.
Update July 2, 2013
(updated temps based on tests conducted on additional AC units)
Still, a digital thermocouple probe is easier to use
when measuring air temps and readings are easily repeatable... certainly if you're monitoring air conditioner performance
while driving. Remember, your readings may be slightly different then mine, but I wouldn't expect to see major variations
(more than 15%) on a system working properly, such as my old R12 system performance, as shown below on my old RadioShack Thermometer
below (less than 1% difference compared to my Fluke 8060A/80T-150UA thermocouple reading), using its external temp probe placed just inside the AC vent while driving. It shows a reading of
40.3F, while the outside temp was 91F. I've used the RadioShack Thermometer on a large number of air conditioners (home and
auto) because it is much smaller then my much larger two piece Fluke 8060A/80T-150UA and easier to carry around.
The term 'it blows cold' is meaningless, as
I 've shown a number of people, several just in the past few weeks. 55-60F may feel cold on your hand or fingers if it is
in the mid 90's outside, but it isn't enough cold from an E28 AC system, or any AC system for that matter! These
temps are 40% to 50% warmer than the system should be producing at maximum cooling, which is typically 40F. In such cases,
your AC is not working properly and should be fixed, if 55-60F is its output air temp, AS MEASURED,
not what it might feel like to you, with your hand placed in front of the AC vent. In fact, most AC Techs consider
(rule-of-thumb) an AC system that can't produce air colder than 45F (7.2C) as having a problem, or certainly a borderline
system.
Measured minimum AC outlet air temp at 94F outside, recirculation air
mode, no outside air intake. Operating at 55 MPH, Fluke Thermocouple.
1983 BMW 528e R12 - 40.3F (4.6C)
1988 Chevy K1500 R134* -
43.1F (6.2C)
2002 VW Golf TDI R134 - 39.7F (4.3C)
2008 Honda Fit Sport R134 - 41.7F (5.4) Update July 2, 2013 2003 VW Golf TDI
R134 - 38.5F (3.6C)
* Originally an R12 system
converted to R134.
Circuit modified for manual control of outside air door, to stop faulty automatic use of hot outside air and only recirculate
inside air, which produces greater cooling.
The InfraRed thermometer will give you a clear indication
of what your cooling system problem may be... bad gauge temp sensor? Faulty or erratic thermostat? Faulty fan clutch? Partially
clogged radiator? Bad aux fan sensors or relays? Faulty gauge electrical ground? Faulty engine block ground(s)? Faulty instrument
cluster component or ground?
It greatly simplifies troubleshooting and you're likely
to know somebody who has an InfraRed thermometer you can borrow. If not, a good quality food thermometer probe will also work,
with the probe held firmly against the hose at the location shown above, used by the infrared thermometer.
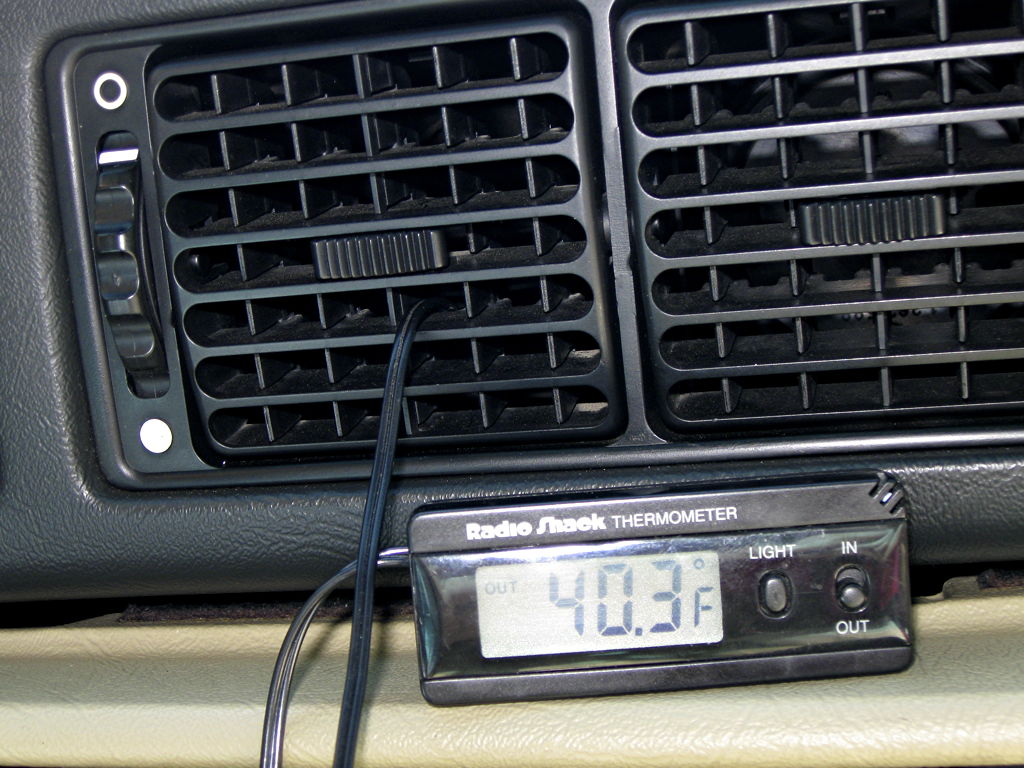
Replacing old sensors can solve intermittent problems.
If you're experiencing random and intermittent problems,
such as warm or cold hard starting, poor cold or warm idle, rich idle, cold or warm stumble and other such problems, check
the age of your coolant sensors. Like mine, they may be original units with many years of operation and are now not functioning
properly all the time and have become intermittent. Mine exhibited erratic DVM readings at various temperatures, when
measured at different times. The four sensors shown below near the fuel pressure regulator are what should be replaced, especially
if intermittent problems are the issue.
Don't forget to apply a high quality contact cleaner and protective chemical, such as
the CAIG Labs products, to the sensor contacts and sensor cable connector contacts. You will save yourself a lot of frustration
and vehicle downtime, if you treat all electrical connectors and ground connections on your E28. Believe me, I know from decades
of experience on E28s!

UPDATE July 25, 2008
And what sensors do what and which one is which?
I have received a surprising amount of Email this week, as
it seems faulty sensors may be the cause of poor running and over heating problems, thanks to our current weather. Unfortunately,
there doesn't appear to be much help for identifying the various sensors, as most photos are very poor. The following should
help.

|
- CLICK TO EXPAND PICTURE - |

|
- CLICK TO EXPAND PICTURE - |
I comment on the Coolant Temp Sensor for the dash temp gauge,
having its signal pass through the Service Interval Processor, because I've seen this path create some temp gauge problems
due to poor or oxidized connections along this path, which involves six (6) connections, when the actual sensor was operating
correctly! The sensors are, of course, the same in the 325e, with the exception of their connecting wire color codes.
Placement of rear Jack Stands
Placement of jack stands
at the rear of the E28 still appears to be a question, especially with new E28 owners. One such person pulled into my driveway
yesterday, having seen my 528e with her backside high in the air. He wanted to know where I put the jack stands, as he wasn't
comfortable about the using the rocker panel pads. I don't trust these, either, except for changing a tire.
I prefer the method often suggested by Shawn D. (MyE28.com)
and several others, of using the rear axle carrier mounting bolt head, where the push strut is also attached. (see Bentley
17-2) The pictures below show where. Using a wooden block (2x3 or 2x4) to contact the bolt head and the push strut flange.

|
View from the front of the rear wheel well. |

|
View from rear wheel well, looking forward. |
UPDATE April 15, 2008
Front Strut Water Drain
I've expanded on this subject, as a local BMW friend
recently had a strut failure, due to a rust problem. Since this is now the 4th such failure I have observed, I think maintenance
of this area deserves more comment.
When doing maintenance on the front end (checking/changing
brake pads, rotating tires, refreshing the brake fluid and bleeding the brakes, etc.), don't forget to check that the strut
spring perch small water drain hole is clear and permits the water to run out. A lot of junk can collect in the bottom of
the spring perch area and trapped water will certainly cause rust and eventual failure of the tube or perch.

|
Small nail being used to check the drain hole at the rear of the strut. |
Check the bottom of the spring perch cone/bowl by running
your fingers around the bottom and removing any small rocks or dirt that you find, so that the water drain hole doesn't become
clogged.
Shown below, is a small hose I use, adapted to my shop vacuum to suck out
anything at the bottom of the bowl. I 've used compressed air, but it tends to cause the debris to simply move around the
bottom to the other side. You're likely to have more luck using a garden hose, as the water will carry the debris away.
And what happens if the strut spring perch bowl is full of junk at the bottom and the
drain hole has been plugged for some time, allowing rust to do its dirty work?
The bottom of the spring perch cone/bowl has rusted through,
allowing the spring perch to slide down the strut tube and the spring perch is now on top of the tire! Luckily,
this happened to my friend at a very low speed and within several blocks of his house, so it was possible to nurse the car
home. The other pictures show the spring perch from different angles...

|
The front side of the strut. |

|
Looking up at the strut from the ground. |
We looked at the left side (drivers side) strut and the spring
perch bowl has a fair amount of dibris in it, with the water drain hole clogged. My suggestion is to replace this side too,
which he is going to do. Check your strut spring perch bowls, too, and watch out for excessive rust, which can make for
a bad day. I am going to have him derust and paint the bottom of his spring perch bowls, when his used replacement strut tubes
arrive. You should consider doing the same thing, especially if you're installing different springs or shock absorbers and
have these off the car, as part of the process.
New Sensors Installation
New sensors installed as a preventive maintenance step, replacing
original 23 year old sensors. Note that there is no metal cover on this October 1982 build 528e and that 5mm hex head bolts
are used... making it difficult to get my torque wrench on it with the anti-sway bar in the way. I have to add a ball-head
5mm hex head socket to my tool list... or replace these with hex head bolts. I've used a yellow cable wrap at both
ends of one sensor, to identify it, as I didn't have a gray one to replace the original gray cable wrap.
Lastly, if you have some erratic running issues that have been difficult to resolve,
pull each sensor and see if it is clean, or has what appear to be small metal shavings on it. Clean the metal particles off
of them, replace and see if this corrects your erratic running problems.

|
Sensors at left side of bell housing |
- Swap the seats and help minimize wear
- A tip about using Gummi Plfege
- Door doesn't latch right without additional force and rattles
- Modified jack pad to prevent damage when lifting the E28 at side lift points under the
rocker panels.
HOME
Mods & Resources Pg. 1
Mods & Resources Pg. 2
Shelley's Autos
The Earlier Years
|